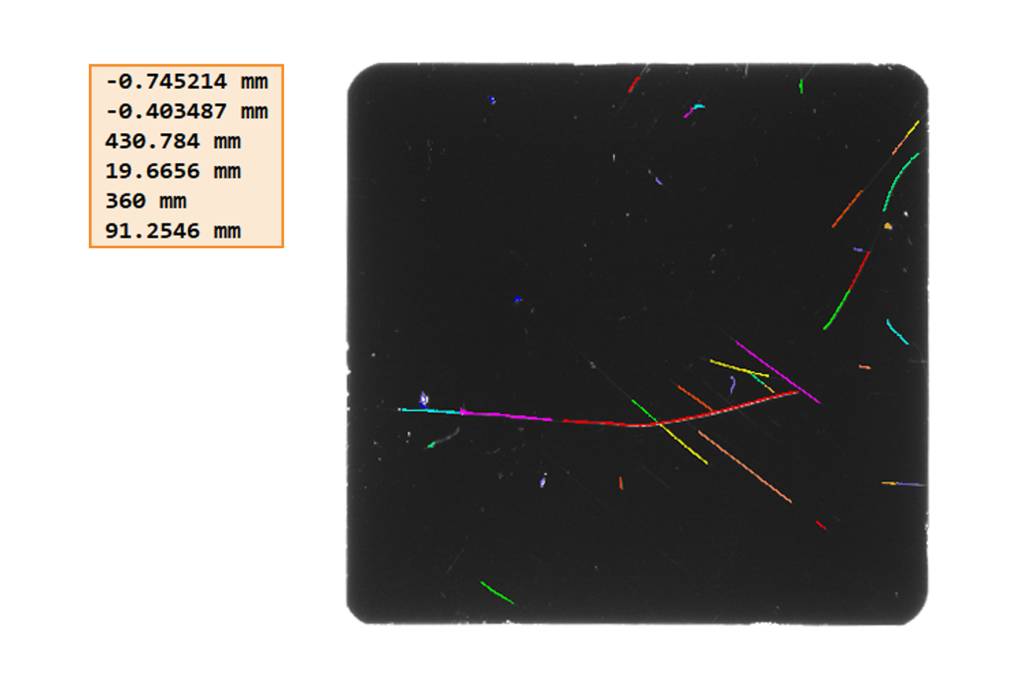
Akeoplus mit Sitz im französischen Château-Gaillard wurde im Jahr 2006 gegründet und unterstützt Kunden aus verschiedenen Branchen mit Anwendungen zur Verbesserung von Industrierobotern. Im Rahmen seiner Robotiklösungen nutzt das Unternehmen Bildverarbeitungssysteme und Algorithmen.
Akeoplus hat im Auftrag des Thales-Alenia-Space-Standorts in Cannes, Südfrankreich, eine Roboteranlage entwickelt. Thales Alenia Space ist ein weltweit tätiger Raumfahrtkonzern, der Lösungen für Telekommunikation, Navigation, Erdbeobachtung, Umweltmanagement, Exploration, Wissenschaft und Orbitalinfrastrukturen anbietet. Die Ingenieure von Thales Alenia Space haben ein Klebeverfahren entwickelt, mit dem die Platzierung optischer Solarreflektoren (OSR) automatisiert und gleichzeitig die thermische Leistung und das Gewicht erhöht werden können. Die Mitarbeiter von Akeoplus arbeiteten anschließend mit den Teams von Thales Alenia Space zusammen, um eine Roboterlösung für einen Herstellungsprozess von Satelliten-Panels zu entwickeln.
In der Anlage mit dem Namen Solar bringen Roboter optische Solarreflektoren (OSR) auf Satelliten-Panels an. Die Aufgabe in der Entwicklung bestand darin, die Roboter unter Reinraumbedingungen zu befähigen, die OSR auf dem 6x3m großen Panel mit einer Genauigkeit von unter 0,2mm anzubringen. Das Verhältnis der Positioniergenauigkeit zur Größe des Arbeitsbereichs beträgt 1:40.000. Um die Anforderungen zu erfüllen, setzte Akeoplus auf die Machine-Vision-Software Halcon von MVTec, die bei Inspektionstätigkeiten und der Ausrichtung der OSR unterstützt.
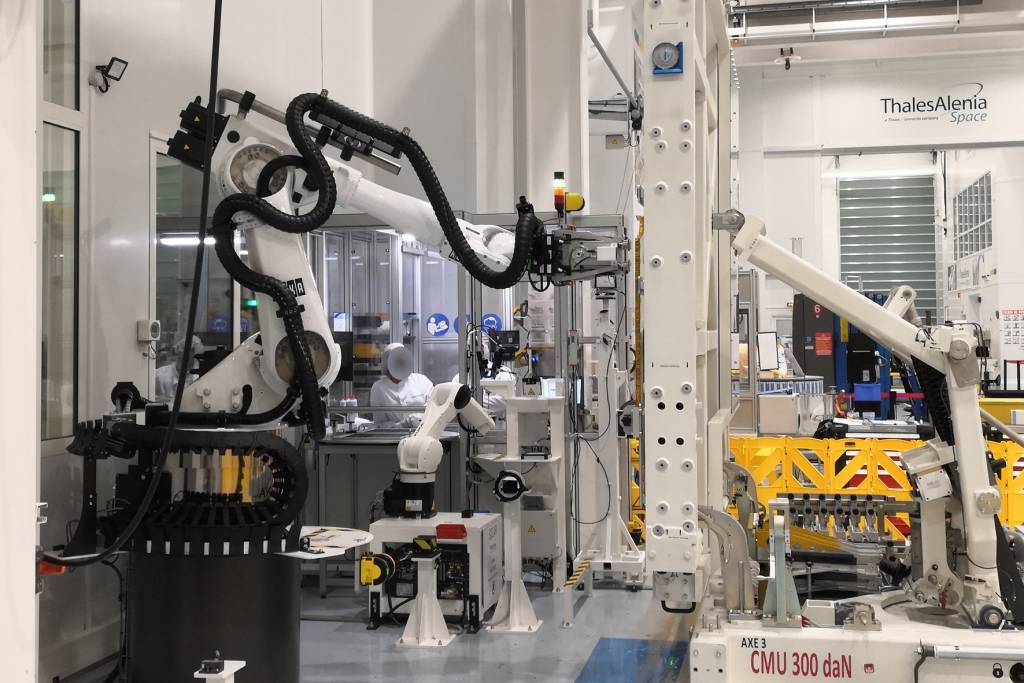
Entlastung der Mitarbeiter
Optische Solarreflektoren werden in der Raumfahrt genutzt, um z.B. Satelliten in geostationären Umlaufbahnen vor den dort herrschenden hohen Strahlungswerten zu schützen. Ein entsprechendes Panel als Außenwand ist mit bis zu 7.000 Reflektoren ausgestattet, wobei ein OSR eine Größe von 40x43mm aufweist. Bislang wurden die OSR auf dem Panel rein manuell aufgebracht. Zwei oder mehr auf Matten liegende Monteure hatten die Aufgabe, mit nach unten gestreckten Armen die OSR-Bauteile zu positionieren und deren Ausrichtung sicherzustellen.
Zwei Roboter arbeiten mithilfe von Machine Vision autonom
Für den neuen automatisierten Produktionsprozess hat Akeoplus gemeinsam mit Thales Alenia Space die Roboterzelle Solar entwickelt. Darin befinden sich zwei Roboter sowie ein Positioniertisch, auf dem die Satellitenpanels einzeln aufliegen. Für die genaue Führung ist ein Laser-Tracker für den Sechsachs-Roboterarm zuständig und für die industrielle Bildverarbeitung werden hardwareseitig drei hochauflösende 2D-Kameras eingesetzt. Die Bildverarbeitungssoftware Halcon ist für die Qualitätsprüfung des OSR, die Feinpositionierung, das Human/Machine-Interface und die Visualisierung zuständig.
Der Fertigungsprozess läuft wie folgt: Der kleinere und schnellere Roboter entnimmt einen OSR aus der Ablage und legt ihn auf eine Vakuum-Hintergrundbeleuchtung unter der ersten Kamerastation. Die Kamera nimmt ein Bild auf, das mithilfe von Halcon auf Bruchstellen und Kratzer untersucht wird. Außerdem wird mithilfe der Machine-Vision-Methode Shape Matching die exakte Position des OSR ermittelt sowie geprüft, ob das Bauteil in Größe und Form auch dem laut Bauplan vorgesehenem Modell entspricht.
Die Positionsbestimmung ist deshalb so wichtig, weil der Roboter jeden optischen Solarreflektor ein klein wenig anders greift. Daher wird der OSR mittels Machine Vision ausgerichtet, um ihn mit einer Genauigkeit von rund 0,2mm zum nächsten Produktionsschritt weiter zu transportieren. Wenn das Bauteil Ok ist, wird es unter die Düse des Klebstoffspenders abgelegt. Nachdem der Klebstoff aufgetragen wurde, nimmt der kleinere der beiden Roboter den OSR wieder auf und legt ihn auf einer festgelegten Stelle ab, damit der größere Roboter diesen für die weitere Bearbeitung greifen kann. Der Roboter mit dem größeren Arbeitsraum verfährt nun das Bauteil vor die nächste Bildverarbeitungsstation, wo die zweite Kamera Bilder des aufgetragenen Klebstoffs aufnimmt. Das eingezogene Bild des Klebemusters wird von Halcon analysiert. Dabei wird geprüft, ob der Klebstoff gleichmäßig verteilt ist und ein ganz bestimmtes Muster einhält, das die Thermotechniker von Thales Alenia Space entwickelt haben und das genau reproduziert werden muss. Anschließend erfolgt die genaue Ausrichtung des OSR am Arm des Roboters. Das ist der erste Schritt, um den Reflektor genau an der vorgesehenen Stelle am Satellitenpanel anbringen zu können. Dazu nimmt die dritte hochauflösende Kamera wiederum Bilder des OSR auf. Die Ausrichtung erfolgt, indem die Algorithmen von Halcon die räumliche Transformation zwischen den äußeren Kanten des OSR und dem Koordinatensystem des Greifers, der den OSR mit einem Vakuum-Greifsystem hält, bestimmen.
Die Ecken des OSR werden durch die Schnittpunkte der Kanten ermittelt. Daraus abgeleitet lässt sich ein Koordinatensystem definieren, bei dem die Ecke des OSR zentriert und an die Kanten des OSR ausgerichtet ist. Das Koordinatensystem des Effektorroboters wurde im Vorfeld durch eine Hand/Augen-Kalibrierung des Roboters bestimmt. Die Bestimmung der Koordinatensysteme ist aus zwei Gründen wichtig: Zum einen für die 3D-Ausrichtung. Es kann sein, dass der Reflektor am Greifer gekippt ist. Daher werden die Ecken des OSR mit der dem Effektor abgeglichen, wobei jede Ecke bekannt ist und somit als Referenzpunkt fungiert. Dadurch können auch geringe Neigungen oder Verschiebungen ausgeglichen werden. Zum anderen dient die Ecke des OSR als Referenzpunkt zum Anbringen auf dem Panel.
Iteraktiver Rückkopplungsprozess
Da der 2,4m lange Greifarm des Roboters allerdings nicht 100-prozentig genau ist, die Reflektoren aber mit einer sehr hohen Genauigkeit angebracht werden müssen, gilt es, die Ungenauigkeiten auszugleichen. Mit Unterstützung des Laser-Trackers und der Bildverarbeitungssoftware Halcon hat Akeoplus einen iterativen Rückkopplungsprozess entwickelt. So gelingt es dem Roboter, den OSR mit der geforderten Genauigkeit an der exakten Stelle an dem 18m2 großem Panel anzubringen.