
Züger Frischkäse hat das Wissen über die sorgfältige Käseherstellung in der Familie weitergetragen. Vater Edwin Züger wollte die noch wenig bekannten Frischkäseprodukte herstellen. 1984 war der erste Züger-Mozzarella marktreif. Bis heute liegen Frischkäseprodukte im Trend. Neben Mozzarella entstehen unter anderem Butter, Frischkäse, Mascarpone, Ricotta und Quark, Hirtenkäse, Hütten- oder auch Grill- und Bratkäse.
Christof und Markus Züger haben neue Spezialitäten und verschiedene Convenience-Produkte auf den Markt gebracht, wie den veganen „Züger MozzaVella“. Das Unternehmen setzt modernste Technologie wie einen Koagulator und umfassende Automation ein. 50 Prozent der Produkte werden exportiert, Hauptabnehmer ist Deutschland. Der Betrieb verarbeitet täglich zwischen 400 und 450t Milch, davon etwa 20 Prozent Bio-Milch. Nachdem sich die Menge innerhalb von zehn Jahren verdoppelt hat, ist in den nächsten Jahren erneut eine Kapazitätserweiterung geplant. „Mit neuesten Technologien möchten wir unser Unternehmen stetig weiterentwickeln und so den sich immer schneller ändernden Kundenbedürfnissen begegnen“, sagt Christof Züger.
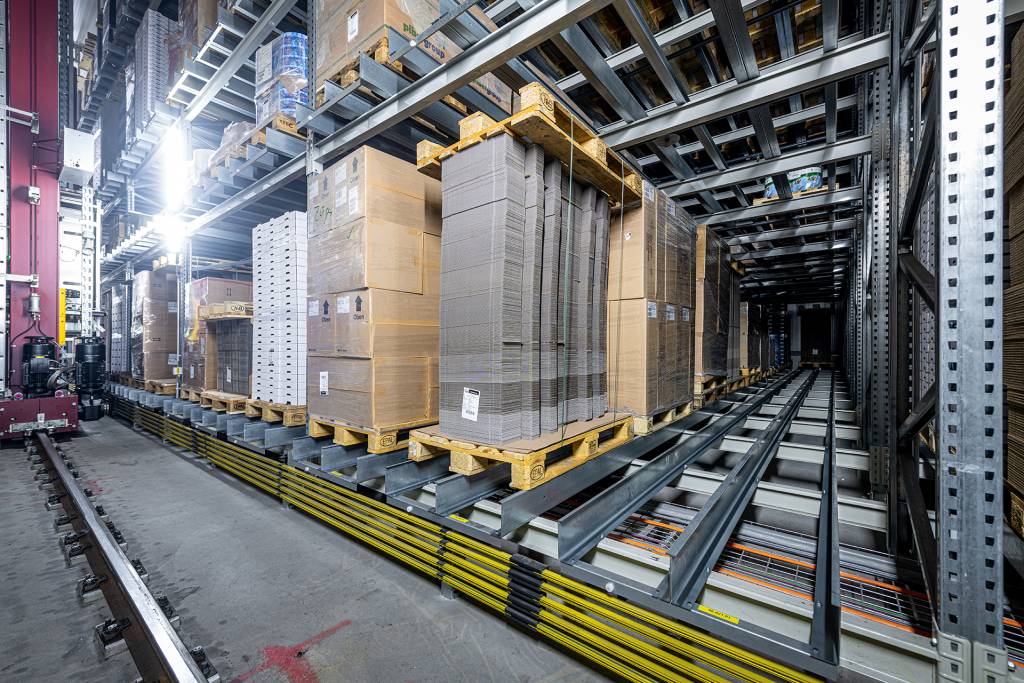
Logistisch für hohe Produktionsmenge aufgestockt
René Giger vom Westfalia-Vertrieb Schweiz hat seit 2006 die Intralogistik-Automatisierung des Betriebs begleitet. 2010 realisierte Westfalia als ersten Auftrag das kompakte automatische Frischelager mit 2.500 Palettenstellplätzen. Das hat der Intralogistikspezialist beim inzwischen 4. umfangreicheren Auftrag nun nach Westen erweitert. „Die Durchsatzleistung mussten wir erhöhen, um die wachsende Anzahl an Produkten durch den Betrieb zu führen“, beschreibt René Giger die Herausforderung. „Außerdem musste mehr Verpackungsmaterial eingelagert werden, um steigende Preise, Rohstoffverknappung, Verfügbarkeiten und längere Lieferfristen abzufedern. Die 700 zusätzlichen Frischelager-Stellplätze hatten sich durch das kompakte Layout angeboten.“ Die selbsttragende Silobauweise spart dabei Kosten für den Hallenbau.
Für den täglichen Durchsatz von ca. 2000 Paletten gab es bislang sechs Senkrechtförderer (SKF). René Giger: „Wir haben zwei weitere einsäulige SKF installiert und auf fünf Ebenen mit Fördertechnik angebunden. Die Lifte sind mit Rollenförderern auf Drehtischen ausgerüstet. Ladeeinheiten lassen sich damit stirnseitig und seitlich aufnehmen und übergeben.“ Die SKF befördern mit bis zu 90m/min über eine Hubhöhe von 24,5m zusätzlich ca. 150 Paletten pro Stunde, erhöhen auch die Einlagerleistung aus Produktion und Verpackungsaufgabe.
Aus Platzgründen aufs Dach gesetzt
Die hohe Zahl der Senkrechtförderer ist eine Besonderheit des Lagersystems: „Wegen der beengten Platzverhältnisse war unsere Lagertechnologie mit Satellit von Beginn an ein Muss für die Logistiklösung – alle drei Lager haben wir aufs ehemalige Dach gebaut“, so Giger. Denn die besonders kompakten mehrfachtiefen Lager mit bis zu fünf Ebenen lassen sich auf knapp bemessene Flächen zuschneiden.
„Nach dem Frischelager von 4°C mit 115x15x11m haben wir 2012 das Tiefkühllager von -18°C mit 30x24x11m und 1.400 Stellplätzen installiert. 2014 folge das Verpackungslager mit 40x34x11m und ca. 3.000 Regalstellplätzen für Paletten. Wir haben so die firmeninternen Intralogistik-Abläufe automatisiert.“
Ausgelegt ist das System für Europaletten aus Holz und Kunststoff, für Paloxen aus Kunststoff und für bis zu 1,3m breite, 0,9m tiefe und 1,8m hohe Ladeeinheiten. Im Kühl- und Tiefkühllager sind sie bis zu einer Tonne schwer, die Verpackungsmaterial-Einheiten bringen es auf jeweils bis zu 250kg. Alle Komponenten seiner Lagersysteme inklusive eigener Speicherprogrammierbarer Steuerung (SPS) und seiner Schlüsseltechnologie Satellit hat Westfalia bei Züger verbaut, darunter zwei Querverschiebewagen für die Pickzone.
Die vier Regalbediengeräte transportieren ca. je 60 Paletten pro Stunde im Doppelspiel und sind mit dem Lastaufnahmemittel Ketten-Satellit ausgestattet. Um im Frischelager die Zugriffsfrequenz zu verdoppeln, fahren zwei RBG auf einer Schiene. Jedes Lager kommt mit einer Gasse aus, das senkt Energieverbrauch und Wartungsaufwand.
Westfalias Warehouse Execution System Savanna.NET generiert bei Züger täglich bis zu 8.000 Fahraufträge. Es bündelt Warehouse Management und Warehouse Controlling – „mit allen projektspezifischen Besonderheiten wie zwei RBGs auf einer Schiene oder einem Senkrechtförderern mit zwei Lastaufnahmemitteln übereinander“, erklärt Christian Goltermann, Vertriebsleiter Software & IT bei Westfalia. „Es tauscht Daten mit dem Host-System CSB aus, befüllt und leert automatisch eine Schnellkühlzone, versorgt eine Pickzone und die drei unterschiedlichen Produkt- und Temperaturzonen Frische, Tiefkühl und Normaltemperatur für Verpackung.“
Neben der Software implementierte Westfalia zusätzliche Savanna-Workstations der Marke Terra als Client des CSB-Hostsystems. 20 Terra-Workstations sind über das gesamte Werk verteilt. Nachgerüstet wurde das System mit sechs Kontrollscannern, um einen Datenversatz zwischen Lagerverwaltung und Materialflussrechner auszuschließen.
Nachhaltige Lagerautomatisierung für höhere Produktivität
Die schrittweise Erweiterung des automatischen Lagersystems auf engstem Raum kommt der Unternehmensentwicklung entgegen, erklärt Silvan Egger, zuständiger Projektleiter bei Züger Frischkäse. „Obwohl wir das erste Lager bereits in 2010 realisiert haben, konnten wir dieses aufrüsten, umrüsten und auf den neuesten Stand bringen. Diese Erweiterbarkeit hat für das Unternehmen und dessen Entwicklung große Vorteile. Durch die aktuelle Erweiterung können wir die Produktivität massiv erhöhen. Lkw müssen nicht mehr auf Ihre Paletten warten.“