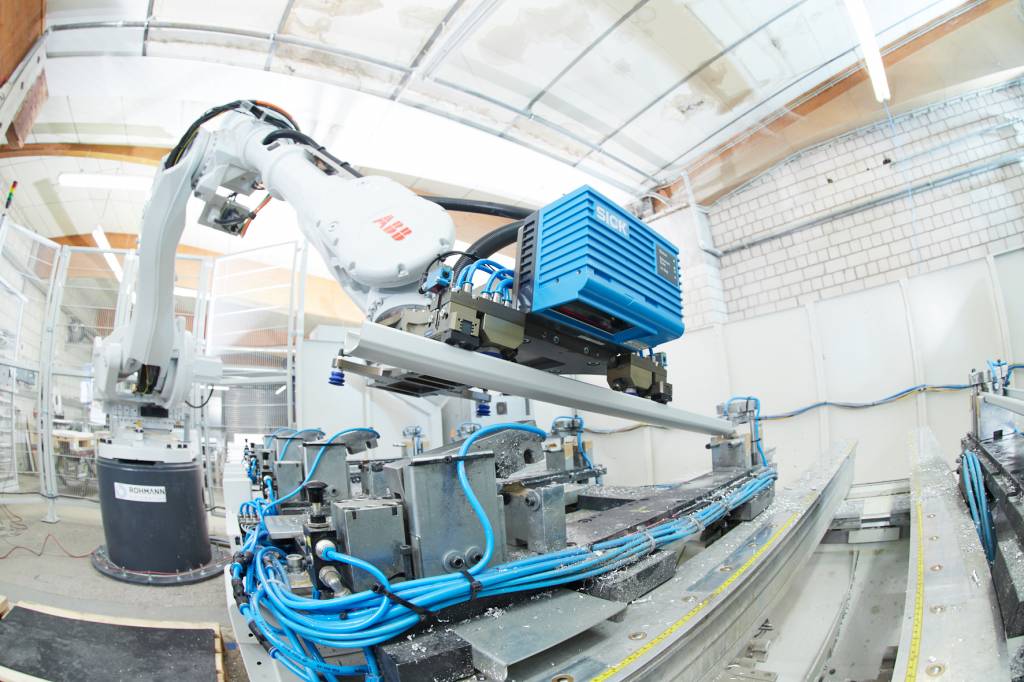
In der Palettieranwendung bei MS-Schuon, die die Firma Rohmann-Automation mithilfe von Sick-Sensoren umgesetzt hat, bestücken zwei Industrieroboter eine automatische Bohr- und Fräsmaschine mit Aluminiumprofilen verschiedener Länge. Während bei vergleichbaren Applikationen bisher meist aufwendige Bereitstellungsmagazine mit definierten Entnahmepositionen eingesetzt werden, ist der hier beschriebene Weg deutlich flexibler und kostengünstiger. So werden die Rohprofile auf Standard-Europaletten in bis zu 25 Lagen mit bis zu 38 Teilen pro Lage angedient, lediglich eine Separierung der einzelnen Lagen mittels dünner Zwischenlagen sorgt für etwas Ordnung. Eine exakte Positionierung oder Ausrichtung der Profile ist nicht erforderlich. Nicht nur die Lagetoleranzen der einzelnen Profile auf den Paletten, sondern auch die Lage und Drehung der gesamten Palette wird aufgrund der 3D-Auswertung beim Greifen berücksichtigt. So stellt die Verschiebung der Paletten um mehrere Zentimeter und Verdrehungen um mehrere Grad kein Problem dar, selbst geneigte Paletten und unebener Industrie-boden behindern den ABB-Roboter in keiner Weise. Liegt eine Palette oder ein Profil außerhalb eines einstellbaren Toleranzfensters, so generiert die Applikation eine Störungsmeldung an den Roboter und verhindert so zuverlässig eine Kollision.
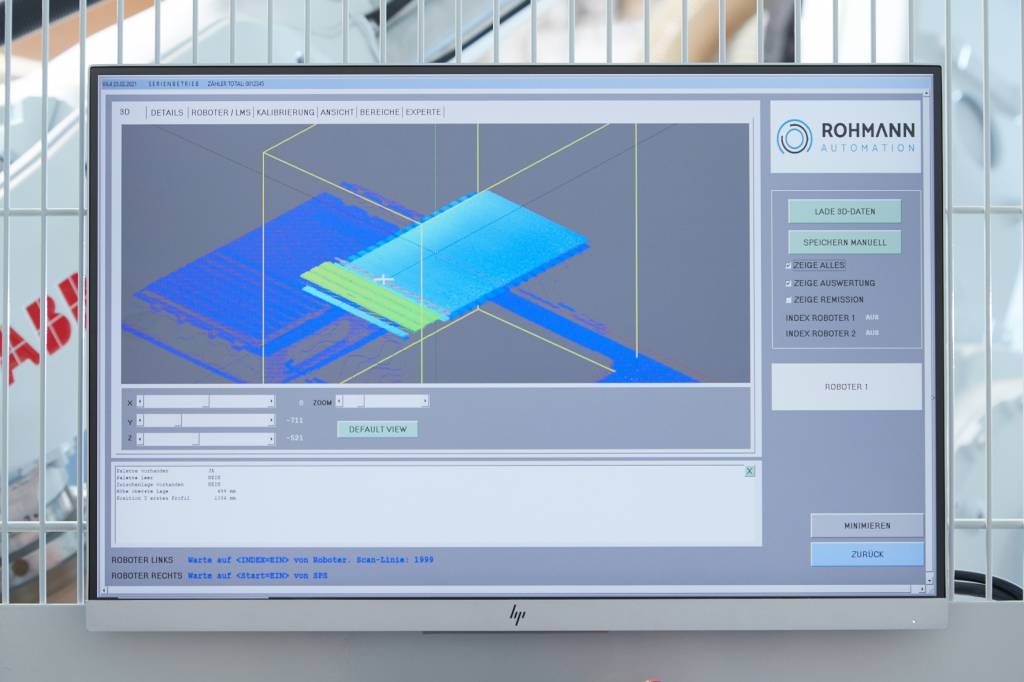
Roboter mit Überblick
Um bei Zufuhr einer neuen Palette oder nach manuellem Eingriff Prozesssicherheit zu gewährleisten, verschafft sich der Roboter einen Überblick über die neue Situation. Mittels Scene-Scan überblickt er die gesamte Palette. Hier werden die Höhe der obersten Lage, die ungefähre Position des ersten zu entnehmenden Profils sowie weitere Plausibilitäten ermittelt. Bedienfehler bei der Herstellung einer Ausgangssituation sind somit ausgeschlossen. Nun folgen die Scannung und das Greifen der einzelnen Profile sowie das Ablegen in die CNC-Maschine des Herstellers SCM.
Präzise Bauteilentnahme
Nun folgen die Scannung und das Greifen der einzelnen Profile. Für hohe Messgenauigkeit und schlanke Taktzeiten erfolgt ein präziser Einzel-Scan des zu entnehmenden Profils nur in dem Bereich, in dem das Bauteil zuvor grob lokalisiert wurde. Für eine platzsparende Zuführung der Bauteile, werden die Aluprofile ineinander versschachtelt pro Lage angeliefert. Jedes zweite Profil ist hierzu auf dem Kopf gedreht. Zur Entnahme sind hierzu unterschiedliche Greifwerkzeuge notwendig. Der Roboter erhält deshalb vom 3D-Vision System zusätzlich die Information, wie herum das zu entnehmende Profil liegt.
Geordnetes Ladebild
Doch wohin mit den fertig gefrästen Profilen? Während die Entnahme und Ablage auf Fertigteilpaletten bisher von Hand erfolgte, wird hier die gleiche Technik wie oben beschrieben genutzt. Der Roboter scannt die Fertigteilpalette und bestimmt die ideale Absetzposition für das nächste Profil. Angebrochene Lagen, Palettenwechsel und Lagetoleranzen der Paletten werden automatisch berücksichtigt. Ergebnis ist ein stets geordnetes Ladebild, ganz ohne manuellen Eingriff.
Positionsbestimmung
Da auch die nur ca. 1 bis 2mm dicken Zwischenlagen automatisch umgesetzt werden ist deren Bestimmung der 3D-Lage erforderlich. Hier werden bei der Positionsberechnung nicht nur die 3D-Daten des 2D-Lidar-Sensors LMS4000 von Sick, sondern auch dessen Remissionsinformationen genutzt. Die 3D-Informationen liefern die Höhendaten, während die Remissionsdaten für eine präzise Kantenbestimmung der Zwischenlagen verwendet werden. So können auch Objekte wie Folien und Bleche vermessen werden, deren Dicke weit unterhalb der spezifizierten Messgenauigkeit des Sensors liegen. Aufgrund seiner Messeigenschaften erkennt der Sensor die Bauteile selbst dann, wenn sie kreuz und quer oder umgedreht auf der Palette liegen. Und auch die Position der Palette wird sicher erkannt. Ebenso wenig bedarf es einer genauen Positionierung der in die Zelle eingebrachten Paletten. Der Werker kann die Palette nach Augenmaß absetzen, den Rest steuert dann der Lidar-Sensor.