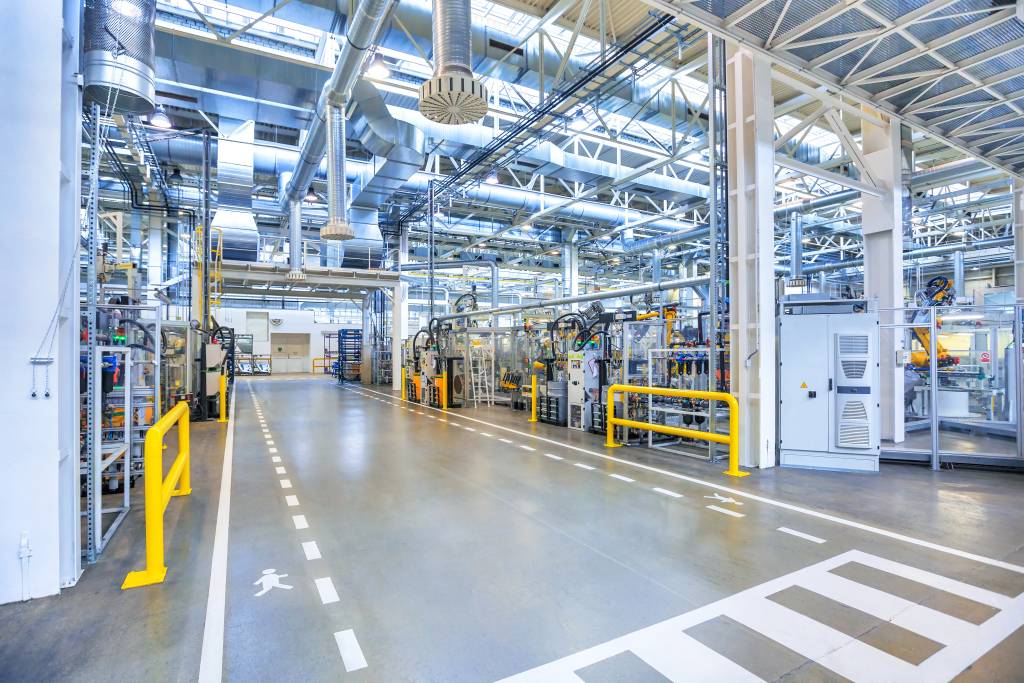
Produzierende Unternehmen liefern immer häufiger maßgeschneiderte Produkte bei sinkenden Losgrößen – und steigendem Aufwand für Umrüstungen. Die regulatorischen Anforderungen steigen und damit der Druck, kosteneffizient und nachhaltig zu produzieren. Weiter haben die Krisen der vergangenen Jahre die Bedeutung verdeutlicht, komplexe und schwankende Produktionsnetzwerke steuern zu können. Manufacturing Execution Systems (MES) dürften in ihren verschiedenen Ausprägungen daher in Zukunft einen unverzichtbaren Bestandteil der vernetzen Produktion darstellen.
Datenflüsse sind entscheidend
In der vernetzten Produktion fallen große Datenmengen an, die es zu erfassen und zum strategischen Vorteil zu nutzen gilt. Dazu gehört es einerseits, die kritischen Daten am Shop Floor an der richtigen Stelle und in der richtigen Form abzugreifen und anschließend so aufzubereiten, dass sie als Entscheidungsgrundlage dienen können. Andererseits müssen der Produktion Daten sowohl bottom-up als auch top-down in der richtigen Qualität und zum richtigen Zeitpunkt zur Verfügung gestellt werden. Das MES ist das zentrale Verbindungselement zwischen den vorgelagerten Systemen des Enterprise Resource Planning (ERP) und des Product Lifecycle Management (PLM) sowie der nachgelagerten werkseitigen Software, die zur Steuerung der Produktion dient. Damit wird das MES zum Kernelement einer effizienten vernetzten Produktion.
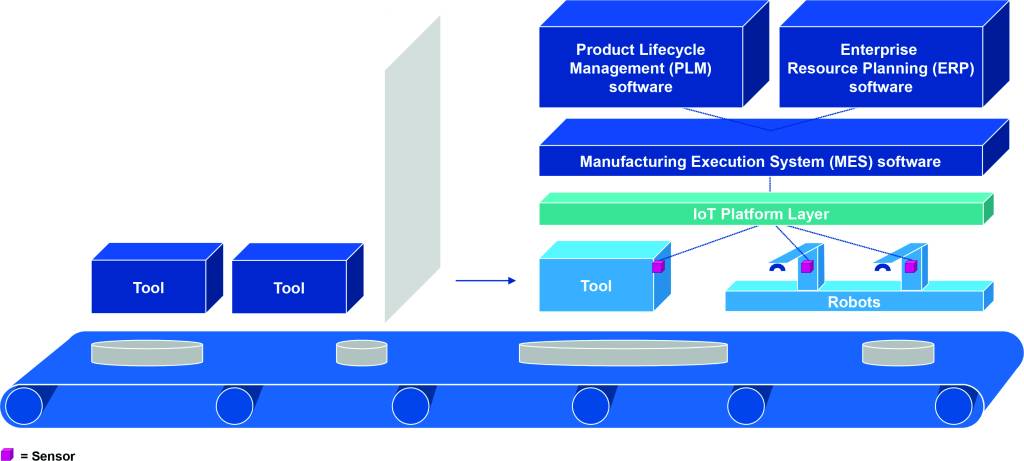
Effekte eines MES
Ein MES liefert Daten meist in Echtzeit und isoliert wichtige Informationen. Dadurch verschaffen diese Systeme den Verantwortliche Transparenz über das Werksgeschehen und ermöglichen ihnen eine Steuerung und Optimierung der Produktion insgesamt sowie von einzelnen Prozessen. Ergänzend können einige MES durch den Einsatz von Machine-Learning-Algorithmen auch Muster erkennen, die auf Maschinenstillstände hinweisen, noch bevor diese tatsächlich eintreten. Dieser Ansatz heißt meistens Predictive Maintenance und wird oft als Impulsgeber für den Weg zur Industrie 4.0 verstanden.
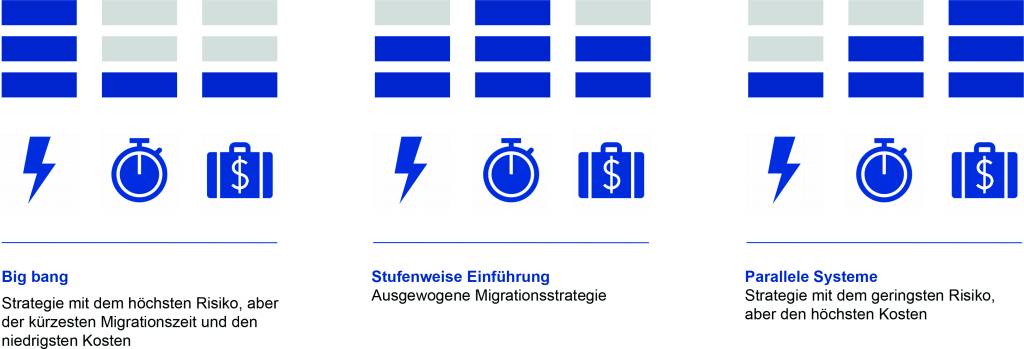
Aufwand und Kosten einer Einführung
Ein MES sollte der Agilität einer modernen Fertigung gewachsen sein und sie nicht etwa durch starre Strukturen ausbremsen. Gerade für mittelständische Unternehmen stehen dafür hardware-agnostische und skalierbare Cloud-Edge-Lösungen bereit, die sich individuell an die Anforderungen anpassen lassen. Viele Systeme unterstützen Anwender auch dabei, verschiedene Werke miteinander zu verbinden. Je nach Komplexität dauert die Einführung eines MES zwischen 12 und 18 Monaten. In der Regel sind die Kosten dabei abhängig vom Umfang der Funktionen, der Anzahl der Benutzerinnen und Benutzer, der Komplexität der Einbindung in die bestehende Systemlandschaft, den individuellen Systemanpassungen und der Anzahl an integrierten Maschinen und Anlagen. Die gewählte MES-Einführungsstrategie kann sich ebenfalls auf die Kosten auswirken. Grundsätzlich gehen die MES-Systemintegratoren in drei verschiedenen Strategien vor: Big Bang, Phased Introduction und Parallel Systems. Die drei Methoden unterscheiden sich hinsichtlich ihres Risikos, Zeitaufwands und der damit verbundenen Kosten.
Kein Projekt ohne Risiko
Da ein flächendeckendes IT-Netzwerk in der Produktion eine der Grundvoraussetzungen für ein MES darstellt, fallen unzureichende Netzwerkinfrastrukturen bei der Systemeinführung schnell auf. Besonders WLAN-Netzwerke sind häufig nicht schnell genug, um den Anforderungen eines MES gerecht zu werden. Weitere Hürden stellen in den Implementierungen regelmäßig die individuellen Schnittstellen dar, die für jedes Modul benötigt werden. Neben den technischen Risiken legen MES-Einführungen immer wieder ein mangelndes Prozessverständnis offen. Abteilungen, Arbeitsabläufe und Softwaremodule greifen heute so ineinander, dass zuständige Projektleiter unbedingt ein weitreichendes Verständnis über den Ablauf der Produktionsprozesse mitbringen sollten. Darüber hinaus stellen fehlende Abstimmungen mit dem Betriebsrat und unrealistische Erwartungshaltungen der verschiedenen Hierarchie-Ebenen einer Firma oft unterschätzte Risiken einer MES-Implementierung dar.