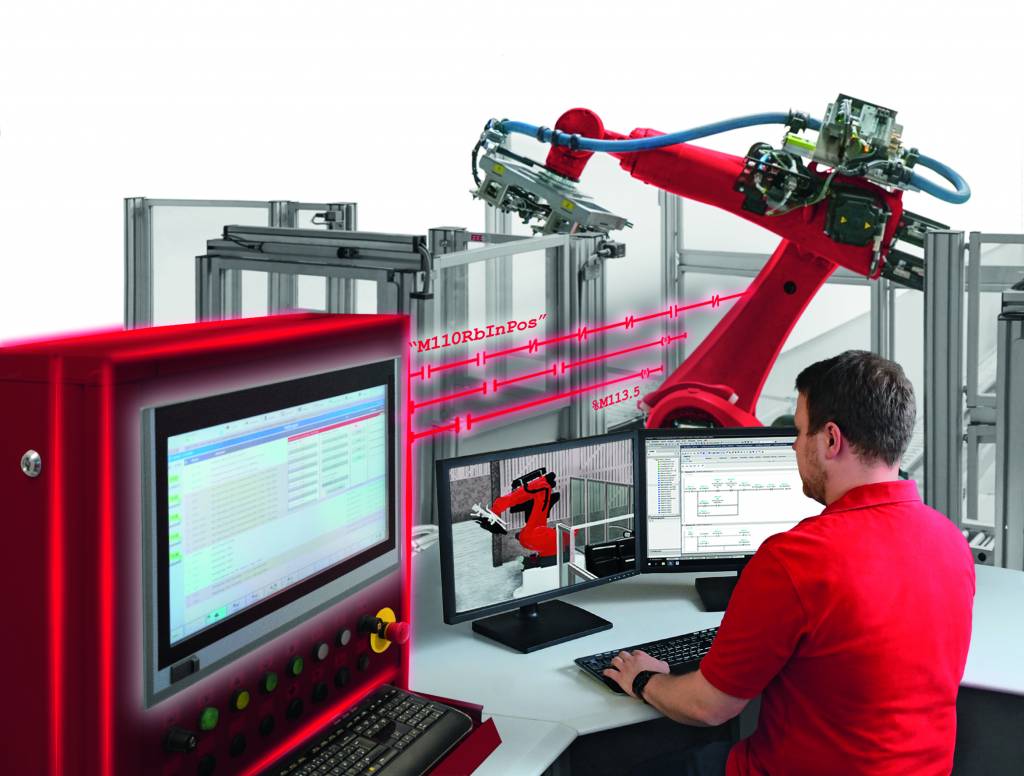
Das Ziel einer virtuellen Inbetriebnahme (VIBN) ist das frühe Feststellen und Beheben von Fehlern sowie das Absichern des Zusammenspiels von Anlagenmechanik und Steuerungssoftware. Dabei löst sich dieser Prozess von den sequenziell geprägten Workflows der meisten Engineering-Organisationen und verändert sich zu einer parallelen Bearbeitung, um Bearbeitungszeiten und Kosten zu sparen.
Von der Anwendung abhängig
Bei einer VIBN werden Simulationsmodelle verwendet, die das reale Verhalten der Anlage abstrahieren, um möglichst realitätsnahe Ergebnisse zu liefern. Die Wahl der Modellierungstiefe ist von der Anlage abhängig, die simuliert werden soll, und muss in einer weitläufigen Intralogistik-Anlage mit 1.000 Antrieben zwangsläufig eine andere sein, als bei einer Bearbeitungsmaschine mit komplexen mechanischen Baugruppen, einer hohen Dichte an Sensorik und Aktorik sowie parallelen, kleinteiligen Bearbeitungsschritten. Dabei hat die Modellierungstiefe keinen Einfluss auf die Anbindung des Modells an die Steuerung über Software in the Loop (SIL) oder Hardware in the Loop (HIL). Ein hoher Detaillierungsgrad erhöht den Aufwand der Modellerstellung, weshalb man beim Aufbau des Modells der Leitlinie folgen sollte: „So genau wie nötig, so idealisiert wie möglich“. Eine VIBN kann die reale Inbetriebnahme zwar nicht ersetzen, da es nach wie vor Tätigkeiten gibt, die nur an der realen Anlage möglich sind. Aber eine VIBN sichert das Engineering und die Programmierung ab, verkürzt die Projektzeit, reduziert die Inbetriebnahmekosten, erreicht eine höhere Anlagenverfügbarkeit im gesamten Inbetriebnahmeprozess und trägt entscheidend zu dessen Vereinfachung bei.
An Daten kommen
In der Regel bilden die Daten aus der Mechanik-Konstruktion die Basis für den Modellaufbau. Je nach Engineering-Prozess stehen diese Daten in verschiedenen Applikationen und unterschiedlicher Qualität zur Verfügung. Sind brauchbare CAD-Daten erst in einer fortgeschrittenen Engineering-Phase verfügbar, bietet sich die Arbeit mit idealisierten Modellen an, um trotzdem einen frühzeitigen Start der Softwareentwicklung sicherzustellen. Zudem sollte die Nutzung anderer Datenquellen – wie Excel, Datenbanken, Visio-Layouts – als Basis für die Modellerstellung möglich sein, um früh ein belastbares Modell zu erhalten. Das Anlagenmodell sollte sich möglichst automatisiert aus den vorhandenen Daten erstellen lassen. Simulationslösungen mit offenen Schnittstellen (Application Programming Interface, API) können diesen Schritt vereinfachen. Mittels eingebetteter Makros im Quellsystem werden dabei alle Elemente analysiert und mit den verfügbaren Informationen über die API an die Simulation übergeben. Werden Daten im Simulationsmodell geändert, können diese über die gleiche Schnittstelle auch bidirektional in das Quellsystem zurückübertragen werden.
Eigene Modelle erstellen
Das Verhaltensmodell hat die Aufgabe, das logische und zeitliche Verhalten der realen Betriebsmittel gegenüber den angeschlossenen Steuerungen zu simulieren. Die Modelle bestehen in erster Linie aus einzelnen Simulationsbausteinen der in der realen Anlage verwendeten Betriebsmittel. Bestenfalls verfügt die eingesetzte Simulationslösung über eine eigene Baustein-Bibliothek sowie über die Möglichkeit, eigene Verhaltensmodelle zu erstellen. Oftmals bieten Softwarehersteller die Modellerstellung auch als Dienstleistung an. Zudem gibt es bereits Hersteller, die z.B. Verhaltensmodelle für Antriebe oder Greifersysteme zur Integration in die Simulationsplattform bereitstellen. Existieren in einer bereits vorhandenen Simulationslösung Bibliotheken von Verhaltensmodellen, ist es vorteilhaft, diese auch in anderen Simulationsumgebungen in Form einer Co-Simulation nutzen zu können.