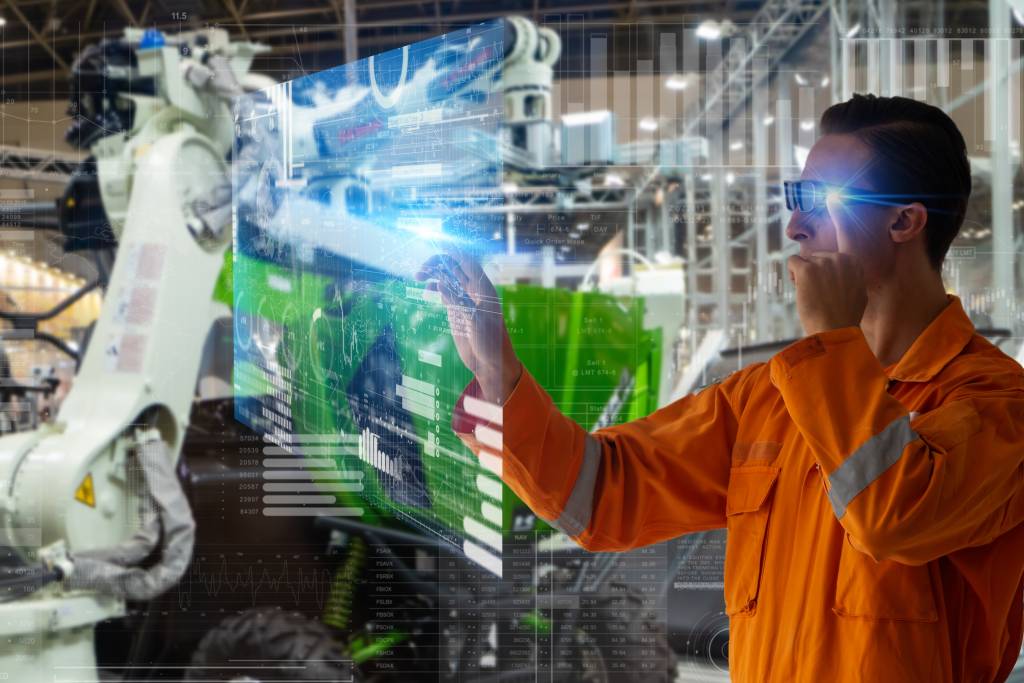
Das Konzept des digitalen Zwillings beschreibt die virtuelle Abbildung von physischen Objekten. Eigenschaften, die hier in Datenstrukturen wiedergegeben werden, sind etwa die Beschaffenheit oder Form, gleichermaßen allerdings auch Verhaltensweisen oder Zusammenhänge. Zu den wesentlichen Charakteristika eines digitalen Zwillings gehören die Sensoren zur Zustandsermittlung, die Konnektivität zur Datenübertragung, definierte Datenstrukturen zur Abbildung des Objektes und die Visualisierung. So vermag das Konzept neben einem 3D-Modell auch ein Verhaltens-, Funktions- und Zustandsmodell für den Anwender abzubilden und nutzbar zu machen. Der digitale Zwilling ist dabei nicht auf materielle Objekte beschränkt, sondern kann auch auf Prozesse und Verfahren angewendet werden.
Nutzen von Beginn an
Der Einsatz digitaler Zwillinge setzt bei bedarf schon früh im Produktentstehungsprozess an. Indem bereits während der Design- und Entwicklungsphase ein virtuelles Abbild des Objektes geschaffen wird, kann das spätere Verhalten des Produkts weitaus genauer vorhergesagt werden. Die Entwicklung digitaler Abbilder vereinfacht die Zusammenarbeit an einem Projekt und die gemeinsame Arbeit zur Optimierung. So ersparen sich Unternehmen beispielsweise die Produktion von unausgereiften Prototypen. Gleichzeitig helfen virtuelle Modelle von bereits gefertigten Produkten dabei, die Lücke zwischen Design und Fertigung zu schließen und auf Basis der gesammelten Daten aus einer früheren Produktion in Zukunft bessere Produkte zu schaffen. Digitale Zwillinge erlauben so Einblicke in mögliche Verbesserungen und bessere Folgegenerationen.
Mehr Transparenz
Der industrielle Mittelstand kann von Digital Twins besonders während der Produktion profitieren – Stichwort Transparenz. Digitale Zwillinge zeigen an, welche Schritte der Wertschöpfungskette schon vollzogen wurden oder noch anstehen. Daraus ergibt sich eine Gesamtübersicht über die verschiedenen Produktionsparameter und Laufzeiten. So lassen sich Produktions- und Lieferzeiten präziser vorausberechnen, Engpässe im Ablauf feststellen und Prozessoptimierungen umsetzen. Instandhaltungsintervalle können besser prognostiziert werden und im Falle eines plötzlichen Ausfalls kann eine Fehleranalyse von jedem Standort aus initiiert werden. Das bedeutet auf Dauer, dass Risiken bereits früher erkannt werden und Unternehmen diese vorab reduzieren können, anstatt im Nachgang Krisen zu bewältigen. Herkunft und Qualität der Materialien und Rohstoffe kann stets kontrolliert und auf ihren Ursprung zurückverfolgt werden. Teams können so ihre Entscheidungen nicht länger auf Vermutungen, sondern auf Fakten zurückführen. Zudem erfahren Hersteller, wie ihre Produkte nach dem Verkauf eingesetzt werden und können daraus nützliche Erkenntnisse für zukünftige Weiterentwicklungen ziehen.
Services generieren
Oftmals fehlt es Herstellern an Anhaltspunkten darüber, wie ihre Produkte nach der Produktion und dem Vertrieb genutzt werden, bis es zur Kontaktaufnahme mit dem Servicecenter kommt, weil Probleme entstehen oder Maschinen komplett ausfallen. Nachdem diese punktuell auftretenden Probleme behoben sind, geht es zurück zur Ausgangslage und der Anbieter muss erneut ohne Informationen darauf hoffen, dass das eigene Produkt den Anforderungen des Marktes gewachsen ist. Mithilfe digitaler Zwillinge kann das Produkt kontinuierlich gemonitort und in der Konsequenz daraus auch ein Service angeboten werden. Das führt nicht nur zu einer besseren Erfahrung für den Kunden, sondern auch zu wichtigen Einblicken in den Lebenszyklus des Produktes und mögliche Verbesserungen.