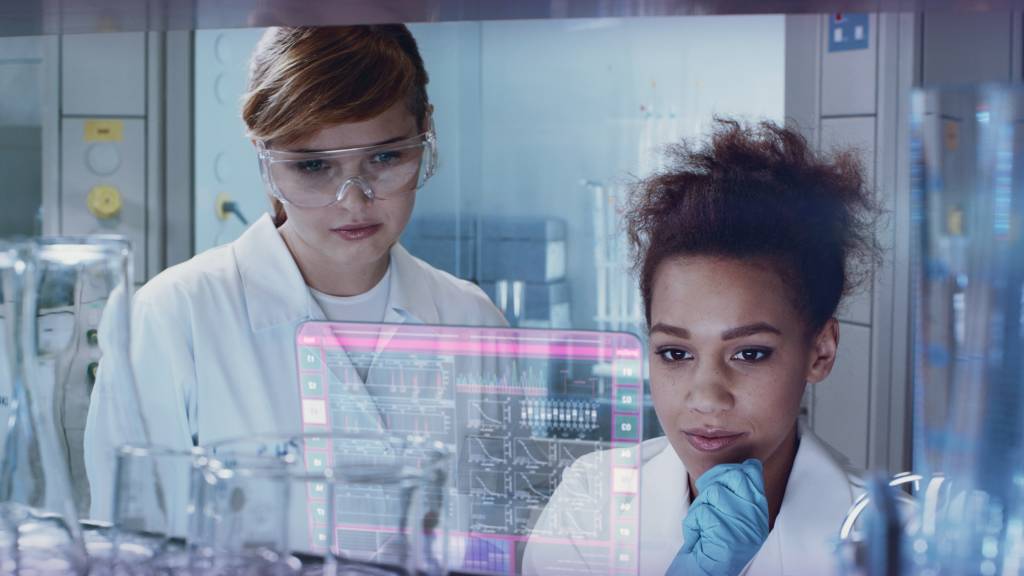
Die im Produktionsprozess erfassten Echtzeitdaten liefern im passenden Kontext und mit der passende Analysemethode – etwa mit Algorithmen des ‚Machine Learnings‘ und weiteren anspruchsvollen Analyseverfahren – detaillierte Erkenntnisse über Prozesse. Die datenbasierte Vorhersage der Qualität, auch bezeichnet als ‚Predictive Quality‘, kann helfen, um Kosten zu senken, die Einführung neuer Produkte zu beschleunigen und zugleich die gesetzlichen Vorschriften zu befolgen. Predictive Quality ist ein vorausschauender und adaptiver Ansatz zur Einbindung der Qualität in die Prozesse. Daten aus dem Fertigungsbereich und der Lieferkette werden dabei zur Beurteilung der Qualität eines Produkts oder zur Ermittlung möglicher Qualitätsprobleme zusammengeführt. Der zugrundeliegende risikobasierte Ansatz macht die Methode zu einem dynamischen Prozess, der stetige Anpassungen erfordert. Analyseverfahren werden zur Bestimmung des Risikogrades und zur Priorisierung der erforderlichen Maßnahmen eingesetzt. Dabei versprechen sich Anwender eine Reihe von Vorteilen aus dem Einsatz des Konzeptes:
- weniger Ausschuss und Nacharbeit,
- gezielte Probeentnahmen und Kontrollen,
- effizientere Fertigung,
- besseres Verständnis der Fertigungs- und Qualitätsprobleme zur Verbesserung der Kennzahl „Time-to-Market“,
- geringeres Risiko, gegen Vorschriften oder Konformitätsregeln zu verstoßen
- höhere Kundenzufriedenheit, durch bessere produkte.
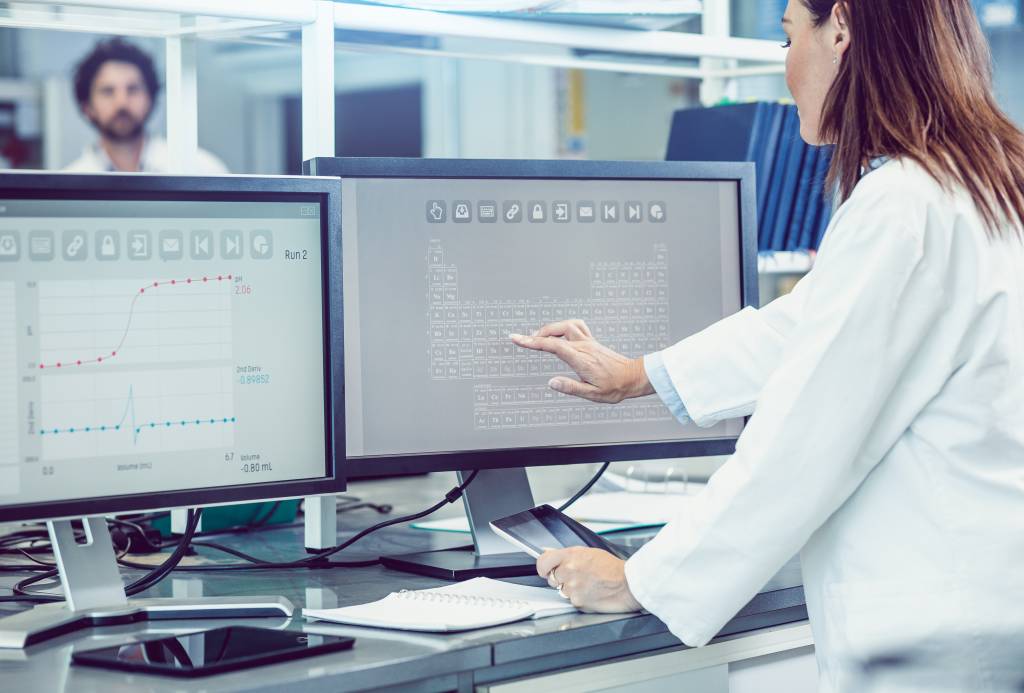
Risikodefinition und -kontrolle
Für eine Vorhersage der Qualität ist eine Definition und Priorisierung von Risiken erforderlich, welche alle Aspekte von Produkten und Prozessen betreffen, nach deren Schweregrad, Zeitrahmen und Art berücksichtigen. Anschließend können Parameter, wie die Häufigkeit von Stichproben oder Inspektionen, bestimmt werden, um so das Risiko hinsichtlich der Produktqualität zu senken. Prädiktive Systeme benötigen genaue, zeitnahe und vollständige Daten zu Prozessbedingungen und -ergebnissen. Diese Daten stammen aus unterschiedlichen Quellen, wie Geräten, Sensoren, Automatisierungssystemen sowie Software, welche Betriebstechnologie (OT) und Informationstechnologie (IT) vereint. Diese Daten müssen zusammengeführt und kontextualisiert werden, um Konsistenz und Qualität der Daten zu erreichen. Eine regelmäßige Rückmeldung aus dem Prozess an die Entwicklung ist erforderlich, um sicherzustellen, dass alles ordnungsgemäß funktioniert.
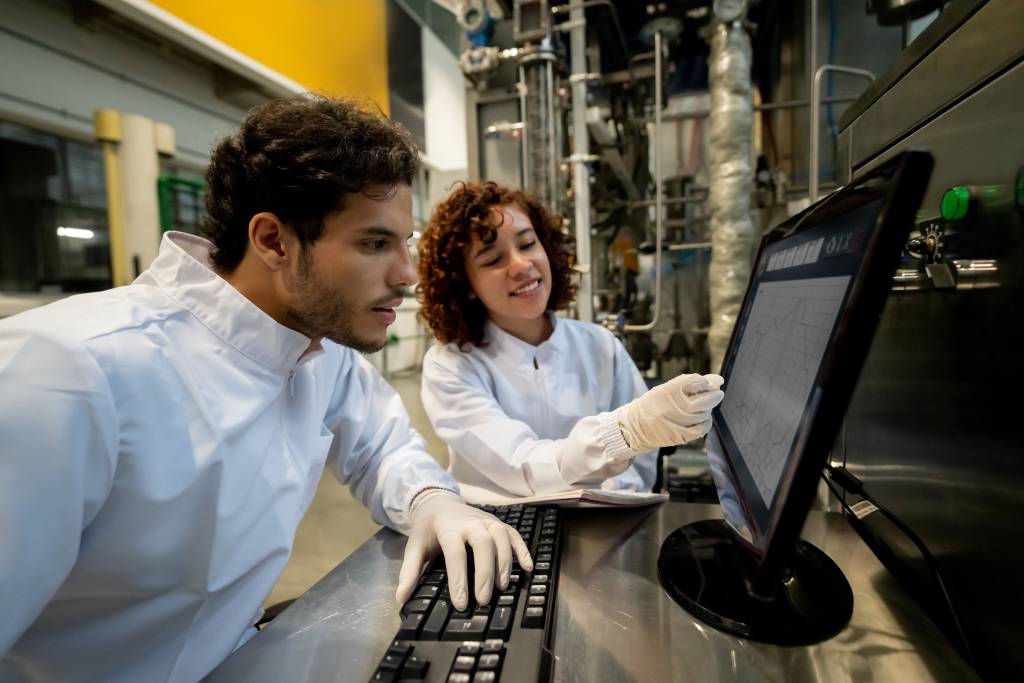
Voraussetzung Integration
Um die erforderlichen vertikalen und horizontalen Informationsflüsse einzurichten, können Fertigungsdatenplattformen helfen. Als Datenquellen für diese Plattformen dienen u.a. Anwendungen wie Manufacturing Execution-Systeme (MES), IIoT-Plattformen (Industrial Internet of Things), Qualitätsmanagementsysteme (QMS) sowie die Analysetools vielfältiger Ausprägungen. Doch keine dieser Lösungen allein genügt, um ein prädiktives Qualitätskonzept zu realisieren. Die oben erwähnte Fertigungsdatenplattform dient nicht nur der Erfassung und Analyse der Qualitätsdaten, sondern zeigt Korrekturmaßnahmen auf und leitet die Mitarbeiter bei ihrer Umsetzung an.

Datendrehscheibe in der Fabrik
Das MES liefert zahlreiche Informationen über Materialien, Spezifikationen, Maschinen, Arbeitsanweisungen, Personal und Daten der statistischen Prozesskontrolle. Viele Systeme können den Produktionszyklus eines Produktes berücksichtigen, um eine Ursachenanalyse (Root Cause Analysis) und die Überprüfung der Wirksamkeit von vorbeugenden Maßnahmen durchzuführen. Abweichungen können im Kontext erfasst werden, und es lassen sich eventuell übergreifende Muster in der Fertigungslandschaft erkennen. Diese Muster können in Predictive-Analytics-Algorithmen zur kontinuierlichen Qualitätsüberwachung und -verbesserung einfließen.