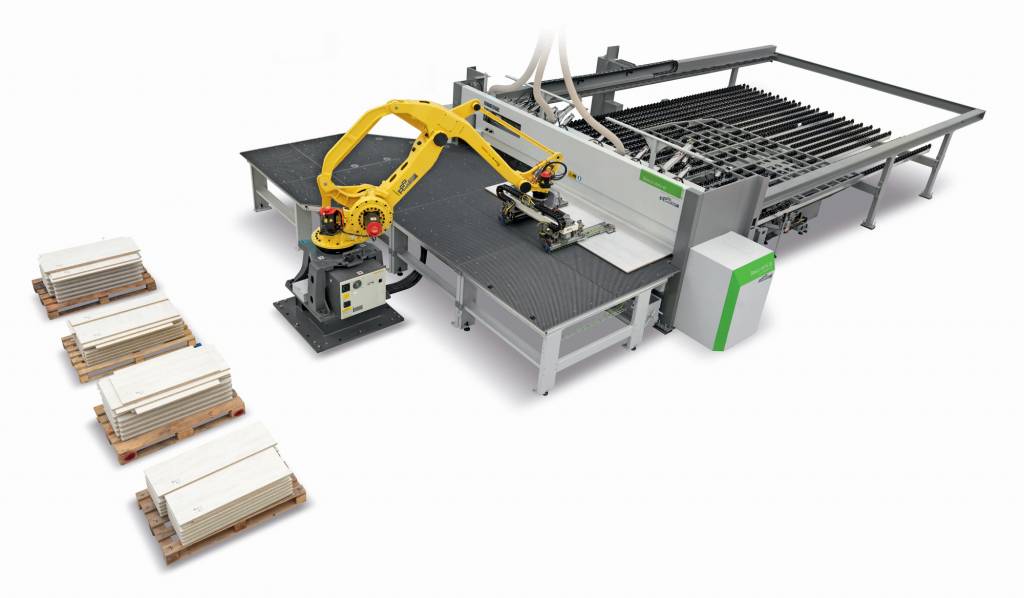
Als Spezialist für Holzbearbeitungsmaschinen optimiert Biesse kontinuierlich seine ausgeklügelten Maschinenlösungen und investiert in die Entwicklung neuer Technologien. Mit dem jüngsten Spross im Komplettsortiment, der Selco WN 6 ROS, bietet der Hersteller mit Sitz in Pesaro eine flexible Plattenaufteilsäge, die mit 1.800 Teilen pro Schicht äußerst effektiv und rentabel produziert. Die komplette Anlage besteht aus dem Flächenlager Winstore von RBO, der Selco WN6 ROS (Robotically Operation System) und einem Twin Pusher (TP). Biesse passt das System individuell an die Hallengröße und die jeweiligen Kundebedürfnisse wie Plattenmaße, Typ, Geschwindigkeit, integrierte Nesting-Maschinen oder Sägen an. Die einzelnen Bausteine lassen sich außerdem leicht in vorhandene, automatisierte Prozesse integrieren.
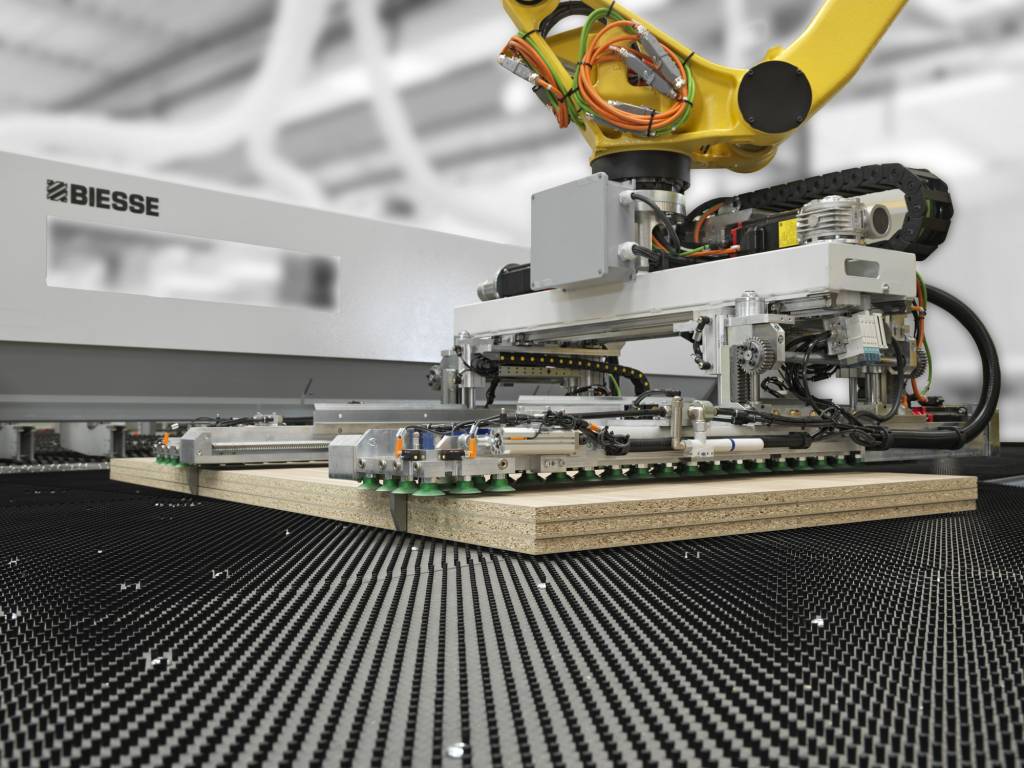
Effizienz von Anfang an
Winstore übernimmt das komplette Handling vom Lager bis zu den Maschinen. Die physikalische und logistische Verknüpfung erreicht mit dem von RBO entwickelten System eine neue Produktivitätsebene. Zur Biesse Group gehörig, hat sich das Unternehmen auf die Herstellung von Robotern zur Automatisierung und Anlagen für das Plattenhandling spezialisiert. Alternativ kann das Beschicken oder Zuführen auch mittels Hubtisch oder dem X-Feeder aus dem Biesse-Programm erfolgen. Vor der Verarbeitung werden die angeforderten Werkstücke abhängig vom Schnittplan und Auftrag auf dem Vorlegeplatz mit Barcodes etikettiert. Beim Einfördern in die Maschine vermeidet das spezielle Klemmen- bzw. Clamping-System ihr Verrutschen. Anschließend sorgt ein Drehtisch für die gewünschte Positionierung der Platten für den Kopfschnitt.
Als ausgereifte technologische Lösung spielt die Selco ihre Stärken in Kombination mit dem integrierten Roboter ROS und dem Twin Pusher, einem zusätzlichen Schieber, aus. Dadurch kann jeder Auftrag zu vordefinierten Zeiten bei gleichbleibendem Qualitätsstandard ausgeführt werden. „Unsere Kunden profitieren von einer deutlich verbesserten Effizienz und Kontinuität in der Produktion. Das Zusammenspiel der aufeinander abgestimmten Komponenten erleichtert die tägliche Arbeit erheblich. Die anwendungsgerechte Konfiguration erfordert keine speziellen Programmierkenntnisse“, erläutert Selco Brandsalesmanager Ingo Reineke. Anstelle eines Bedieners übernimmt ROS das Handling mit bis zu drei Platten. Bis zum Abschluss der Bearbeitung findet der Arbeitszyklus vollautomatisch statt. Stillstandzeiten reduzieren sich ebenso wie das Risiko von Beschädigungen am Material.
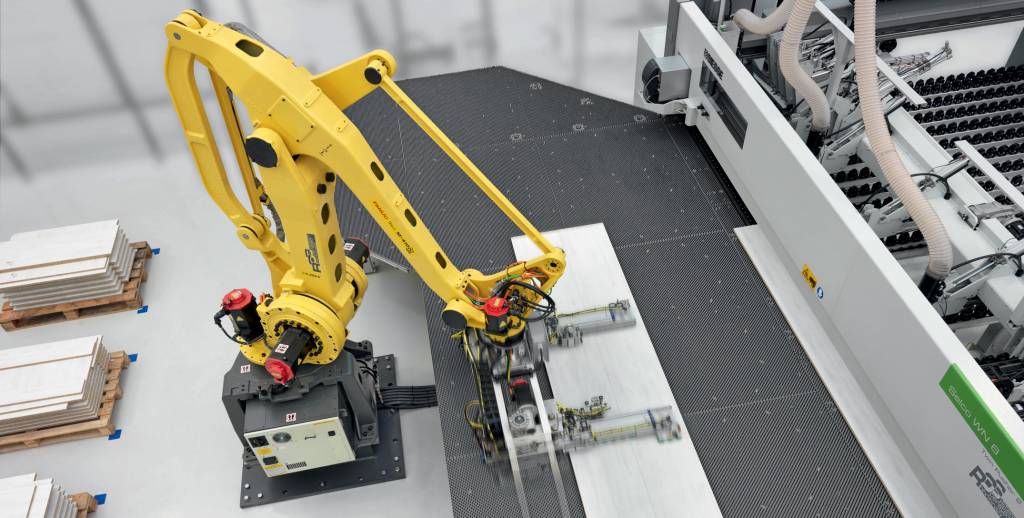
Voll Integriert Robot ROS verrichtet sämtliche Arbeiten vom Längsschnitt über den Querschnitt bis zur Platzierung am Winkelanschlag. Der Robot dreht einzelne Platten oder komplette Stapel, legt sie wieder an und sortiert sie abschließend Stück für Stück auf den richtigen Abstapelplatz. Wahlweise fördert das robotergesteuerte System die geschnittenen Bauteile automatisch auf eine angebundene Rollenbahn für den Weitertransport. Mit Unterstützung des eingebundenen Twin Pushers nimmt ROS simultan auch zwei Werkstücke gleicher oder unterschiedlicher Größe auf. In Kombination machen beide Systeme den Zuschnitt noch effizienter, da mehrere Streifen – auch stapelweise – neben einander liegen können. Alternativ positioniert TP den letzten Streifen des Schnittplans für die Bearbeitung und der Hauptschieber rekrutiert schon die nächste Aufgabe vom Vorlegeplatz. Fertige Teile, die von der Reihenfolge her noch nicht zum Absortieren bereit sind, lagert der Schieber auf einer eigenen Warteposition zwischen. Reste werden von ROS auf einen vorab definierten Stapel bzw. eine zusätzliche Parkstation ausgeschleust. Für eine spätere Verarbeitung lassen sie sich manuell wieder zuführen. Während der abschließenden Reinigung der Werkstücke mit Druckluft können die fertigen Teile auch alternativ zum Labeln auf dem Vorlegeplatz etikettiert werden. Optimierung 4.0
Mit der Anbindung an die passende ERP und CAD/CAM-Software stehen komplette Softwarelösungen für die durchgehende Industrie 4.0 Fertigung zur Verfügung und bieten die entsprechenden Module für alle Arten der Bearbeitung. Mit der hausintern entwickelten Optiplanning verfügt Biesse über eine perfekt abgestimmte Optimierungssoftware für Schnittpläne. Ausgehend von den zu produzierenden Werkstücken und den verfügbaren Platten berechnet die benutzerfreundliche Software die ideale Lösung durch maximale Verringerung des Materialverbrauchs, der Schnittzeiten und Produktionskosten.
www.biesse.com