Abb. 3 zeigt die Marktanteile der aktuell angebotenen Bauformen von CNC-Bearbeitungszentren für die Holzbearbeitung.
Bei der Analyse der Marktanteile lässt sich feststellen, dass nun deutlich mehr Bearbeitungszentren mit festem Portal (Tischbauweise) angeboten werden und mit 43% nun den größten Anteil ausmachen. Während 2007 noch Auslegermaschinen den ersten Platz belegten waren anschließend Maschinen mit Fahrportal (Gantrybauweise) dominierend. Im Unterschied zum Fahrportal ist bei der Tischbauweise der Maschinentisch nicht fest, sondern kann das Werkstück entlang der x?Achse positionieren. Insbesondere bei der Plattenbearbeitung wird hierdurch eine hohe Flexibilität ermöglicht, da große Spannweiten und Verfahrwege realisiert werden können. Zudem ist ein schneller Transport zwischen Lagerort und dem Bearbeitungszentrum automatisiert realisierbar. In Abb. 4 ist der Maschinenpreis den jeweiligen Maschinenbauformen gegenübergestellt. Hierbei wird vor allem deutlich, dass die Gantrybauweise in allen Preisklassen vertreten ist. Währenddessen Maschinen in Tischbauweise, die in dieser Umfrage den höchsten Marktanteil ausmachen, nur im mittleren Preissegment vertreten sind.
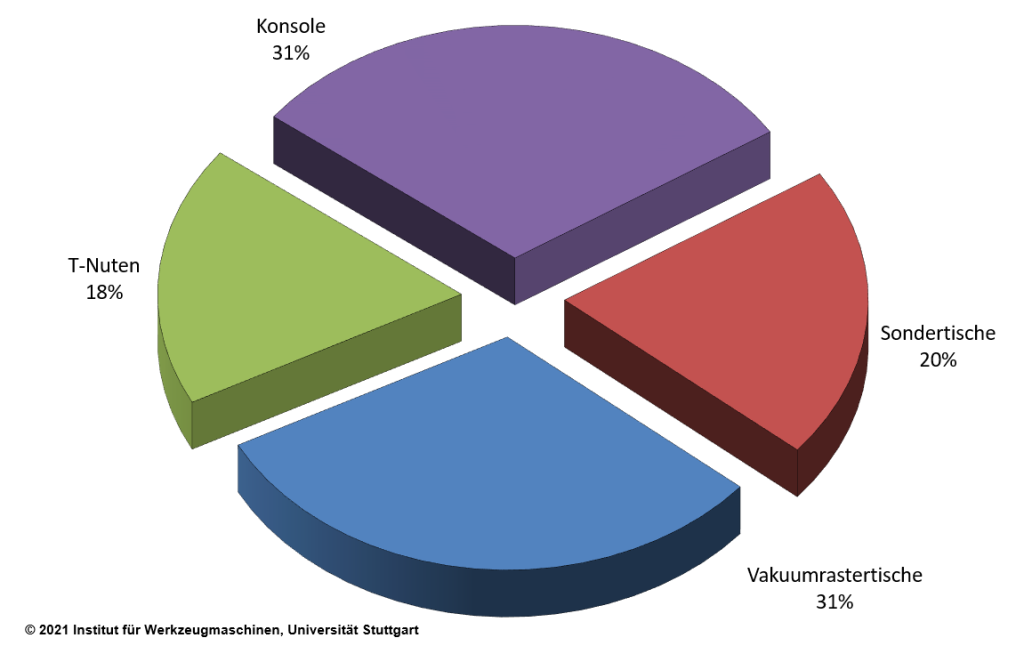
Tischkonzepte und Spannsysteme
Aufgrund des breiten Spektrums von Werkstückgrößen und -formen in der Holzbearbeitung, hat sich ein vielseitiges Angebot von Tisch- und Spannsystemen etabliert. Dabei stellt jeder Anwendungsbereich andere Herausforderungen an die Werstückspannung. In Abb. 5 sind die Anteile der für die Maschinen verfügbaren Tischkonzepte zusammengefasst. Dabei ist festzustellen, dass sich die Verteilung über die letzten Jahre nahezu konstant gehalten hat. Die Bearbeitung von Türen, Platten sowie das Nesting fordern spezielle Spannsysteme zum Spannen von plattenförmigen Werkstücken, während in der Fenster- und Treppenbearbeitung aufgrund der prismatischen Werkstücke andere Lösungen zur Fixierung der Werkstücke gefordert sind. Als Tischkonzepte in Bearbeitungszentren werden Vakuumraster- und Konsolentische mit Anteilen von jeweils 31 % angeboten. Diese eignen sich besonders zum Spannen von plattenförmigen Werkstücken, können aber auch durch vielfältige Zusatzmodule prismatische Werkstücke verlässlich spannen. Auf Konsolentischen ist zudem ein vollautomatisches Spannen von Werkstücken möglich, weshalb diese bei der Fertigung von größeren Stückzahlen im Bereich von Möbelbauteilen und Fenstern häufig zum Einsatz kommen. Weiterhin sind Sondertische und T-Nutentische verbreitet, welche beispielsweise zum Spannen spezieller Werkstücke dienen oder sich durch eine hohe Flexibilität in der Aufnahme von Vorrichtungen auszeichnen. Durch elektronische Rüsthilfen wie Laser oder LED werden Maschinenbediener bei der manuellen Ausrichtung von Spannsystemen oder Werkstücken unterstützt, vgl. Abb. 6. Der Trend zur automatisierten Werkstückspannung setzt sich weiterhin fort. Der Marktanteil für Maschinen, die ein manuelles Spannen bedingen, ist erstmals unter 40 % gefallen. Durch automatisch verfahrende Konsolen und Blocksauger können weiter Rüstzeiten reduziert werden. Die zunehmende Funktionalisierung von Bearbeitungszentren führt zudem dazu, dass durch Integration zusätzlicher Aktorik in Spannelementen, z.B. zum vertikalen Verfahren des Werkstücks zum Kantenanleimen, die Flexibilität der Bearbeitung erhöht werden kann. Dem Trend der Digitalisierung folgend werden mittlerweile in der Spanntechnik zunehmend intelligente Komponenten eingesetzt, die Daten generieren um beispielsweise eine Energieüberwachung und vorausschauende Wartung zu ermöglichen.
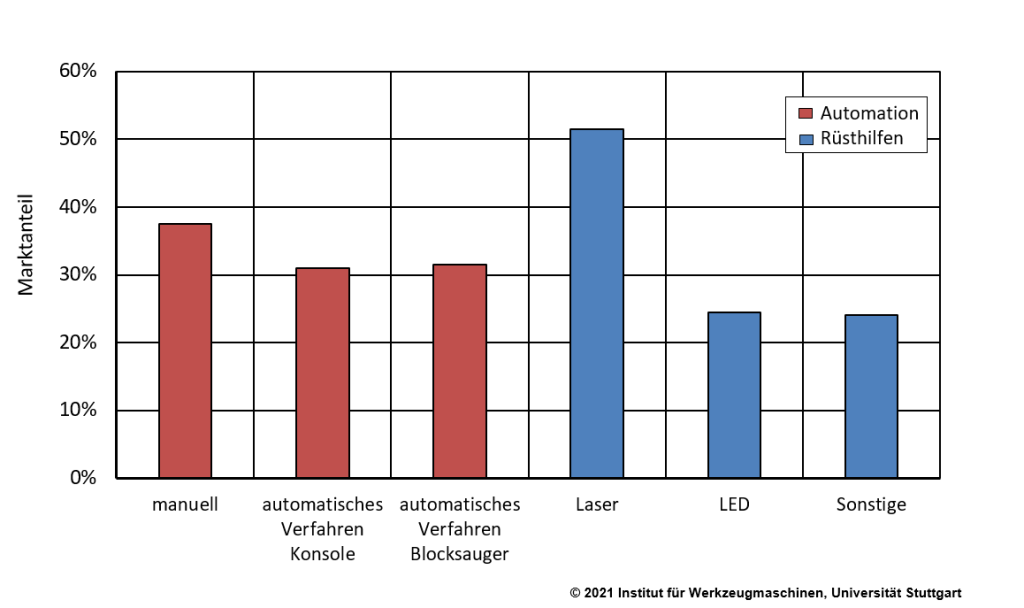
Achsantriebe
In der Verteilung der Achsanstriebssysteme kann für die letzten Jahre keine Veränderung beobachtet werden. Die längste Maschinenachse (X-Achse) wird zu 86,4 % mit Ritzel-Zahnstangen-Antrieben ausgeführt. Der Ritzel-Zahnstangen-Antrieb stellt dabei die kostengünstigste Lösung zum Verfahren auf der X-Achse dar. Zum Antrieb der Z-Achsen werden in knapp 97 % der Fälle Kugelgewindetriebe eingesetzt. Durch große Steigungen im Gewinde kann dabei eine hohe Dynamik der Achsen erreicht werden. Bei den Y-Achsen ist eine etwas ausgeglichene Aufteilung zwischen Kugelgewindetrieb (45,5 %) und Ritzel-Zahnstangen-Antrieb (53 %) zu beobachten. Der Anteil der angebotenen Bearbeitungszentren mit Lineardirektantrieben ist in den letzten Jahren auf einem sehr niedrigen Niveau von ca. 1 % verharrt. Abb. 7 zeigt die Verteilung der Achsantriebssysteme für die drei linearen Maschinenachsen von CNC-Bearbeitungszentren für die Holzbearbeitung.
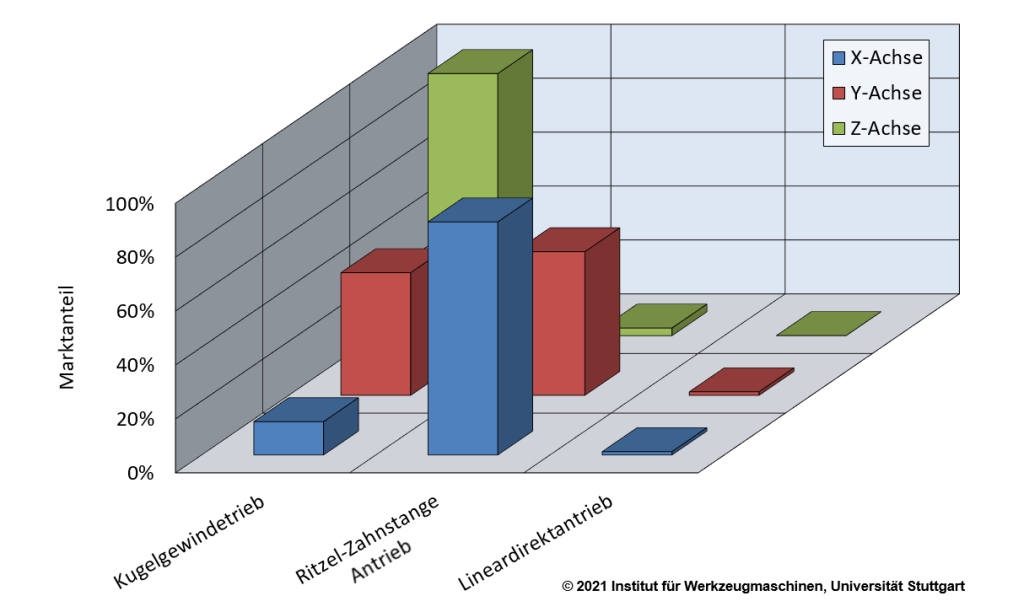
Spindeldrehzahlen und -leistungen
Die Hauptspindel stellt trotz steigender Anzahl an Nebenaggregaten den Kern eines jeden CNC-Bearbeitungszentrums dar. Die Spindeleigenschaften sind dabei, ebenso wie die Achsantriebe, wesentlich für die Produktivität der Fertigung. Die Spindeldrehzahlen und -leistungen beeinflussen dabei zusammen mit der Wahl der Zerspanwerkzeuge maßgeblich die erreichbare Schnittleistung der Bearbeitungsprozesse. Abb. 8 zeigt die Verteilung der Hauptspindeln der ausgewerteten Maschinenbaureihen nach Leistung und Drehzahl.