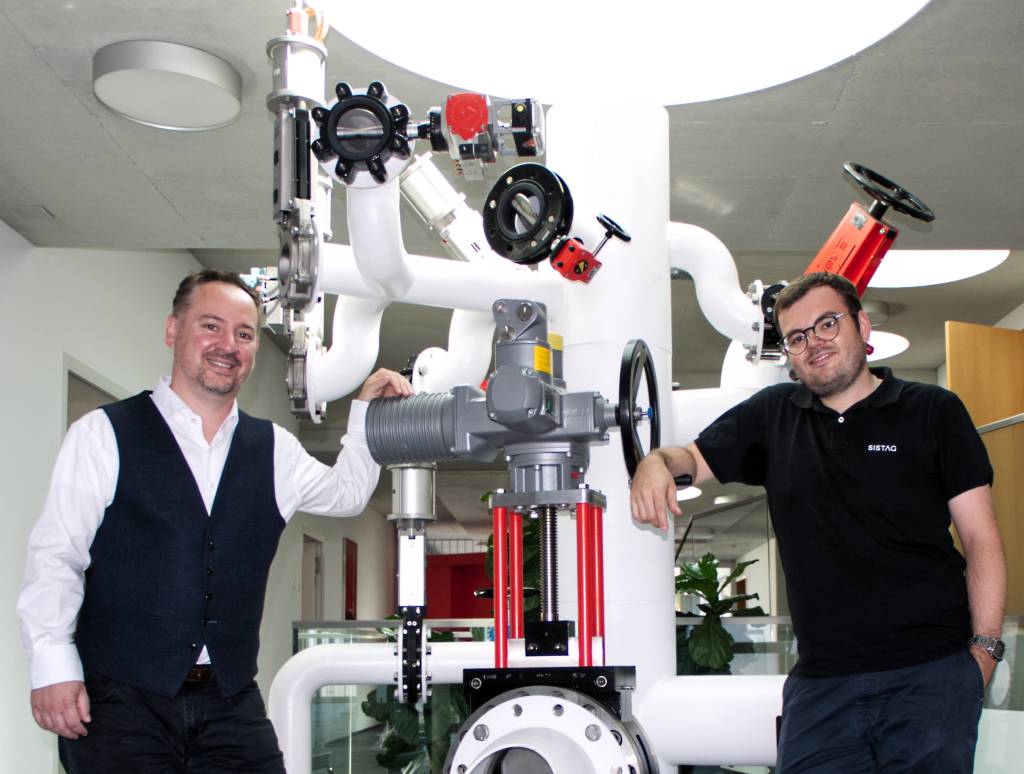
Das weltweit agierende Unternehmen Sistag stellt Armaturen für die Wasserversorgung und Industrie her. „Darüber hinaus sind wir auf Flachplattenschieber spezialisiert, die unter dem Markennamen Wey Valve bekannt sind und u.a. in der Petrochemie, Ölförderung und im Bergbau eingesetzt werden. Unsere mechanische Fertigung hier am Standort stellt mit rund 165 Mitarbeitern pro Jahr rund 20.000 Schieber her“, erklärt der Leiter Fabrikation Manuel Schmidlin.
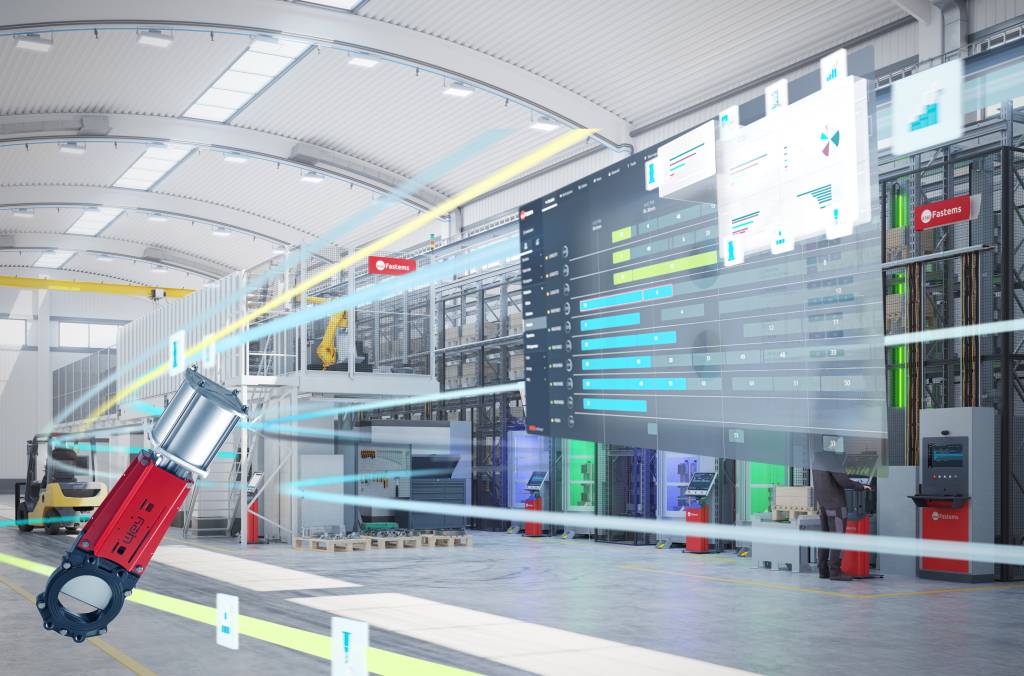
Modernisierung mit Fokus auf Digitalisierung
Wie viele andere Schweizer Klein- und mittelständische Unternehmen (KMU) sieht sich auch Sistag mit Sitz in Eschenbach (Kanton Luzern) mit hohen Kosten konfrontiert. Um weiterhin wirtschaftlich zu bleiben, müssen die Maschinen quasi non-stop laufen. Die Gehäuse als Kernkomponente für die Flachplattenschieber werden auf zwei horizontalen Bearbeitungszentren gefertigt. 2005 investierte der Betrieb in ein flexibles Fertigungssystem von Fastems: ein Multi-Level-System (MLS), angebunden an eine OKK HM 630. Das System wurde 2010 auf eine Gesamtlänge von 35m erweitert und eine zweite OKK gleichen Typs kam hinzu.
2022 entschloss sich Sistag, das MLS zu modernisieren. „Das Betriebssystem der Steuerungssoftware sowie die entsprechende Elektronik liefen noch auf 32Bit und waren im Prinzip ‚End of Life‘. Im Zuge der Umrüstung auf ein 64Bit-System nahmen wir dann ein komplettes Retrofit sowohl steuerungsseitig als auch mechanisch vor“, geht Schmidlin ins Detail. Da Sistag zudem seit rund vier Jahren eine konsequente Digitalisierungsstrategie verfolgt, wurde nicht nur das FFS softwareseitig mit der Manufacturing Management Software (MMS) von Fastems auf den aktuellen Stand gebracht, sondern das Augenmerk insbesondere auf die Digitalisierung der gesamten Produktion gerichtet. Übergeordnetes Ziel dabei ist, mit der MMS als zentrales Manufacturing Execution System die gesamte Produktion zu steuern.
‚Terra Incognita‘ in der Fertigung
Die MMS von Fastems bietet hierzu sämtliche Voraussetzungen, denn sie zählt derzeit wohl zu den leistungsfähigsten Lösungen zum Planen, Ausführen und Überwachen einer automatisierten spanabhebenden Fertigung. Die MMS plant automatisch die Produktion bis zu 96 Stunden im Voraus und berücksichtigt hierbei sämtliche erforderlichen Ressourcen wie Rohmaterialen, NC-Programme sowie Werkzeuge inklusive deren Standzeiten. Manuel Schmidlin weiß allerdings nur zu gut, dass für eine durchgängig planbare Fertigung auch Stand-Alone-Maschinen, manuelle Arbeits- und Prüfplätze etc. in die Digitalisierung einbezogen werden müssen. Keine einfache Aufgabe, denn diese Bereiche sind bislang oftmals noch eine ‚Terra Incognita‘ in der Fertigungsorganisation.
Das soll sich bei Sistag mit der Implementierung des MMS-Softwaremoduls WCO ändern. „Wir wollen den gesamten Produktionsfluss in der MMS abbilden und hierbei jeden einzelnen Schritt – vom Zuschnitt auf einer Lasermaschine über das Hobeln, Fräsen, Bohren und Schleifen bis hin zur Qualitätsprüfung – mit einbeziehen“, erläutert Schmidlin. WCO steht für ‚Work Cell Operations‘ (Arbeitszellen-Operationen) und ist eine Lösung, mit der sich auch nicht-automatisierte Maschinen und Arbeitsprozesse digitalisieren lassen. Das Modul erlaubt es hierbei u.a., die Kapazitäten und Arbeitsreihenfolgen von Einzelmaschinen sowie Arbeitseinheiten (Zellen) zu organisieren und deren Auslastung zu erfassen.
Vollständige Integration
Schmidlin vermittelt einen konkreten Eindruck von den Potenzialen des MMS-Moduls: „Jedes WCO steht für eine Stand-Alone-Maschine oder einen Arbeitsplatz, wobei sich auch mehrere Maschinen in einem WCO gruppieren lassen. So haben wir beispielsweise die Drehmaschinen einer Abteilung in einem WCO zusammengefasst. Innerhalb der WCO-Gruppierungen können wir dennoch die Aufgaben an jeder Maschine verteilen und koordinieren. Alle weiteren netzwerkfähigen Stand-Alone-Maschinen werden ebenfalls direkt mit der MMS verbunden. Darüber hinaus haben wir aber auch ältere Maschinen, z.B. Metallhobel, die sich als vergleichsweise einfache Fertigungslösungen ebenfalls für die Einbindung in die Gesamtorganisation mit den WCOs anbieten. Weil die Maschinen nicht netzwerkfähig sind, erhalten die Mitarbeiter ein Tablet, um die erforderlichen Produktionsdaten und Infos an die MMS zu übertragen.“