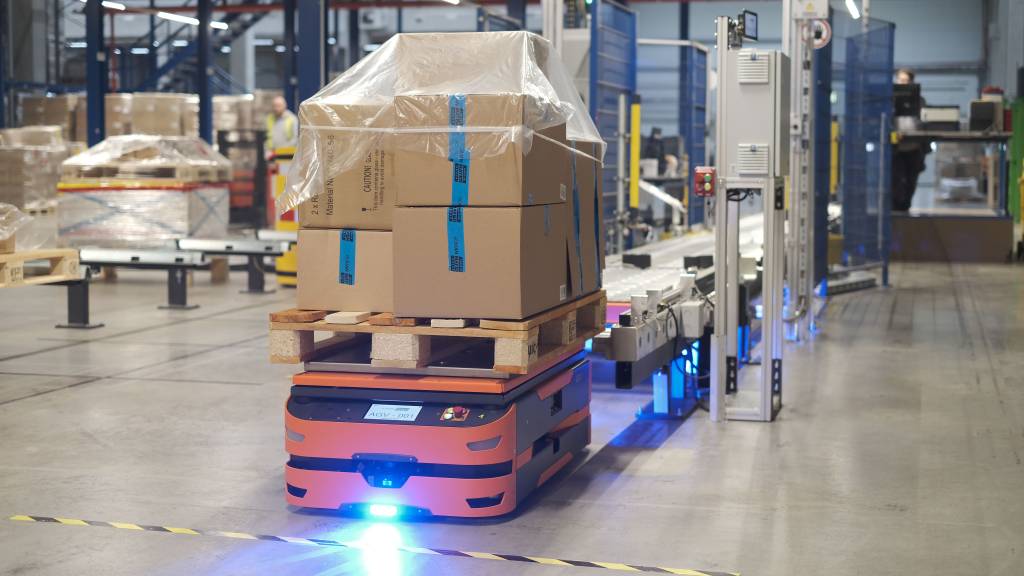
Die Roman Mayer Logistik Group ist als Logistikdienstleister in ganz Europa tätig. Für den 3PL ist eine effiziente Intralogistik entscheidend, um die Kundenerwartungen zu erfüllen. Die Automatisierung spielt hierbei eine zentrale Rolle. Mit der Einführung eines fahrerlosen Transportsystems (FTS) mit mehreren fahrerlosen Transportfahrzeugen (FTF) von Safelog steigerte der Logistikkomplettanbieter die Produktivität an seinem Fulfillment-Standort Nürnberg um 30%.
Ausgeklügelte Fulfillment-Konzepte
Die Roman Mayer Logistik Group ist ein europaweit agierender Komplettanbieter für Kontraktlogistik, Lagerung, Kommissionierung, Prozessoptimierung und Konfektionierung. Der 3PL beschäftigt insgesamt 1.400 Angestellte an 30 Standorten in Europa. Das Portfolio des familiengeführten mittelständischen Unternehmens reicht im Bereich Warehousing von konventionellen bis hin zu hochautomatisierten Logistiklösungen und ausgeklügelten Fulfillment-Konzepten. Am Standort Nürnberg gehören dazu unter anderem das Verholen und Entladen von Seecontainern sowie die Kommissionierung, Verpackung und das Versenden der Waren an Empfänger in Europa und darüber hinaus. Die Lagerfläche im Innen- und Außenbereich umfasst gut 20.000m². Diese Fläche bietet Platz für ca. 40.000 Paletten.
Palettenstau führte zu vermindertem Output
Bereits vor gut zwei Jahren hat Roman Mayer die Intralogistik des Standorts in Nürnberg weitestgehend automatisiert. Ziel war es, den Output zu erhöhen, um besser auf das stark schwankende Saisongeschäft des Großkunden und die damit verbundene Personalknappheit, während der Peak-Zeiten reagieren zu können. „Allerdings erfolgte der Palettentransport zwischen den Sortierplätzen und dem vollautomatischen Wickler weiterhin manuell mit Flurförderzeugen (FFZ) wie Hubwagen und Staplern“, erklärt Niederlassungsleiter Werner Böhm. „Das hat immer wieder zu Problemen geführt.“
Sobald eine Palette mit den Waren bestückt war, wurde diese von einem Werker von den Sortierplätzen zur Pufferfläche verbracht. Von dort aus erfolgte der Transport zur Aufgabestation eines vollautomatischen Wicklers. Da die Sortierung zumeist schneller als der manuelle Abtransport vom Pufferplatz vonstattenging, entstand an der folgenden Station ein Überhang bzw. Stau der fertig kommissionierten Paletten. Im Ergebnis funktionierte das angestrebte FIFO-Prinzip nicht mehr. So wurde Ware, die zuletzt in den Puffer gelangte, anschließend auch als Erstes versandfertig gemacht. Die Paletten erreichten den Versand nicht in der vorgesehenen Reihenfolge und Zeit. Daraus resultierten Verzögerungen bei der Verladung und zu lange Standzeiten der wartenden Lkw. „Außerdem mussten wir für den Palettentransport Mitarbeiter von anderen Stationen einsetzen. Diese konnten in dieser Zeit nicht ihren eigentlichen Aufgaben nachgehen“, sagt Böhm. Die Personalplanung gestaltete sich aus diesem Grund als große Herausforderung.
Um den Transport zwischen den Stationen zu automatisieren und damit die Effizienz des Bereichs zu erhöhen, beauftragte Roman Mayer Safelog, einen der führenden FTS-Produzenten in Europa. Der Prozess sollte in diesem Bereich dabei so ausgelegt sein, dass der 3PL im Durchschnitt mit aktuell 480 Paletten pro Tag auch zukünftig eine steigende Nachfrage bewältigen kann.
Effizienter Palettentransport durch AGV
Um den Rotationswickler optimal mit Paletten zu versorgen, erarbeitete Safelog einen Workflow mit zwei FTF vom Typ AGV L1 mit Palettenauflage. „Bei Roman Mayer kommen unsere größeren mobilen Transportroboter zum Einsatz. Dank der omnidirektionalen Fahrweise brauchen die AGV weniger Platz zum Manövrieren und können Paletten mit bis zu 1.500kg transportieren“, erläutert Michael Treml, Niederlassungsleiter bei Safelog.