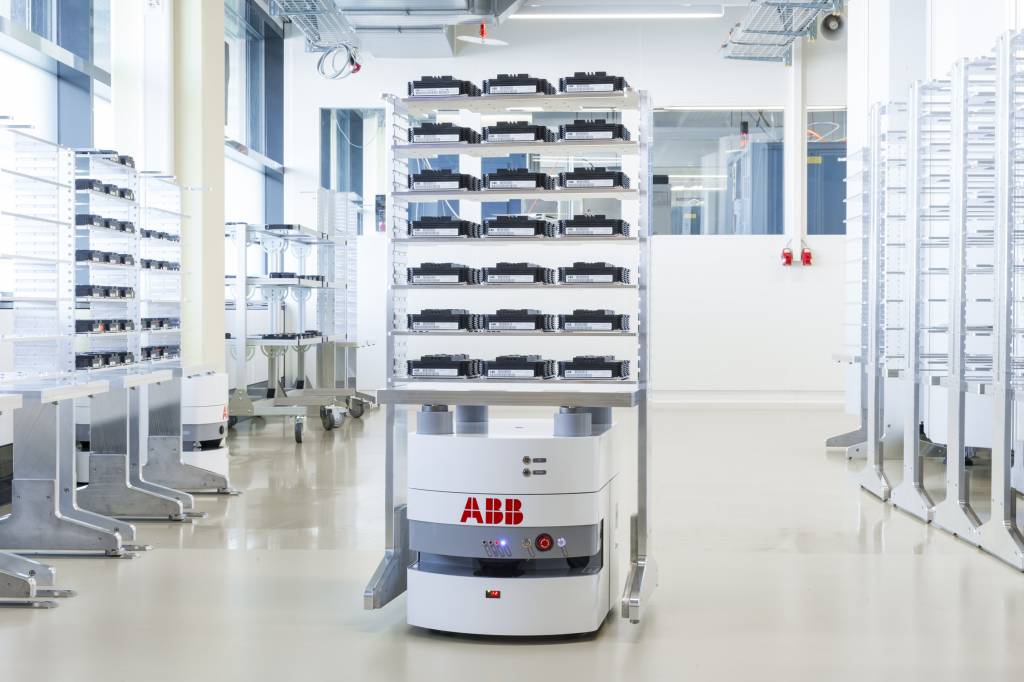
Da der diskontinuierliche Backend-Prozess als besonders geeignet ausgemacht wurde, begann Hitachi ABB Power Grids hier mit der Automatisierung. Das zugehörige Programm mit dem Namen Genesis startete im Jahr 2014: über 100 Teilprojekte, 20 neue Produktionseinheiten, mehr als 50 Roboter und zunächst sechs fahrerlose Transportfahrzeuge (engl. AGV) mussten schrittweise in das Manufacturing Execution System (MES) integriert werden.
Zum Testen entstand eine Pilotanlage mit echten Produktionszellen und Betriebsmitteln sowie vier fahrerlosen Einheiten und mehreren ABB-Robotern. Sie umfasste bereits alle vorgesehenen Elemente im kleinen Maßstab, sodass Hardware, Software und Schnittstellen getestet werden konnten. Erprobt wurde auch die Kommunikation sowie die mechanische Übergabe zwischen den AGVs und der Produktionsausrüstung.
Automatisierter Produktionsprozess
Das endgültige Programm umfasst mehrere automatisierte Produktionszellen. Die Logistik übernehmen speziell entwickelte Einheiten, die mittels Autonomous Navigation Technology (ANT) von BlueBotics angesteuert werden. Das System nutzt ortsunveränderliche Umgebungsobjekte als Bezugspunkte für die Fahrzeuglokalisierung. Zudem kombiniert es Informationen aus den Encodern und Laserscanner der mobilen Einheiten zu einer Positionsgenauigkeit von ±1cm bzw. ±1°. Bei einem plötzlich auftretenden Hindernis können die AGVs eigenständig anhalten. Eine feste Verbindung zwischen den einzelnen Zellen kann daher zugunsten einer variablen Streckenführung entfallen.
Die Koordinierung des gesamten Ablaufs erfolgt über das MES und ein Leitsystem, das ABB Ability Manufacturing Operations Management (MOM). Im Gegensatz zu herkömmlichen Automatisierungslösungen, wo der Materialfluss fest in der Zelle programmiert ist, wird hier die Geschäftslogik ins MES verlagert, die somit ohne Ändern der Programmierung in den Roboterzellen flexibel angepasst werden kann.
Bescheidene Anfänge
Eine der wichtigsten Voraussetzungen ist die Produktionsleittechnik des MES. Dieses System behält den Gesamtüberblick und koordiniert alle Vorgänge. Für die Logistik zwischen den Zellen kamen mehrere Möglichkeiten infrage. Erst wurde ein herkömmliches Transportsystem, dann eine Deckenförderbahn erwogen – beides wurde verworfen. AGVs haben es hingegen ermöglicht, die gesamte Anlage zu automatisieren, obwohl ursprünglich nur die Automatisierung eines Teilbereichs geplant war.
Komplexer Prozess als nahtlose Abfolge
Die Halbleiterherstellung ist prozesstechnisch sehr komplex und stellt hohe Anforderungen an die Rückverfolgbarkeit. Geht etwas schief, muss nachvollziehbar sein, welche Maschinen und Materialien involviert waren. Alle AGVs zu integrieren, war schwierig, denn die Produktion in Lenzburg umfasst viele Einzelschritte, über die das MES informiert sein muss. Die AGVs müssen also zuverlässig mit der Produktionsausrüstung kommunizieren. So bestand die größte Hürde für die Fahrzeuge in der Interaktion mit der Produktionszelle. Der automatische Transport der Bauteile-Kassetten erforderte ein spezielles Verfahren sowie die Koordination und Synchronisation mit der Ausrüstung und dem MES. Demnach mussten spezielle, in dieser Branche übliche Handshake-Protokolle implementiert werden.