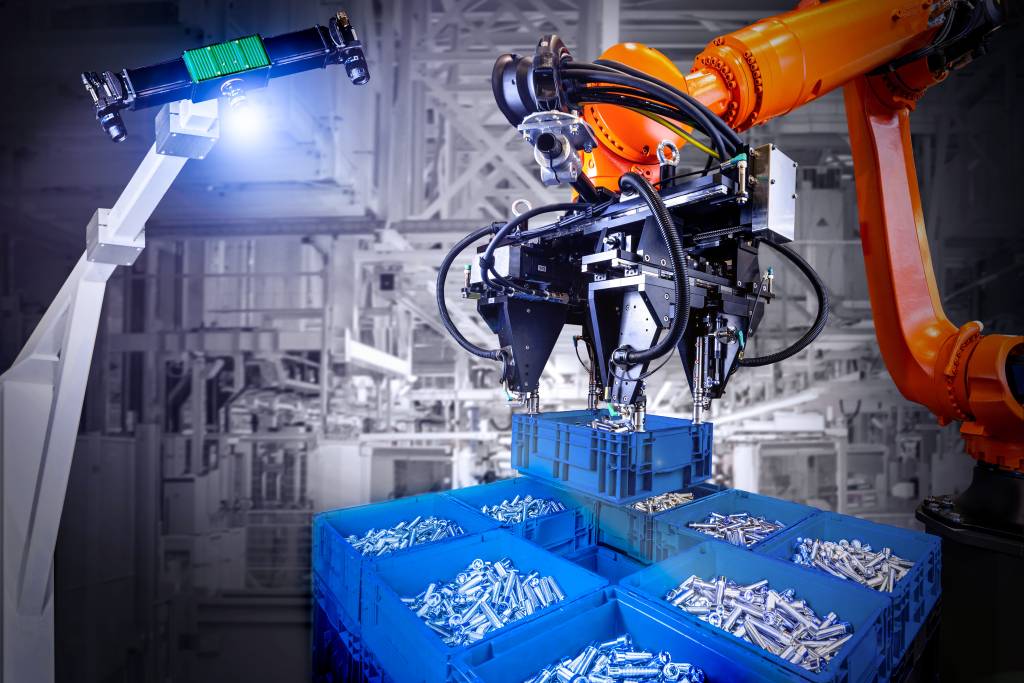
Kleinladungsträger (KLT) unterschiedlichster Größe und Farbe sind in zahlreichen Industriebereichen gang und gäbe. Für ein sicheres und wirtschaftliches Depalettieren solcher Palettenstapel sind flexible Automatisierungssysteme erforderlich, die in der Vergangenheit meist nicht allen Anforderungen der Anwender entsprachen. Die automatisierte Entnahme von KLTs von Paletten mit bekanntem Stapelschema ist heute kein echtes Problem mehr – jedoch bei unbekannten, ständig wechselnden Schemata mit KLT verschiedener Größe, Farbe, Orientierung und Greifposition stoßen herkömmliche Depalettiersysteme schnell an ihre Grenzen. Das 3D-Visionsystem OSC 6D (Object Shape Capture) von VMT Bildverarbeitungssysteme als Basis für Roboter-gestützte Komplettsysteme dient auch zur KLT-Depalettierung. Eine Besonderheit der Lösung besteht darin, dass sie selbst dann mit sehr kurzen Taktzeiten zuverlässig arbeitet, wenn die Stapelschemata unbekannt sind und ständig wechseln.
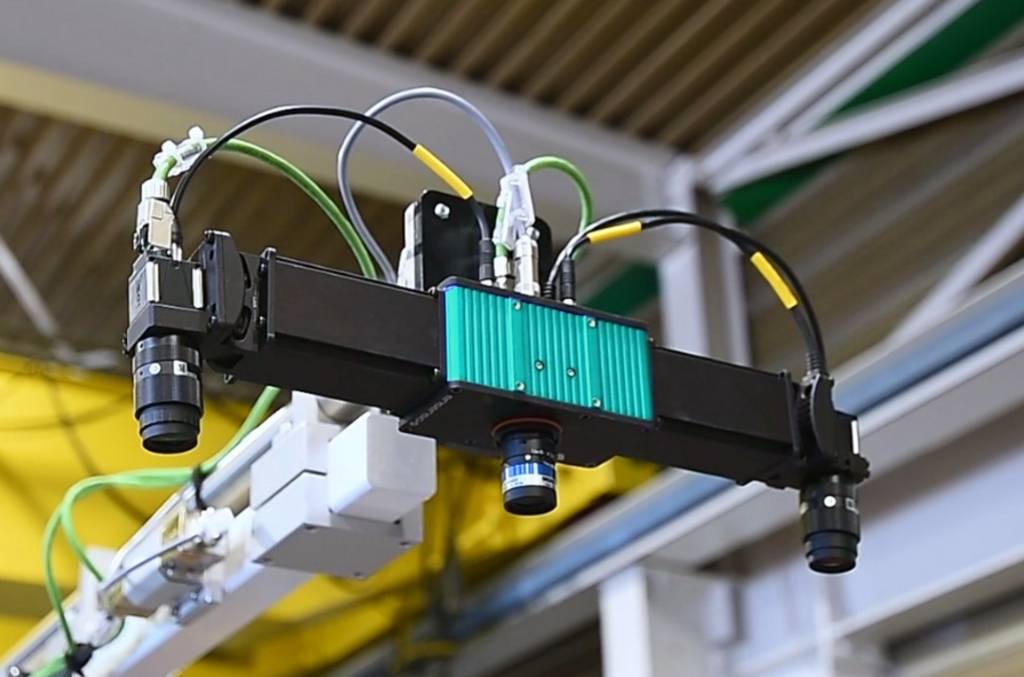
Formbasiertes Antastverfahren
Grundlage des Systems ist der DeepScan 3D Sensor. Dieser Stereosensor ist oberhalb der Depalettierstation installiert und nimmt Bilder der Paletten mit den darauf gestapelten KLT mit Hilfe eines Projektionsverfahrens auf und berechnet daraus eine 3D-Punktewolke. Dabei setzt OSC 6D zur optischen 3D-Lagebestimmung auf ein formbasiertes Antastverfahren. Anstelle von Kanten, Löchern oder anderen prägnanten Objektmerkmalen wird die geometrische Außenkontur eines Bauteils oder Werkstücks ganz oder teilweise verwendet, um dessen Position bzw. Lage und Orientierung zu ermitteln. Durch ein spezielles 3D-Matching mit CAD-Referenzdaten kann das System die tatsächliche Bauteillage zur Führung beliebiger Handhabungseinheiten wie beispielsweise eines 6-Achs-Roboters präzise berechnen.
„Nach einer Höhenauswertung der Punktewolke kann das System eine zuverlässige Aussage darüber treffen, ob sich KLTs auf der Palette befinden“, erläutert VMT-Produktmanager Matthias Fiedler. „Im nächsten Schritt wird dann die oberste Schicht der Punktewolke in ein höhenkodiertes Grauwertbild umgewandelt und die Ecke eines Kleinladungsträgers aus einer definierten Suchrichtung ermittelt. Ist diese gefunden, so sucht das System mit einem Kantenerkennungs-Tool in X- und Y-Richtung nach den KLT-Rändern. Anhand der so gewonnenen Kantenlängeninformation identifiziert das System eindeutig den aktuellen Kistentyp und seine Orientierung und verfügt somit über die Information, ob die Kiste in 0°- oder 90°-Lage auf der Palette steht.“
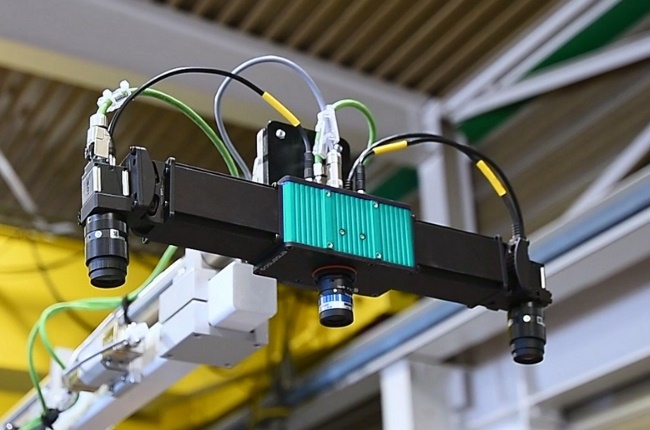
Spezieller Multifunktionsgreifer
Ohne die Aufnahme weiterer Bilder findet eine nachfolgende Prüfung in definierten Suchbereichen die Greifpunkte der Kiste und erkennt dabei auch eventuelle Fremdkörper. Als Ergebnisse liefert das VMT-System alle Informationen zum Kistentyp, den Kistenmittelpunkt sowie die 3D-Positionen der Greifpunkte an den Roboter der Anlage, der den ersten Kleinladungsträger somit zuverlässig von der Palette nehmen kann. „Um die KLTs sicher an den dafür vorgesehenen Aussparungen aufnehmen zu können, haben wir einen speziellen Multifunktionsgreifer entwickelt, der seine Aufnahmemechanik je nach Kistentyp automatisch verfährt und dem Lochbild des nächsten Kleinladungsträgers anpasst“, so Matthias Fiedler. Der gesamte Ablauf wird so lange wiederholt, bis sich keine Kleinladungsträger mehr auf der Palette befinden. Damit ist das System bereit für die Abarbeitung der nächsten vollen Palette.
Eine Besonderheit der Lösung hebt Matthias Fiedler besonders hervor: „In der Regel arbeiten vergleichbare Anlagen zweistufig. Dabei erfolgt zunächst eine Bildaufnahme für die grobe Ausrichtung und in einem zweiten Schritt die Bestimmung der Feinposition des Greifers. Erst dann kann sicher zugegriffen werden. Diese Herangehensweise führt zu längeren Taktzeiten, ist aufwendiger und zudem kostenintensiver für den Anwender als unser KLT-Handling, das mit einem einzigen stationären 3D-Sensor alle erforderlichen Informationen erfassen kann.“ VMT bietet das 3D-Visionsystem OSC 6D einzeln an, übernimmt bei Bedarf jedoch auch die Planung, Realisierung und Inbetriebnahme kompletter Roboterzellen zur Depalettierung. Zudem passt das Unternehmen den Sensor optimal an die jeweiligen Anforderungen an.
Virtuelle Inbetriebnahme
Mit eigenentwickelten Softwaretools ist VMT in der Lage, komplette Handlingszellen wie Palettier-/Depalettiersysteme, ganze Anlagenkonzepte oder auch spezielle Sensoranordnungen auf Basis von CAD-Daten virtuell zu planen und per Simulation zu testen. Dies ist auch bei nachträglichen Erweiterungen von bestehenden Anlagen möglich und erlaubt es somit, Prüfaufgaben bereits vor der Fertigstellung der realen Anwendung offline anzulegen und zu testen. „Mit Hilfe einer solchen virtuellen Inbetriebnahme lässt sich der gesamte Verlauf eines Projekts bereits im Vorfeld sehr präzise und effektiv planen“, unterstreicht Matthias Fiedler.