Die Arntz-Optibelt-Gruppe produziert Hochleistungs-Antriebsriemen, die etwa im Maschinenbau, in der Automobilindustrie, der Landtechnik und der Haushaltsgeräteindustrie eingesetzt werden. Das Unternehmen ist in 30 Ländern präsent. Hauptsitz der Gruppe ist Höxter in Nordrhein-Westfalen. Um die Qualität der Produkte und der Fertigungsprozesse zu steigern, nutzt das Unternehmen Daten, die mittels Maschinendaten- bzw. Betriebsdatenerfassung (MDE/BDE) erhoben werden. „Zunächst wollten wir lediglich die Daten unserer Messmaschinen speichern“, sagt Maik Hagemeyer aus der Abteilung Betriebsmittel-Entwicklung. „Uns war aber schnell klar, dass mit einem MES weit mehr möglich ist.“
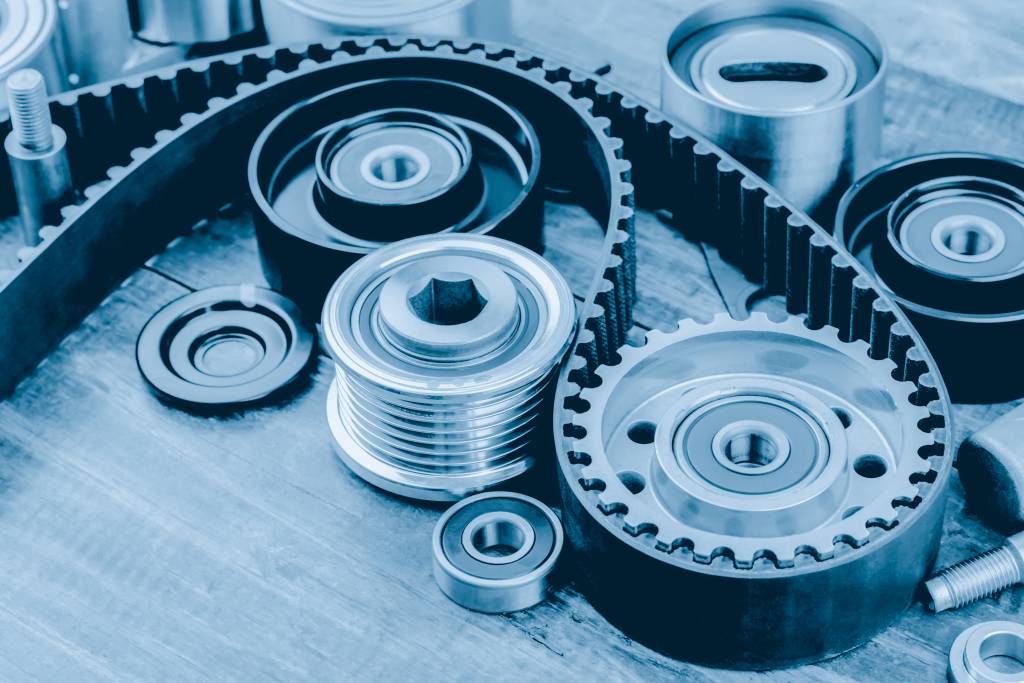
Keine durchgängige Kommunikation
Optibelt nutzte diverse MDE/BDE-Insellösungen, weshalb es keine durchgehende Kommunikation auf dem Shop-floor und zu Systemen darüber gab. Relevante Prozessparameter wie Drücke, Temperaturen usw. konnten nicht in Echtzeit auftragsbezogen mitgeschrieben werden. Des Weiteren war es nicht möglich, die Maschinen automatisch mit den im ERP-System hinterlegten Vorgabewerten zu versorgen. Die Soll-Prozessparameter mussten manuell an den Maschinen eingestellt werden.
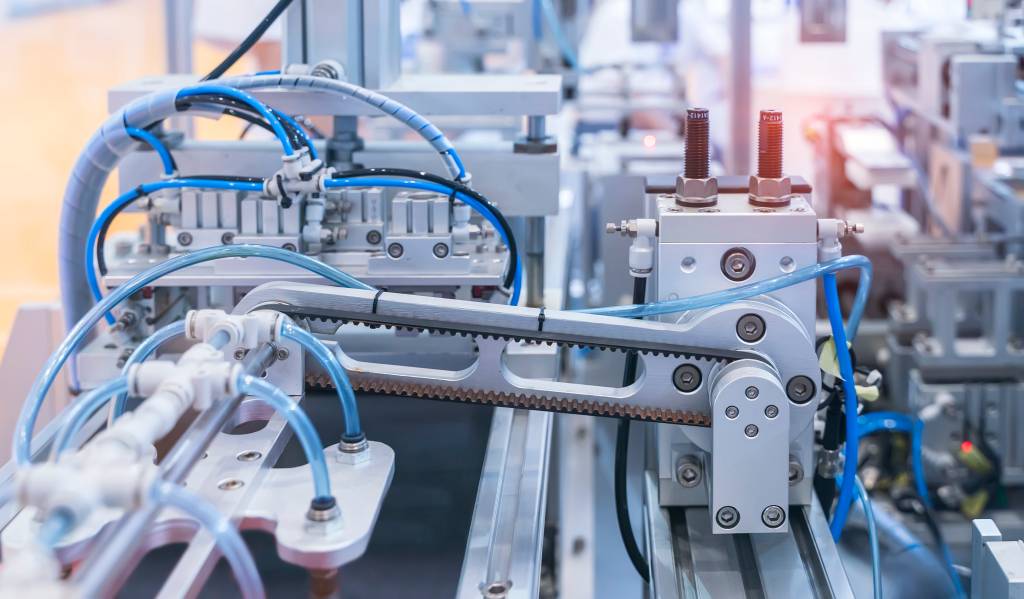
Die Anforderungen
Mithilfe eines Manufacturing Execution Systems wollte Optibelt produktbezogene Prozess- und Qualitätsdaten auswerten und speichern, um daraus anhand von Produktionskennzahlen den Ist-Zustand in der Fertigung als Grundlage für Vergleiche zu ermitteln. Mit diesen Daten sollten sowohl Stillstand- und Ausfallzeiten reduziert, als auch Durchlauf- und Vorgabezeiten sowie der Material- und Produktfluss optimieren werden. „Unser Ziel war, die Produkt- und Prozessqualität insgesamt zu steigern und zu dokumentieren sowie die Transparenz in der Fertigung zu erhöhen“, fasst Hagemeyer zusammen. Gleichzeitig sollten die Dokumentationsanforderungen der Kunden aus der Automobilindustrie erfüllt werden. Am Ende fiel die Wahl auf die Anwendung BisoftMES von GBO Datacomp.
Daten ohne Ende
Zu Beginn wurde ein Pilotbereich definiert, der 16 Vulkanisierkessel, zwei Konfektions- und sechs Messmaschinen umfasste. Auf den Konfektionsmaschinen werden die sogenannten Wickel erzeugt, die dann in den Kesseln vulkanisiert werden. An den Messmaschinen werden die Riemen überprüft. Rund ein Jahr nach dem Strategieworkshop wurde der Pilot in Betrieb genommen. Inzwischen sind mehrere hundert Vulkanisationsanlagen und Bearbeitungsmaschinen an das MES angebunden. Für den Softwarepartner war das Projekt eine Herausforderung. „Es handelte sich um eines der größten Datenvolumina, die wir mit BisoftMES bis dato gemanagt haben“, sagt GBO-Geschäftsführer Michael Möller. Jede Sekunde werden Massen an neuen Daten erzeugt. „Wir haben ein eigenes Protokoll geschrieben, da die Standard-OPC-Protokolle mit diesen Geschwindigkeiten der Datenerfassung teilweise nicht mitkamen“, sagt Möller.