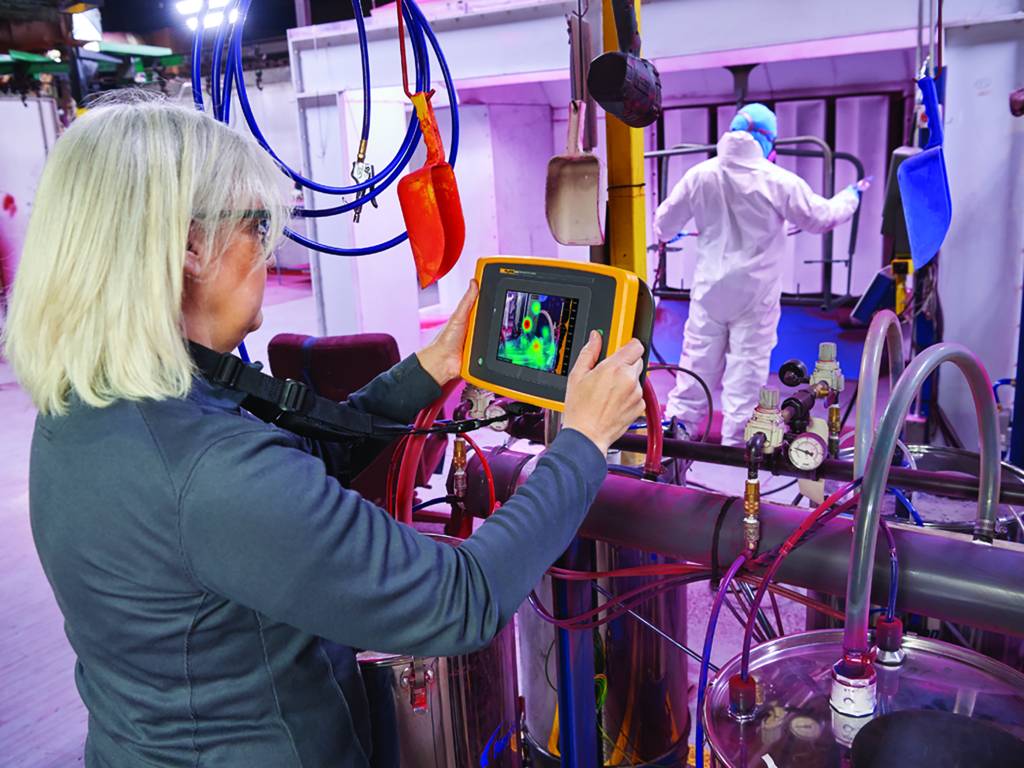
Dazu muss zunächst ein Profil der Anlage erstellt werden: Wie viele Motoren, Kompressoren, welche Größe und welche Steuerungen sind vorhanden? Dann muss der Energieverbrauch über alle Betriebszyklen und den wichtigsten Verbrauchern aufgezeichnet werden. Geprüft werden muss außerdem, ob alle Komponenten im Anlagenprofil identifiziert sind. Diese Analyse der Ausgangssituation ist von entscheidender Bedeutung, wenn es darum geht, Probleme mit der Effizienz und Qualität der in einer Industrieanlage verbrauchten Energie und Leistung zu lösen. Das bedeutet:
Ü Feststellen, wo und wann Energie verbraucht wird.
Ü Parameter über einen Zeitraum messen, protokollieren und vergleichen.
Ü Mobile Lösungen verwenden, um Probleme und Energieverschwender in der Hauptschalttafel zu identifizieren.
Ü Das Energieprofil des Anlagenbetriebs über einen Tag, eine Woche oder einen Monat vergleichen.
Ü Qualität der Energie überprüfen.
Ü Ausfallzeiten vermeiden und rechtzeitig mit einem Wartungsplan reagieren.
Ü Probleme mit der Netzqualität beheben, bevor es zu Schäden kommt.
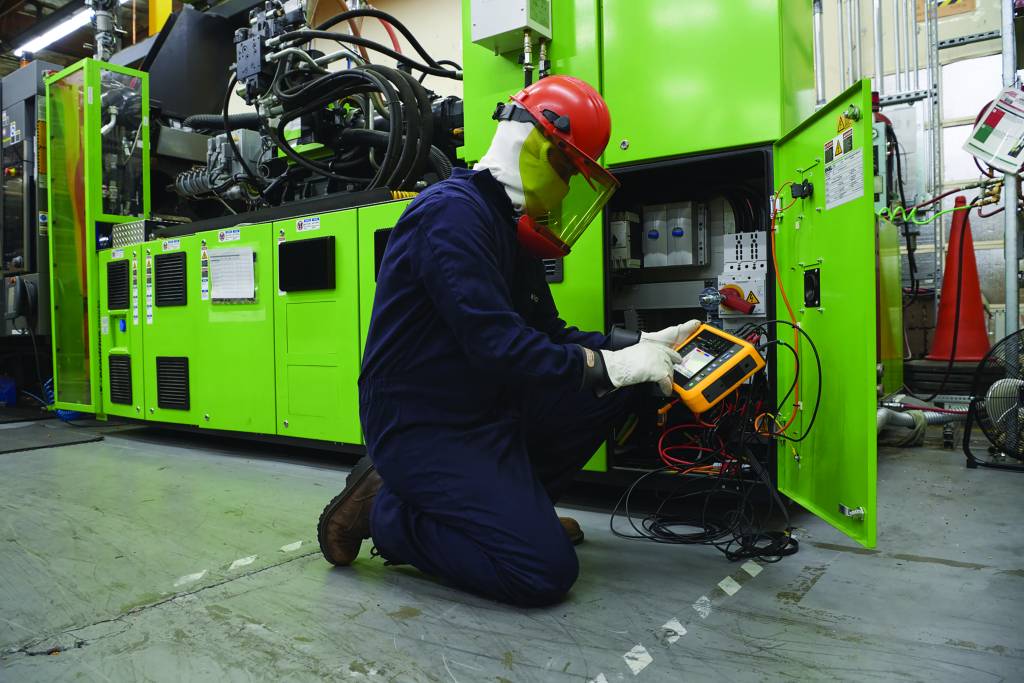
Höchstleistung und Netzasymmetrie
Energieeffizienz bedeutet in der Praxis u.a., zu überwachen, ob Maschinen mit maximaler Leistung laufen und ob Motoren und Antriebe über- oder unterlastet sind. Betriebs- und Produktionsleiter können die Energieverluste von Druckluftkompressoren, Prozess- und HLK-Anlagen bewerten, indem sie die Netzqualität bei jeder Gelegenheit überwachen und optimieren. Es gibt viele Möglichkeiten, wie Anlagen beschädigt werden oder korrodieren können. Oft sind die Gründe für das menschliche Auge unsichtbar und führen zu Energieverschwendung, ohne dass die Ursache oder das Ausmaß der Verschwendung erkennenbar ist.
In einem symmetrischen Dreiphasensystem müssen die Phasenspannungen und -ströme in Amplitude und Phase entweder gleich oder sehr nahe beieinander liegen. Jede Unsymmetrie in diesen Bereichen kann zu verminderter Leistung oder sogar zu vorzeitigem Ausfall führen. Schlechte Motorleistung wird durch Gegen-EMK und vorzeitigen Motorausfall verursacht, da die Asymmetrie eine übermäßige Erwärmung der Wicklungsdrähte verursacht. Die größten potenziellen Kosten entstehen durch den Austausch von Motoren, Umsatzeinbußen aufgrund des Auslösens des Stromkreisschutzes und die damit verbundenen Ausfallzeiten und Arbeitskosten zur Behebung des Problems. Unsymmetrien wirken sich auch auf die Energiekosten aus, da sie die Motorleistung verringern.
Eine der Möglichkeiten, Probleme mit Spannungsasymmetrien frühzeitig zu erkennen, ist die Messung der Spannung am Anschluss an das öffentliche Stromnetz (Netzeingang). Nach der Netzqualitätsnorm EN50160 darf die Spannungsunsymmetrie als Verhältnis von Schein- zu Wirkspannungsanteil am gemeinsamen Kuppelpunkt maximal 2% betragen. Ist die Spannung am Netzeingang nicht symmetrisch, so ist die Leistung in der gesamten Anlage unsymmetrisch und muss vom Netzbetreiber so schnell wie möglich korrigiert werden.
Asymmetrien können bei einer einzelnen Last oder einem Zweig der elektrischen Infrastruktur auftreten, z.B. bei einem Elektromotor oder sogar bei einer Reihe von Motoren. Es wird daher empfohlen, die Eingangsspannung und den Eingangsstrom zu überprüfen, wobei die Asymmetrie dieser beiden Parameter 2 bzw. 6% nicht überschreiten sollte. Die Stromasymmetrie ist eine direkte Folge der Spannungsasymmetrie, und wenn die Spannung symmetrisch ist, wird die Stromasymmetrie durch die Asymmetrie der Lasten verursacht.
Netzqualität
Schlechte Netzqualität kann zu unvorhersehbarem Verhalten von Produktionsanlagen und sogar zu deren vorzeitigem Ausfall führen. Ohne regelmäßige Überprüfung der Netzqualität können Probleme mit Motoren, Kabeln, Transformatoren, Kondensatorbatterien und Schalttafeln auftreten. Durch die Möglichkeit, die Netzqualität im Rahmen eines routinemäßigen Wartungsprogramms zu überprüfen, lassen sich potenzielle und bestehende Probleme erkennen und beheben, bevor sie zu Ausfällen und Produktionsausfällen führen.
Wenn in einer Produktionsanlage neue, komplexe Maschinen installiert werden, die das dynamische Verhalten des Werksnetzes verändern, führt dies ebenfalls zu einer Beeinträchtigung der Netzqualität. Mit steigender Komplexität einer Produktionsanlage nimmt auch die Wahrscheinlichkeit zu, dass schlechte Netzqualität zu einem Problem wird. Um dieser Komplexität entgegenzuwirken, ist eine einfache und sichere Analyse der Netzqualität erforderlich. Im Idealfall sollte der Prozess nicht viel Zeit des Personals in Anspruch nehmen. Auch weniger erfahrene Wartungstechniker sollten die Inspektionen problemlos durchführen und Berichte erstellen können.
Oberwellen, Spannungseinbrüche und -Spitzen
Hersteller können z.B. mit dem Netzqualitätsanalysator der Serie 1770 von Fluke ihre Produktivität und Effizienz steigern. Das Gerät misst und analysiert automatisch Netzqualitätsparameter wie Spannungs- und Stromunsymmetrie, Transienten, Flicker, Oberschwingungen, Einbrüche und Spitzen. Das Gerät erkennt schnelle Spannungstransienten und hilft, deren Auswirkungen zu reduzieren, um Geräteausfälle zu vermeiden. Die Daten lassen sich über Wi-Fi, Ethernet oder ein GSM-Netz weiterleiten.