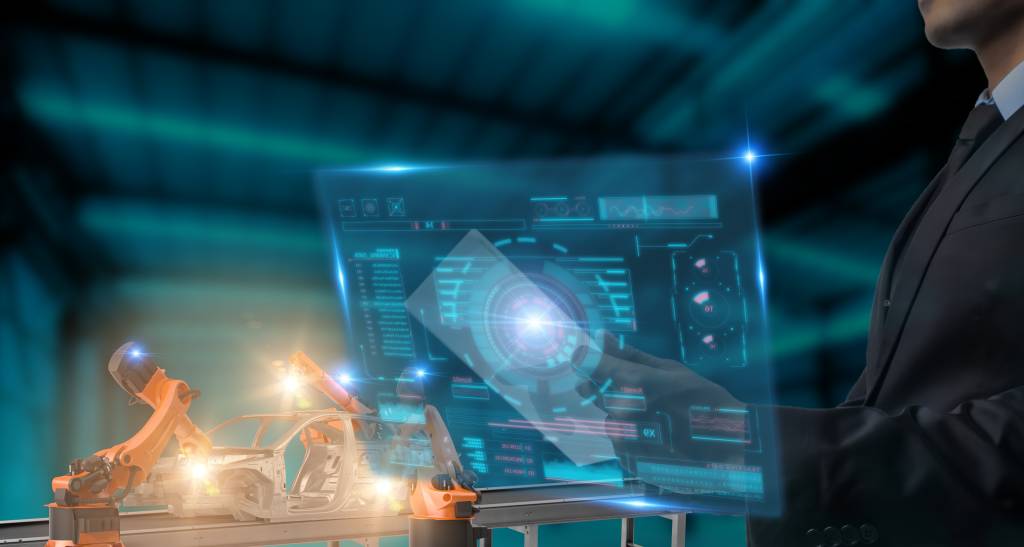
Mit Green Deal und Öko-Designrichtlinie will die EU die Digitalisierung von Produkten und Kreislaufwirtschaft durch standardisierte Daten fördern. Ein wichtiger Aspekt dabei ist der digitale Produktpass, der den Weg von einer linearen zur zirkulären Wirtschaft ebnen soll. Über den gesamten Produktlebenszyklus hinweg könnte der digitale Produktpass künftig über standardisierte Schnittstellen mit maschinell lesbaren Daten befüllt werden. Ein Produktpass startet im Engineering des Produktes, bezieht jedoch Herstellung, Nutzungsphase und Recycling konsequent ein. Dieses Umdenken wirkt sich auf das digitale Zusammenspiel aller Beteiligten in der Wertschöpfungskette aus. Um sich darauf vorzubereiten, können Unternehmen heute schon auf das Modell des digitalen Zwillings als standardisierte Verwaltungsschale von Eigenschaften der Objekte im Life Cycle setzen. So lassen sich relevante Daten sowohl aus Nachhaltigkeits-, als auch aus Automatisierungssicht sammeln.
Datenmodell für den Lebenszyklus
Die ersten Digital Twins (DT) entstanden bei der NASA als virtuelle Abbilder von Raumfahrtobjekten, deren Zustand nicht physisch überprüft werden konnten. Mittlerweile setzt sich das Konzept auf breiter Basis durch. Bosch etwa bekennt sich explizit zum digitalen Zwilling als wichtige Technologie rund um die Nachhaltigkeit und sieht sie als Paradigmenwechsel. Ein Digital Twin setzt sich aus drei wesentlichen Bestandteilen zusammen: Das physische Produkt im realen Raum, das virtuelle Produkt im digitalen Raum und die Datenverarbeitung, mit der beide Welten verbunden werden. Digitale Zwillinge können nicht nur Produkte abbilden, sondern auch Prozesse und Dienstleistungen. In der chemischen Industrie beispielsweise eignen sich Digital Twins für die Produktionsanlagen ebenso wie für Ausrüstung, darunter intelligente Flansche, Pumpen und Kondensatableiter.
Auf den Produktbetrieb fokussiert
In der Praxis sind viele kleine und mittelständische Unternehmen noch weit von solchen Projekten entfernt. Die IT-Landschaften prägen noch immer Datensilos, obwohl Daten für eine ganze Reihe von Zukunftsthemen die treibende Kraft sind. Das gilt für digitale Geschäftsmodelle und Services, die oft auf der Integration von IoT-Sensoren und KI-Analytik basieren. Digitale Services helfen etwa den Betreibern, Maschinen und Anlagen innerhalb profitableren Leitplanken zu fahren. So lässt sich Energie sparen, Ausschuss vermeiden oder mit vorausschauender Wartung für weniger Ausfälle und eine längere Produktlebensdauer sorgen. Zudem entsteht für Maschinen- und Anlagenbauer so ein Fenster in Richtung der nächsten Lebensphase des Produkts beim Betreiber. Dazu sollten sie jedoch ihren Fokus von der Entwicklung und Herstellung auf den gesamten Lebenszyklus ihrer Produkte ausdehnen – und damit auf den Digital Twin.
Intensive Verbraucher unerwünscht
Das demnächst von der EU geforderte Nachhaltigkeits-Reporting ändert für betroffene Unternehmen einiges. Ab 2026 verpflichtet die Corporate Sustainability Reporting Directive (CSRD) auch Mittelständler ab 250 Mitarbeitenden zur Erstellung eines Nachhaltigkeitsberichts. Viele Betreiber erkennen derzeit die Wichtigkeit, für eine Verbesserung der CO2-Bilanz die größten Verursacher in ihren Prozessen zu identifizieren. Hohe Energiekosten sind dabei ebenfalls ein Treiber. Hier gerät etwa Rotating Equipment wie Pumpen und Ventilatoren besonders in den Fokus, das jetzt perspektivisch einem Retrofit mit Sensorik unterzogen wird. So schätzt Steve Schofield vom Verband europäischer Pumpenhersteller Europumps, dass Pumpensysteme etwa ein Fünftel des weltweiten Stroms verbrauchen. Die Pumpen sind in der Industrie innerhalb der EU damit der größte Einzelposten. Er steht mit seinem Stromverbrauch von über 300 TWh pro Jahr für über 65 Mio. Tonnen CO2-Ausstoß. Bemerkenswert ist dabei, dass rotodynamische Pumpen in der Regel zu 20 bis 30 Prozent überdimensioniert sind – und rund 80 Prozent der installierten Basis ausmachen.