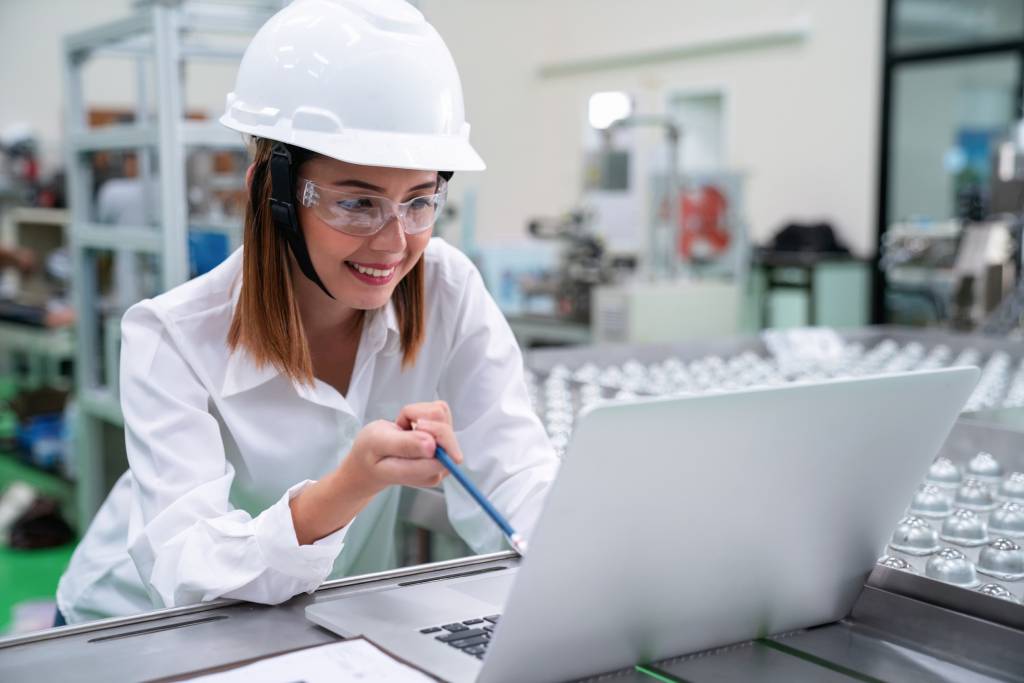
Die exakte Planung von Instandhaltungszyklen für Anlagen, Fahrzeuge, Maschinen und Werkzeuge ist oft ein geschäftskritischer Prozess in Unternehmen – besonders für Fertiger. Dort beeinflussen Faktoren wie Alterung, Verschleiß, Reparatur oder Austausch das Alltagsgeschäft nicht selten erheblich. Die Folgen sind können eine stockende Produktion, zunehmende Energieverbräuche, höhere Produktionskosten oder Qualitätsprobleme sein. Mitunter kann es auch zu einer Verzögerung bei der Warenauslieferung, schlimmstenfalls sogar zum Lieferstopp, kommen.

Vorsicht: Ausfall
Doch Wartungs- und Instandsetzungsarbeiten führen in der Regel zu Ausfallzeiten, wenn sie nicht sorgfältig geplant werden. Um diese Gefahr eindämmen zu können, haben sich in den vergangenen Jahren verschiedene Maintenance-Konzepte etabliert. So existieren heute grundsätzlich vier Wartungsstrategien:
Reactive Maintenance folgt der Regel, eine Reparatur möglichst lange aufzuschieben. Man wird also prinzipiell erst dann aktiv, wenn eine Anlage oder Maschine defekt ist – eine Methode, die sich für geschäftsunkritische Anlagenumgebungen durchgesetzt hat.
Proactive Maintenance stützt sich auf Vorschläge, die von Anlagenherstellern stammen und ihren Kunden als Richtlinien für periodische Wartungen dienen. Ein Beispiel für Proactive Maintenance ist beispielswesie der Ölwechsel eines Fahrzeugs alle 10.000 Kilometer oder sechs Monate. Solche planmäßigen Instandhaltungsroutinen werden mittlerweile oft schon bei der Zulassung von Anlagen und Maschinen definiert.
Predictive Maintenance hat sich im Rahmen der Industrie 4.0 zu einem Trendthema entwickelt. Dieses Instandhaltungskonzept umfasst erstmals auch dynamische Aspekte: Informationen von ähnlichen Anlagentypen und Komponenten werden gesammelt, um sowohl Rückschlüsse auf Ursache als auch bestmögliche Behebungsmaßnahmen zu treffen. Dabei fließen sogar Variablen wie die tatsächliche und spezifische Nutzung durch den Anlagenbetreiber und sogar Faktoren wie das Wetter mit ein.
Die Condition-based Maintenance beschreibt eine zustandsabhängige Instandhaltungspolitik. Sie beinhaltet prognostizierte Handlungsempfehlungen auf Basis einer kontinuierlichen Überwachung von Maschinen. Dazu messen Sensoren den Betriebszustand einer Anlage. Die Daten werden mit festgelegten Randwerten (Indikatoren) verglichen. Bei Überschreiten der zulässigen Betriebsparameter wird festgelegt, ob eine Reparatur, Wartung oder ein Austausch einzelner Maschinenkomponenten erforderlich ist. Insbesondere bei hochwertigen bzw. hochpreisigen Maschinen hat sich dieses Wartungskonzept durchgesetzt.
Mischformen in der Praxis
In der Praxis finden sich häufig Mischformen aus den unterschiedlichen Arten der Instandhaltung. Unternehmen definieren dabei ihre Wartungszyklen so, dass unterschiedliche Instandhaltungsszenarien greifen – abhängig davon, wie wichtig Anlagen und Maschinen für den Geschäftsbetrieb sind. Für gewöhnlich kommt in diesem Zusammenhang ein Zeitplan zum Einsatz, der reaktive und proaktive Wartungseinsätze enthält und zum Teil sogar unvorhergesehene Ereignisse und Korrekturmaßnahmen umfasst. Einen Schritt weiter gedacht liefern prädiktive und zustandsabhängige Methoden das Grundgerüst für eine prospektive Instandhaltungsplanung, bei der der optimale Zeitpunkt in Abstimmung mit der Produktionsplanung vorausschauend ermittelt wird.
Von guten Daten abhängig
Um reibungslose Abläufe in der Herstellung gewährleisten zu können, kommen in der Fertigung in der Regel spezielle Produktionsplaner zum Einsatz. Sie zeichnen für die Verfügbarkeit von Ressourcen und Anlagen verantwortlich. Darüber hinaus obliegt ihnen die Erstellung von Produktionsplänen. Ihr Ziel ist es, einen maximalen Nutzen von Ressourcen zu erreichen, um den größtmöglichen Wert für das Unternehmen in kürzester Zeit zu erzielen. Produktionsplaner sind allerdings davon abhängig, möglichst viele Informationen zu erhalten, um entsprechend effektive Pläne erstellen zu können. Da ihnen doch die Transparenz über einzelne Wartungspläne fehlt, sind sie schlichtweg gar nicht in der Lage, unerwartete Ereignisse wie einen Maschinenausfall, fehlendes Rohmaterial oder einen defekten Motor in ihren Kalkulationen zu berücksichtigen.
Adaptive
Maintenance Scheduling