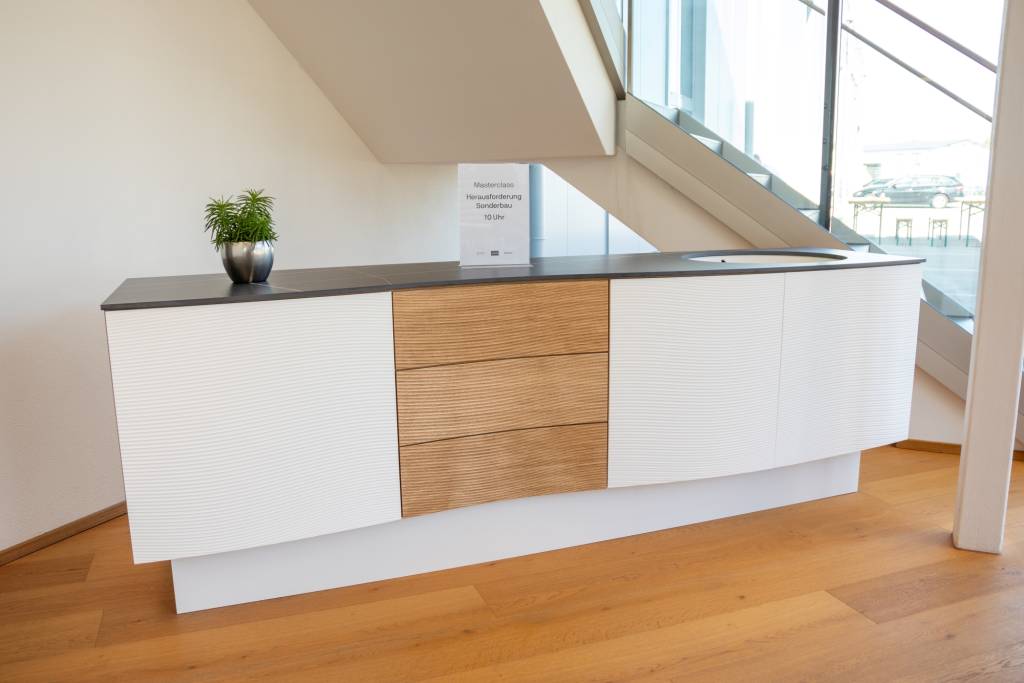
„Ich bin überwältigt“ – die außerordentlich positive Resonanz der Inside-Besucher hinterließ bei Cornelius Oheimb einen starken Eindruck. Seine erste Hausmesse als neuer Geschäftsführer von Biesse in Deutschland hat ihm und seinem Unternehmen eine ideale Plattform für den regen Austausch mit Kunden, Interessenten und Partnern geboten. „Während der intensiven Beratungsgespräche konnten wir zahlreiche Fragen der Gäste en Detail beantworten und ihnen viele neue Impulse für ihre Produktion vermitteln. Das war für alle Seiten äußerst gewinnbringend.“
Das fachkundige Publikum ergriff die Gelegenheit beim Schopfe und informierte sich ausgiebig über intelligente Maschinenlösungen sowie innovative Software für den Holz- und Kunststoffbereich. Das Thema Automatisierung spielt dabei eine wichtige Rolle und steht für die Zukunft im Maschinen- und Anlagenbau – und bildete folglich einen Schwerpunkt der Messe. Die bedienerfreundliche und lasergesteuerte Positionierhilfe der Rover A FT sowie die Rückführung zum leichteren Be- und Entladen der Brema Eko zeigten anschaulich den aktuellen Stand und die Möglichkeiten in diesem Bereich. Natürlich wurden nicht nur diese beiden Nesting- und Bohrmaschinen, sondern auch die dreizehn anderen, kontinuierlich auf Hochtouren laufenden CNC-Bearbeitungs- und Plattenzuschnittzentren, Kantenanleim-, Kalibrier- sowie Schleif- und Bohrmaschinen auf der 1.600qm großen Aktions- und Ausstellungsfläche inspiziert und getestet.
Ein wichtiges Utensil haben die Besucher zusammen mit den Experten von Biesse auf dem Nesting-Bearbeitungszentrum Rover A FT sowie der Breitbandschleifmaschine S2 hergestellt: Grillzangen aus Esche. Diese wurde bei phantastischem Wetter während der Mittagszeit im Außenbereich gleich auf Ihre Praxistauglichkeit getestet. Ein Food Truck sorgte zusätzlich für ausreichend Stärkung.
Bild: BIESSE Deutschland GmbH Stefan Katzer, Gründer und Geschäftsführer von Atmos – Bild: Biesse / Atmos
Masterclass: Herausforderung Sonderbau
Für Oheimb trugen die sechs vor Ort vertretenen Partnerfirmen für Präzisionswerkzeuge, Schleifmittel, Klebstoffe und Software mit ihren auf die Maschinen von Biesse abgestimmten Lösungen einen maßgeblichen Teil zum gelungenen Event bei. „Dieses Jahr stand ein besonderer Programmpunkt auf der Agenda: zum ersten Mal haben wir gemeinsam mit unserem CAD-CAM Softwarepartner Moldtech und den Spezialisten für Vakuumpressen von Atmos eine Masterclass mit dem Thema „Herausforderung Sonderbau | Vom Konzept zur Realität“ veranstaltet. Die wissbegierigen Teilnehmer haben viel neuen Input über typische Anforderungen im Sonderbau erhalten und können nun mit ihren neu gewonnenen Kenntnissen konvexe, konkave, reliefgefräste und tiefgezogene Elementen einfach in die Realität umsetzen.“ Einen Video-Rückblick über die Masterclass ist auf dem YouTube-Kanal von Biesse zu finden: youtu.be
Katharina Schaf trägt im deutschsprachigen Raum die Verantwortung für das Marketing von Biesse und weiß über die aktuellen Entwicklungen und die Erfordernisse des Marktes Bescheid – ein guter Grund, sich als eine von insgesamt 60 Teilnehmern in einen der ausgebuchten Workshops über die Herausforderungen im Herstellungsprozess einzureihen. Auch branchenkundige Profis wie sie lassen sich von der realistischen Umsetzung noch mitreißen: „Es war sehr spannend den Entstehungsprozess von der Konstruktion bis zum fertigen Produkt inklusive Programmierung sowie Erstellen und Aufspannen der Gegenformen selber zu erleben und zu gestalten. Wir haben am PC mit der Software unseres Partners Moldtech, übrigens beispielhaft für die typischen Anforderungen im Sonderbau, einen Waschtisch mit einer geschwungenen Front und einem tiefgezogenen Waschbecken konstruiert, ihn anschließend an einer unserer Selco-Sägen aufgeteilt und mit der Rover gefräst. Danach kam unser Partner für Vakuumpressen ins Spiel und wir haben mit dem Vorheizer und der Formstation von Atmos unser Werkstück tiefgezogen. Abschließend stand noch die Erstellung der Reliefstruktur auf einer unserer CNCs auf der Agenda.“
Gründer und Geschäftsführer von Atmos
Für Biesse war die Inside ein voller Erfolg. Als den Höhepunkt der diesjährigen Hausmesse erlebten sowohl die Besucher als auch der Veranstalter den Workshop über die Herausforderungen im Sonderbau, in dem die Teilnehmer den „Werdegang“ eines Werkstücks von der Konzeption bis zum fertigen Produkt aktiv erleben und gestalten durften. Ein guter Grund Stefan Katzer, den kreativen Kopf von Atmos, ein paar Fragen zu stellen.
Herr Katzer, Sie haben über 20 Jahre Erfahrung im Vertrieb von Holzbearbeitungsmaschinen gesammelt, bevor Sie ihr junges, aber schon sehr erfolgreiches eigenes Unternehmen gegründet haben und mit Leidenschaft Vakuumpressen herstellen – nun waren Sie als Partner von Biesse auf der Inside – der Hausmesse des traditionsreichen und renommierten italienischen Maschinenherstellers – zu Gast. Wie kam es zu dieser Kooperation?
Die Kooperation kam durch unseren gemeinsamen Software-Partner Moldtech zustande. Während den Vorbereitungen zur Inside kam der Gedanke zu einem Live-Workshop auf. Da die Vakuumpresse eine ideale Ergänzung zum Bearbeitungszentrum ist, wurde ich als Partner mit ins Boot geholt.
Wollen Sie diese Partnerschaft zukünftig intensivieren und ausbauen?
Auf jeden Fall, denn die Zusammenarbeit war bereits während der Vorbereitung sehr angenehm und konstruktiv. Auch während der Inside herrschte eine gute Atmosphäre zwischen allen Partnerfirmen, was uns bei Atmos natürlich sehr wichtig ist. Schließlich nutzen wir die Atmosphäre ja auch in unserer Vakuumpresse.
Gemeinsam mit Biesse und den CAD-CAM Softwareanbieter Moldtech haben Sie als Spezialist für Vakuumpressen eine Masterclass mit dem Thema „Herausforderung Sonderbau | Vom Konzept zur Realität“ veranstaltet – was war Ihr Part bei dem Workshop?
Bei der Masterclass haben wir die thermoplastische Verformung von Mineralwerkstoff in der Vakuumpresse veranschaulicht. Hierfür haben wir das Frontteil des Waschtisches in unserer Vorheizstation auf die notwendige Temperatur erwärmt, und dann in unserer Vakuumpresse in Form gebracht. Für das Waschbecken wurde ein Mineralwerkstoff auf Acrylbasis erwärmt und tiefgezogen. Durch die Sublimation haben wir noch ein wenig Farbe ins Spiel gebracht und jeweils ein Waschbecken mit Marmoroptik und Hirnholzoptik individualisiert.
Wie schaut Ihr Resümee aus? Mit welchen Erfahrungen sind Sie aus Nersingen heimgekehrt?
Für mich war die Inside eine sehr gute Gelegenheit, mein junges Unternehmen und unsere Vakuumtechnik einem interessierten Fachpublikum zu präsentieren. Ich bin sehr dankbar, dass die Firma Biesse mir diese Möglichkeit gegeben hat.
Apropos Inside – wie sieht es Inside Atmos aus, mit welchen Innovationen dürfen wir in Zukunft rechnen?
Die ersten drei Jahre mit Atmos haben mir gezeigt, dass der Wunsch nach Individualisierung in vielen Branchen einen immer größeren Stellenwert einnimmt. Aus diesem Grund habe ich ein Forschungsprojekt angestoßen, welches diese Individualisierung mit Nachhaltigkeit in Einklang bringt. Das Forschungsprojekt wird im Frühjahr 2024 beginnen und zu gegebener Zeit berichte ich Ihnen gerne von unseren Fortschritten.