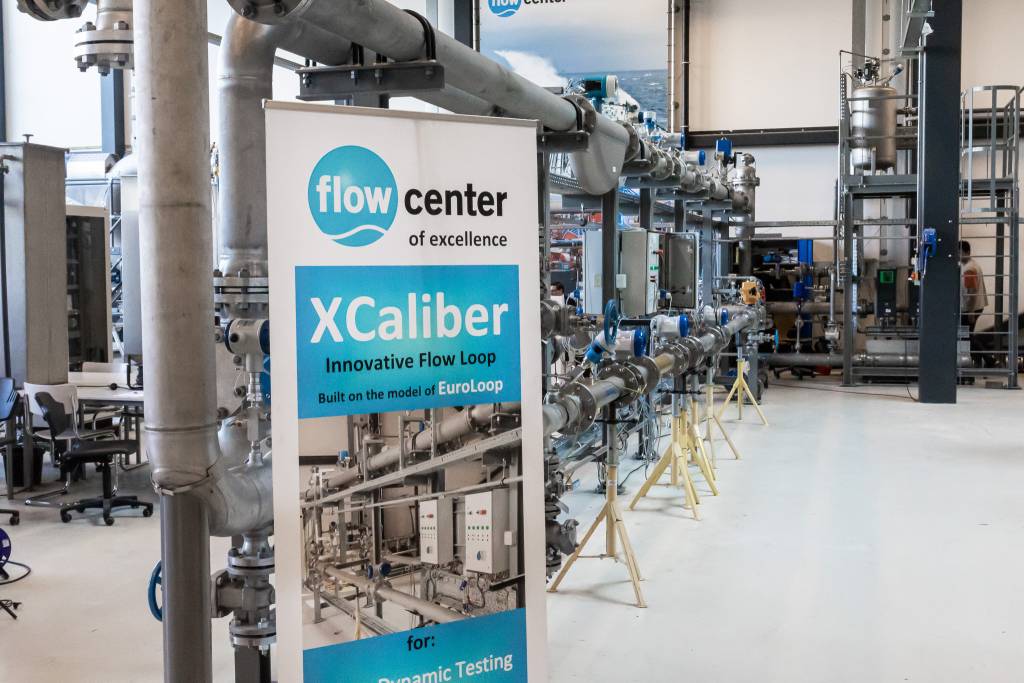
Der Impuls zum Implementationsprojekt kam von Jules Oudmans, einem Allianz-Mitglied und Director bei UReason: „Ich kenne Daan Wortel von der Duurzaamheidsfabriek schon lange. Das Flow Centre of Excellence innerhalb der Nachhaltigkeitsfabrik bietet eine ausgezeichnete, industrieorientierte Testeinrichtung, die in Bezug auf die Hardware, Kommunikationsprotokolle und verwendeten Steuersysteme der realen Praxis sehr nahekommt.“ „Das Flow Center of Excellence ist eine Musterfabrik für die Prozessindustrie, in der wir ausbilden,“ sagt Daan Wortel, Geschäftsführer der Duurzaamheidsfabriek. „Software wie jene von UReason, aber auch vielfältige Hardware von den Stiftungsmitgliedern ist dort bereits installiert. Ich fand die Idee toll, den nächsten Schritt in der Digitalisierung der Prozessindustrie zu gehen, und konnte für das Projekt die Unterstützung des SMITZH, der Smart Industry Fördereinrichtung für die Metropolregion Rotterdam gewinnen.“

Startschuss gefallen
Von der ersten Hardware-Installation im November 2021 bis zu den Tests der Feld-zu-Edge-zu-Cloud-Kommunikation der Anlagendiagnose und -prognose Ende Januar 2022 dauerte es knapp drei Monate, auch daher hat das Demonstrationsprojekt im Flow Center of Excellence den OI4 Implementation Award 2021 erhalten. Das Integrationsprojekt setzt in der Edge an, also bei dem mit Wasser betriebenen Flow Loop, der nach dem Muster des für Öl- und Gasanlagen relevanten EuroLoop-Kalibrierungscenters aufgebaut ist. Die Verkabelung und Umsetzung der Signale von Sensoren und Aktoren geschieht wie branchenüblich in Rangierschränken. Typische Prozessanlagen in Fabriken verfügen teils über mehr als 25.000 Sensoren und Aktoren. Üblicherweise werden 32 Endgeräte mit einer Klemmkarte verbunden. 64-polige Stammkabel führen in den zentralen Schaltraum und dort in System-, Interface- und Rangierschränke. 60 Schaltschränke können ohne Weiteres in einer realen Prozessfabrik erreicht werden. Hier im Projekt wurden drei Schaltschränke neu hinzugefügt. Nach den Schaltschränken geschieht der Sprung in die Ethernet-Verkabelung. Die verwendeten IIoT-Server nutzen den auf TCP/IP laufenden MQTT-Broker zur Abfrage der Endgeräte.

Parameter festschreiben
Im Fall der Installation am Flow Loop wurden in zwei Segmenten alternative Wege der Konnektivität erprobt. Das Projekt hat auch den Zweck, den Mitgliedern der Open Industry 4.0 Alliance die Möglichkeit zu eröffnen, ihre Software und Hardware mittels der verschiedenen Kommunikationsprotokolle einzurichten. Dabei ist trotz der Beachtung von Standards auch manches Verfahren, etwa die Auswahl bestimmter Parameter, erst festzuschreiben. Insgesamt elf Mitglieder der Allianz sind am ‚OI4 Demonstrator for Process Industry‘ unmittelbar oder mittelbar beteiligt. Die vorhandene Installation ist ein Mix aus Komponenten von Mitgliedern und Nicht-Mitgliedern – wie es auch sonst in der Realität üblich ist. Die Soft- und Hardware von Balluff (Nicht-Mitglied) oder Endress+Hauser (Mitglied) war bereits im Flow Loop verbaut. Nun kommen Komponenten von Pepperl+Fuchs, Wago, CodeWrights (Nicht-Mitglied) und UReason (Mitglied) neu hinzu. Mit Pepperl+Fuchs und Wago übernehmen ebenfalls zwei Mitglieder die Organisation in verschiedenen Rangierschränken und den Zugriff auf die physikalischen Endgeräte, wie elektromagnetische Durchflussmesser, Antriebe mit variabler Drehzahl, Zentrifugalpumpen und Sensoren zur Zustandsüberwachung. Eine gewisse Ausnahme stellt auf der physikalischen Ebene das smarte Ventil Focus-1 dar, das mit einem Computer sowie jeweils zwei Druck- und Temperatursensoren ausgestattet ist. Das Produkt des Joint Ventures Focus-On von Samson und Krohne kann sich direkt ins Netz verbinden.

Protokolle im Parallelbetrieb
Von der physikalischen Ebene der Geräte stellen die Projektbeteiligten die Verbindung nach oben dar, also in Richtung northbound. Sie beginnen mit dem bewährten Hart-Protokoll über verschiedene Gateways, alternativ per Hart IP oder OPC UA. Dabei nutzt Pepperl+Fuchs zwei Rangierschränke (MUT A und B) mit Anbindung der physikalischen Endgeräte in Section A und B, während Wago über einen weiteren Rangierschrank der Section 2 die Endgeräte anbindet, die in der gleichnamigen Sektion organisiert sind. Bereits in der Werkshalle gilt es, die analogen Signale ins Digitale zu übertragen. Hier wird heute noch in den meisten Anlagen das Hart-Protokoll genutzt, das analoge Signale in 0 und 1 auf zwei Frequenzebenen digitalisiert. Gleichzeitig werden Ethernet-Kabel gelegt, um auch das TCP/IP-basierte MQTT-Protokoll zu nutzen. So gelingt schon vor Ort – physikalisch betrachtet nach den Rangierschränken – die Umsetzung in Hart IP oder OPC UA. Damit erfolgt dann der Transport der Daten an verschiedene Server, die diese analysieren und konsolidieren können.