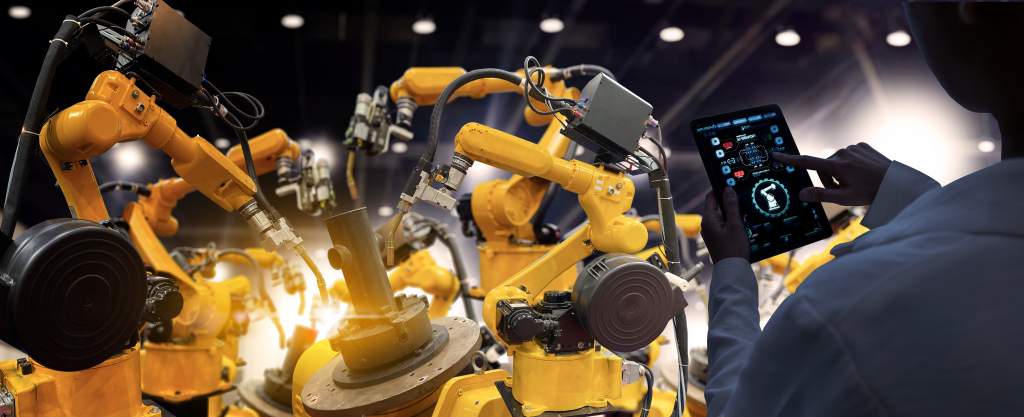
Derzeit dominieren Schlagwörter wie Künstliche Intelligenz (KI), Internet of Things (IoT) und Big Data die Diskussion um die Zukunft der Produktion. Diese Technologien bilden die Basis für Trends wie Industrie 4.0, Smart Production und die Smart Factory, bei denen es im Kern um die intelligente und ganzheitliche Vernetzung der gesamten Produktionskette geht. Laut einer Studie von Microsoft führen 88 Prozent der Befragten bereits eigene IoT-Projekte durch, 92 Prozent davon sind überzeugt, dass IoT entscheidend für den Geschäftserfolg ist. IoT lebt wie alle Digitalisierungsprojekte von Daten, die, eingehend ausgewertet und analysiert, die Basis für Entscheidungen über die Art und Weise des weiteren Ablaufs der Produktion liefern. Dazu greifen Sensoren umfassende Daten zum Zustand der Maschinen und zum Ablauf der Produktionsprozesse ab, d.h. liefern ein Bild davon, was sich in der Anlage abspielt. Meist handelt es sich dabei um real existierende Sensoren, die, an den neuralgischen Punkten der Anlagen und Maschinen angebracht, Daten zu den verschiedensten Aspekten liefern. Das können Parameter wie Temperatur, Druck, (Fließ-)Geschwindigkeit, Beschleunigung sowie Werte zu Drehzahl, Schaltzustand, Position oder auch Schall sein.
Software-Sensoren
Der Einsatz physischer Sensoren kann aber durchaus fehleranfällig, oder aufgrund baulicher Gegebenheiten schlicht nicht möglich oder kostspielig sein. Zudem können viele Werte auch nur im Labor ermittelt werden. Beispiele dafür sind etwa Aspekte der Materialeigenschaften und damit der Qualität des Endproduktes. Solche Angaben liegen daher erst mit einer erheblichen Zeitverzögerung vor und können so nur begrenzt zur Steuerung der aktuellen Produktion beitragen. Die Lösung hierfür sind Software-Sensoren, oft auch als virtuelle Sensoren bezeichnet. Diese können auf Basis der von physischen Sensoren generierten Daten wie etwa Temperatur, Druck, oder Flüsse, sowie anderweitig verfügbarer, den Prozess beeinflussenden Parameter abhängige Größen vorhersagen, d.h. reale Sensorwerte, Labormesswerte oder nicht direkt messbare Größen wie Qualität, Lebensdauer oder anderes. Hierzu nutzen Software-Sensoren so genannte Vorhersagemodelle. Damit quantifizieren sie die Auswirkungen der Messgrößenauf die Zielgröße. Sie können außerdem durch einen erneuten Lernprozess der Modelle leicht an Veränderungen in der Systemumgebung angepasst werden.
Bislang daten-, zeit- und kostenaufwändig
Warum aber setzen sich Software-Sensoren trotz dieser Vorteile nur schleppend durch und warum schrecken viele Unternehmen vor deren Einsatz noch zurück? Der Grund: Der Aufbau der zugrundeliegenden Vorhersagemodelle erfordert in der Regel sehr große Datenmengen und nimmt viel Zeit in Anspruch. Darüber hinaus erfordert er manuelle Eingriffe und eine intensive Beteiligung von Data Scientists mit Fachkenntnissen. So müssen beispielsweise Daten synchronisiert und bereinigt werden, sowie Beziehungen zwischen Daten extrahiert, Ursachen von Vorkommnissen analysiert und auf Basis von Zeitreihen ein Vorhersagemodell erstellt werden. Verwendet man etwa neuronale Netze als Grundlage, muss zunächst das richtige Design gefunden und anschließend aufwändig trainiert werden. All dies machte die Erstellung von SoftwareSensoren zeit- und kostenaufwändig. Zudem können konventionelle datenwissenschaftliche Methoden in vielen Fällen industrielle Anforderungen nur unzureichend erfüllen, etwa, wenn es um komplexe Sensorik-Umgebungen mit mehreren 1.000 Signalen geht und schnelle Ergebnisse gefordert sind.
Eigenständige Analysen und
Vorhersagemodelle