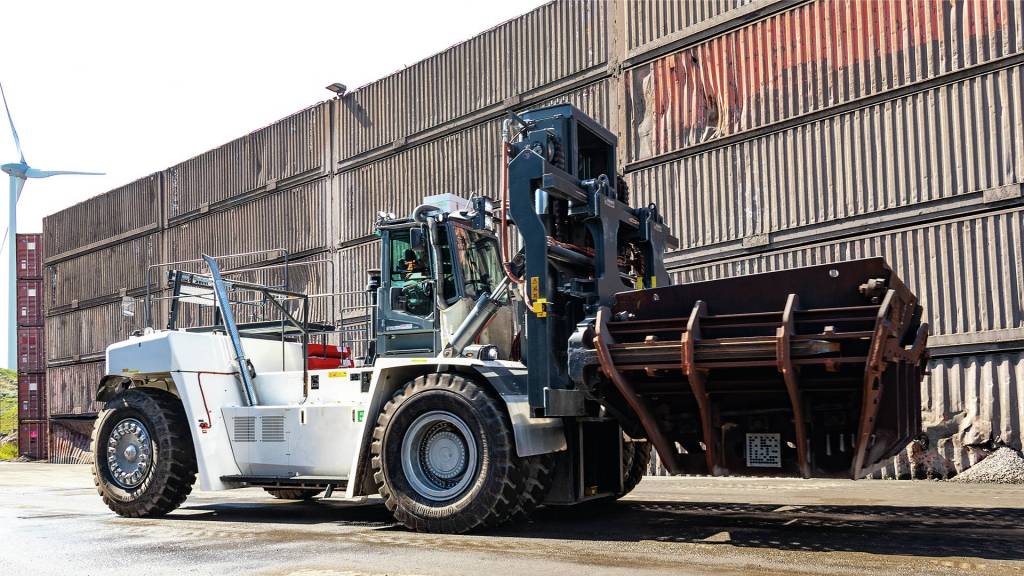
Es liegt Salzgeschmack in der Luft. Man kann das Meer erahnen. Ein Windrad dreht sich auf dem Deich. Direkt an der Nordsee, nordwestlich von Amsterdam. Doch hier gibt es nicht nur Touristenidylle, sondern auch das einzige Stahlwerk der Niederlande befindet sich hier. Genauer gesagt in IJmuiden, in der Provinz Noord-Holland. Über 8.000 Menschen arbeiten diesseits des Deichs auf der Fläche einer mittelgroßen Kleinstadt. Und zahlreiche Industriedienstleister sind auf dem Areal tätig und kümmern sich beispielsweise um die Entsorgung und Weiterverarbeitung der bei der Stahlproduktion entstehenden Schlacke. Sie ist ein Nebenprodukt der Stahlherstellung und wird beispielsweise als Untergrund im Straßenbau eingesetzt.
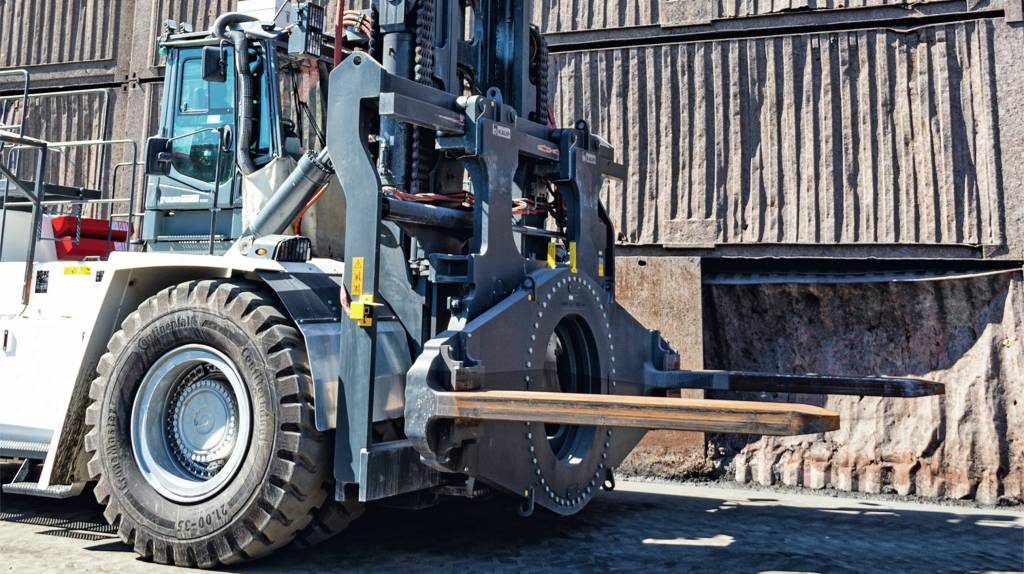
Grafitstaub in der Luft
In der Vergangenheit wurde die Schlacke in großen Gießtiegeln gesammelt und an den Rand des Werksgeländes gefahren. Dort entleerten massive Brückenkräne die Behälter unter freiem Himmel, damit die Schlacke sich vor der Weiterverarbeitung abkühlen konnte. Nachteil dieser Methode: massive Graphitstaubentwicklung, unter der vor allem die Bewohner der Nachbargemeinde Wijk aan Zee zu leiden hatten.
Und der anfallende feine Grafitstaub ist nicht nur schmutzig. Er enthält auch zahlreiche Schadstoffe wie Mangan, Blei und Vanadium. Anhaltende Bürgerbeschwerden führten deshalb dazu, dass die bisherige Methode von der Regionalregierung im Frühjahr 2019 verboten wurde.
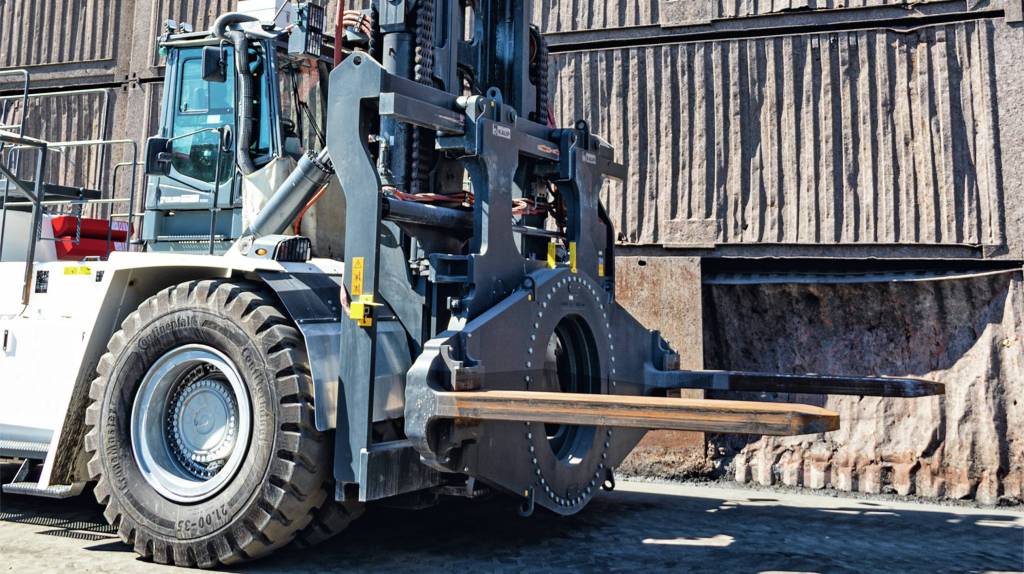
Prozesse komplett umgestellt
„Wir waren also gezwungen, zeitnah etwas zu tun“; erklärt ein Projektbeteiligter, „und beschlossen, den bisherigen Prozess komplett umzustellen.“ Die Lösung? Der Bau einer neuen Halle, um so die Staubbelastung mit komplexen Filteranlagen auf null zu reduzieren.
Gleichzeitig wollte der Kunde von Kaup die Schlackenentsorgung nicht nur sauberer, sondern auch moderner und zukunftssicher gestalten. Individuelle Transportbehälter, sogenannte Skips, sollten die althergebrachten Gießtiegel ersetzen. „Daraus entstand aber für uns ein neues Handlingsproblem“, berichten weitere Projektbeteiligte. „Schließlich können die Skips bis zu 23t Schlacke aufnehmen und sollten nicht von einem stationären Gerät, sondern einem Gabelstapler entleert werden.“ Zudem böte ein Gabelstapler noch weitere Anwendungsmöglichkeiten. „Doch bisher gab es kein so großes Anbaugerät für Gabelstapler, das unseren Anforderungen entsprach“, erläutert der Entsorgungsprofi weiter, „und so kam Kaup ins Spiel.“
Anspruchsvolle Konstruktion und Produktion
Der Industriedienstleister kontaktierte Kaup zum ersten Mal im Frühjahr 2019. Von da an ging es ganz schnell. Intensiver Austausch zwischen einem kleinen Konstruktionsteam von Kaup und den anderen Projektbeteiligten folgte. „Und dabei wurden wir mit ein paar interessanten Herausforderungen konfrontiert“, berichtet Kaup-Konstrukteur Bernd Ackermann. „Die Größe des Geräts und der enge Zeitrahmen waren zwei Aspekte“, so Ackermann weiter. „Die angepasste Flanschanbindung und der komplett neue Schweißanschluss zwei weitere ausschlaggebende Faktoren“, erklärt der erfahrene Konstrukteur weiter. „Denn so etwas hatten auch wir in der Form noch nie konstruiert.“ Doch nach etwa zehn Wochen – im Oktober 2019 – konnte mit der anspruchsvollen Produktion begonnen werden. So mussten beispielsweise die Gabeln langwierig von Hand an die riesige Grundplatte geschweißt werden. Dies sogar zwei Mal – denn schließlich orderte der Kunde zwei 60T391.