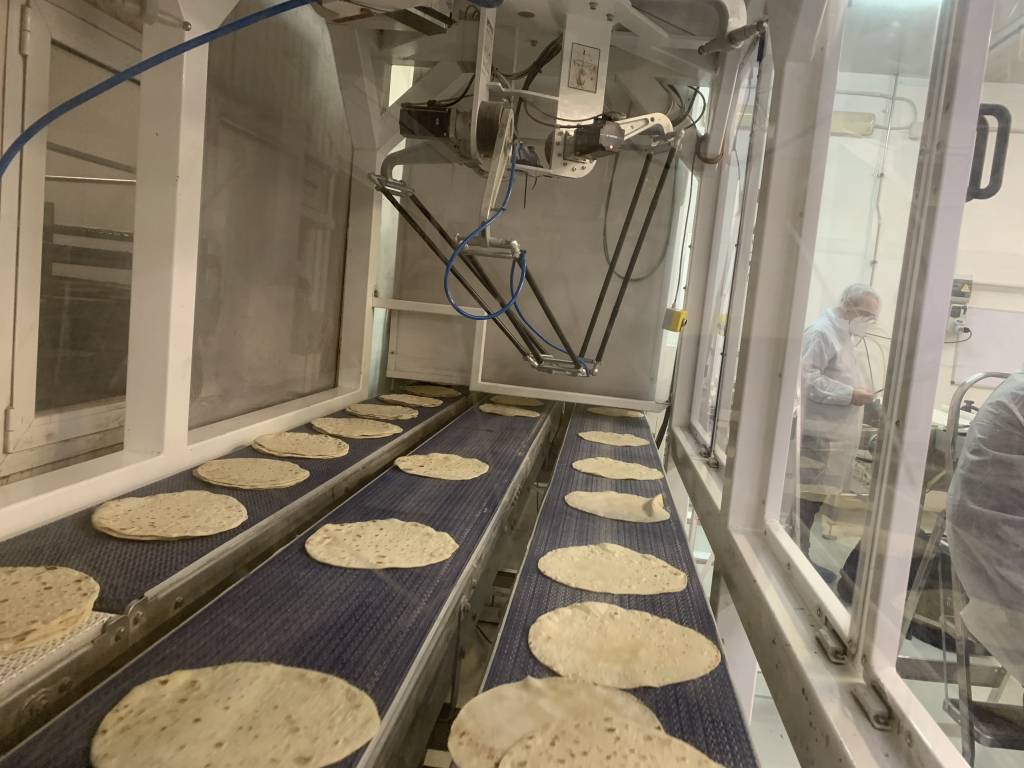
Der Ursprung der Piadina geht auf die Zeiten der alten Römer zurück und noch heute ist das Fladenbrot unter Erwachsenen und Kindern sehr beliebt. Im Laufe der Jahre hat es die Grenzen Italiens überschritten und im Ausland viel Verbreitung gefunden. Nach den Daten des Konsortiums zur Förderung und zum Schutz der Piadina Romagnola ist die Produktion im Jahr 2020 rapide angestiegen und hat 22.030 Tonnen erreicht. Das entspricht einer Steigerung von mehr als 23 Prozent gegenüber dem Vorjahr. Um die wachsende Nachfrage des Marktes bedienen zu können, sind gut funktionierende Produktionslinien unerlässlich.
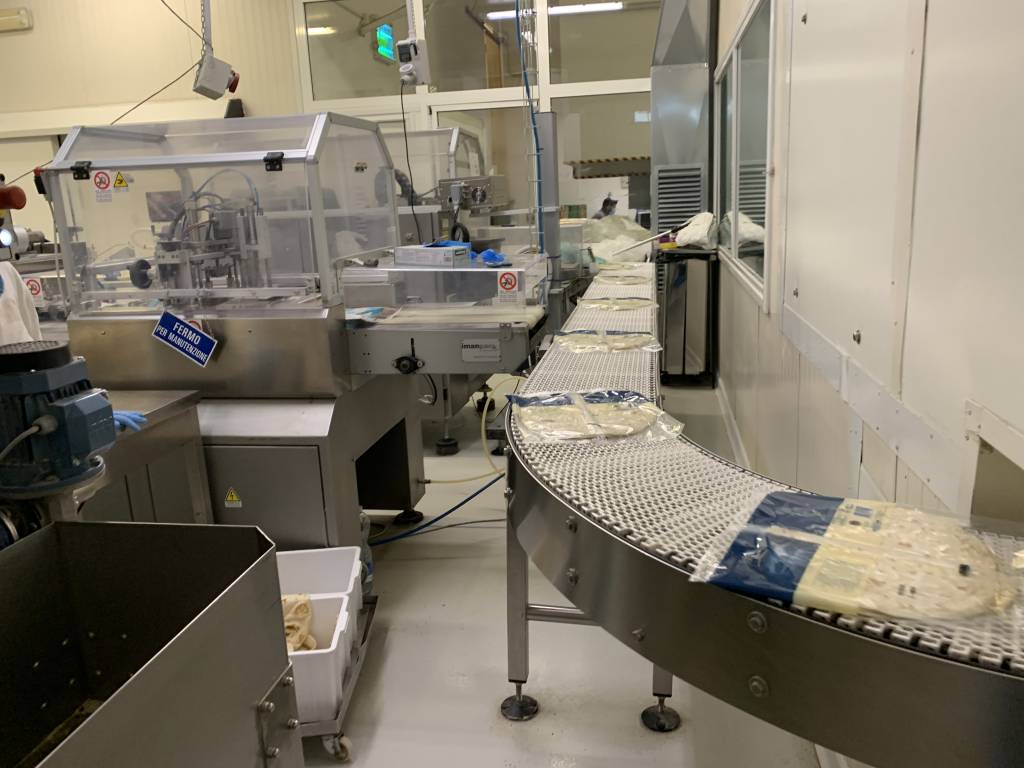
Hohe Ansprüche an Pick&Place
Aus diesem Grund wandte sich ein Piadina-Produktionswerk in der Provinz Rimini an den Systemintegrator Bosso Automazioni. Auf Basis einer Zusammenarbeit mit Yaskawa wurde das Pick&Place-System der Anlage überarbeitet, das zum Stapeln der Piadine für die Verpackung verwendet wird. Das frühere System war stark veraltet und umfasste Komponenten, die nicht dem Industriestandard entsprechen. Mit zwei Delta-Robotern, die jeweils von einer separaten Steuerung mit MechatrolinkII-Schnittstelle und Sigma7-Servomotoren geführt wurden, hatte die Produktionslinie nie die gewünschten Ergebnisse erzielt. Selbst mit dem Einsatz eines zusätzlichen Roboters waren die Probleme geblieben: geringer Wirkungsgrad, mangelhafte Produktaufnahme, häufige Komponentenausfälle, Überlastung der Verstärker. Mit den höheren Produktionsraten, die zur Deckung der Spitzennachfrage erforderlich sind, hätten sie sich vermutlich noch verschlimmert.
Die Anforderungen des Endkunden waren deshalb klar: Beseitigung der Zuverlässigkeits- und Zyklusprobleme, Erhöhung der Produktivität auf 85 Piadine pro Minute und Reduzierung des Ausschusses auf unter 3 Prozent. Gleichzeitig sollte auch eine Verbesserung der Lebensdauer der verwendeten Geräte, der Motorabstimmung und der Qualität der Bewegungsabläufe erreicht werden, um Ausfälle der Servomotoren zu vermeiden bzw. zu verringern. Zusätzlich zu all diesen Anforderungen sollte versucht werden, den Umfang der Änderungen am bestehenden System so gering wie möglich zu halten.
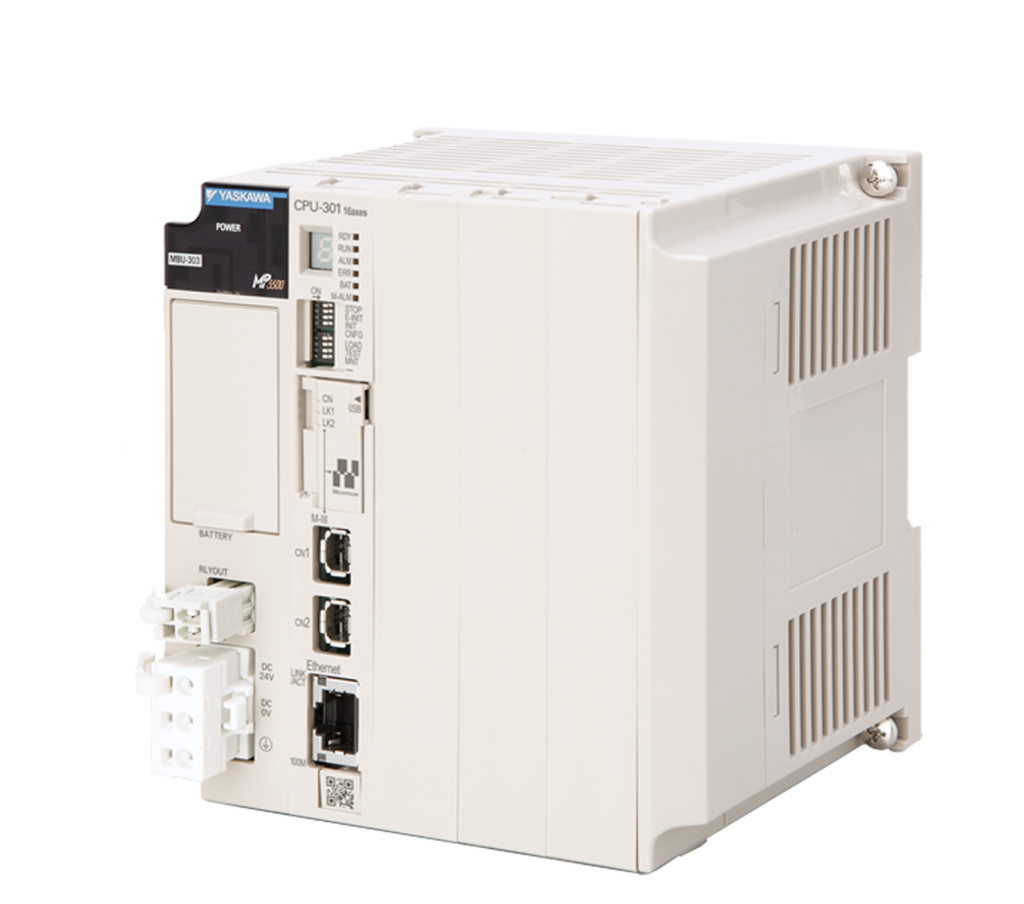
Komplexe Modernisierung
Die Komplexität der Anwendung war beträchtlich: Das Aufnehmen und Ablegen der Piadine sollte zwischen gegenläufigen Förderbändern stattfinden. Der Vorgang erfordert eine hohe Variabilität, sowohl in Bezug auf die Form als auch auf die Positionierung. Für das Aufnehmen und das Ablegen ist daher der Einsatz von Conveyor-Tracking-Funktionen an den laufenden Bändern erforderlich. Die Piadine werden in unregelmäßigen Abständen aus einer langen Backlinie mit anschließender Abkühlung herausgefahren. Um die Anwendung zu steuern, wurde eine Lösung benötigt, die mit einer Vielzahl von Komponenten zusammenwirken kann. Die Maschinensteuerung MP3300iec RBT von Yaskawa wurde auf Firmware-Ebene in die Steuerung integriert. Man entschied sich für die Verwendung nur einer Steuerung für die gesamte Anlage. Dadurch wurde das Konzept der singulären Steuerung konkretisiert und die in Wechselwirkung stehenden Funktionen der Komponenten selbst konnten besser gesteuert werden konnten.
Doch damit nicht genug: Ein weiterer Faktor verkomplizierte die ohnehin schon schwierige Situation. Da es sich bei dem Endanwender um einen Supermarktlieferanten handelt, der im Dreischichtbetrieb arbeitet, konnte die Produktionslinie während der Migration auf die Yaskawa-Lösung nicht unterbrochen werden. Die zu berechnende Dynamik war komplex, sowohl wegen der hohen Variabilität als auch wegen der Verwendung einer Kamera (anstelle eines echten Vision-Systems). Sie war außerhalb des Roboter-Arbeitsbereichs positioniert, was die Kalibrierung zusätzlich erschwerte.
Da im Vorfeld keine Praxistests möglich waren und die Produktion nicht gestoppt werden durfte, entschied sich das Yaskawa-Team dazu, die Effizienz der Sortieralgorithmen in einer Simulation über das HMI der Zelle zu testen. Die Idee war, die Anwendung auf dem Simulator zu entwickeln und zu testen und dann von der Simulation auf die reale Maschine zu wechseln. Die Ergebnisse waren überzeugend: Die maßgeschneiderte Simulation erlaubte es, das Lastmanagement zu verbessern und die Geschwindigkeit der Roboter schnell anzupassen. Als die reale Zelle in Betrieb war, erlaubte der Simulator die Visualisierung des Prozesses in Echtzeit. Aufgrund der Flexibilität der für die Anwendung entwickelten Algorithmen konnte auch die charakteristische Unregelmäßigkeit der ankommenden Produkte sehr gut gemanagt werden. Das Ziel, etwa 6.000 Piadine pro Stunde zu stapeln, wurde erreicht, und der Prozentsatz der Ausschussware wurde auf null reduziert.
Erfolgsfaktoren und Ergebnisse
Das Knowhow von Yaskawa in den Bereichen Datenerfassung, Risikoanalyse und Projektmanagement bildeten die Basis für den Erfolg dieser Anwendung. Von großer Bedeutung war auch das Ergebnis in Bezug auf die Energieeffizienz: Während ursprünglich jeder Deltaroboter über eine eigene Steuerung geführt wurde, gibt es nun für die gesamte Lösung eine singuläre Steuerung. Die kumulative Last wurde von auf 55 Prozent des ursprünglichen Werts reduziert und die Leistung der Servomotoren wurden von 1kW auf 750W verkleinert.