
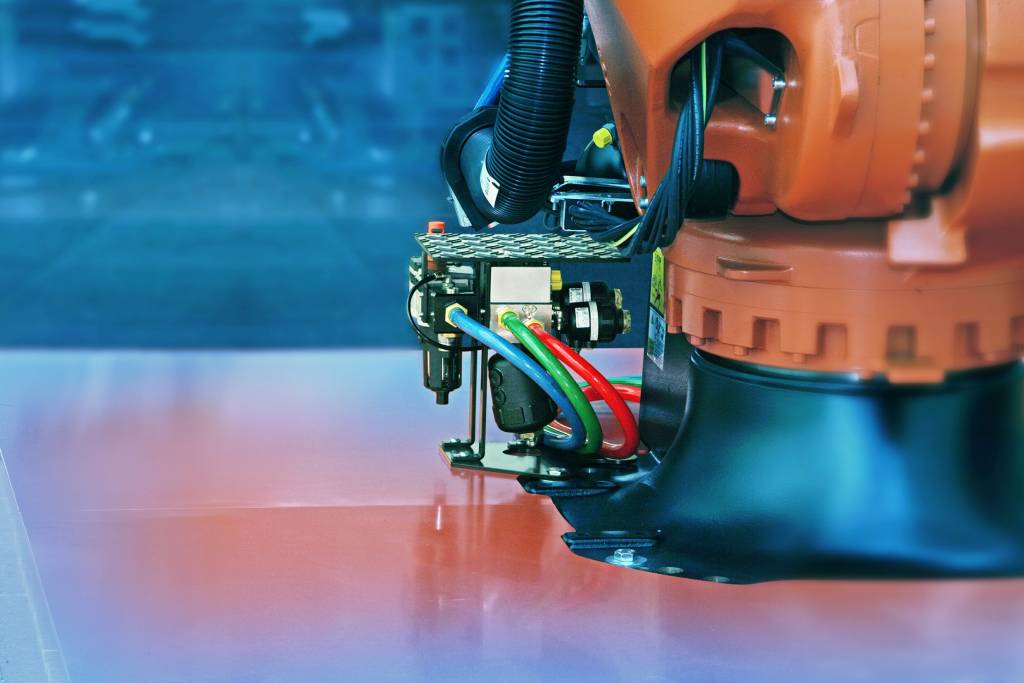
Platzsparende Montage
Für eine geregelte Schweißzangenkühlung hat Bürkert Fluid Control Systems deshalb schon vor einigen Jahren mit der Systemlösung Typ 8821 eine praxisgerechte Lösung entwickelt, die so kompakt ist, dass sie direkt neben der Versorgungsplattform des Roboters an der Bodenplatte Platz findet. Beim Schweißen wird der Roboter dann nicht durch das Kühlsystem in seinem Arbeitsbereich eingeschränkt, weshalb konventionelle Systeme oft anderorts untergebracht werden. Damit unterscheidet das System sich von den herkömmlichen, meist kühlschrankgroßen Lösungen. Die Anordnung an der Roboterbefestigungsplatte verkürzt zudem die wasserführenden Kühlschläuche zum Punktschweißwerkzeug. Die Regelung und die Abschaltungsüberwachung arbeiten dadurch wesentlich schneller als bei einer Anordnung weiter entfernt am Schutzzaun des Roboters. Eine manuelle Bedienung oder visuelle Überwachung des Kühlsystems entfällt, da alle Regelmerkmale und Überwachungsdaten per Feldbus am Bediengerät des Roboters oder der SPS eingestellt oder visualisiert werden können. Die kompakte Systemeinheit besteht aus Pneumatikmodul, Steuermodul mit integriertem Prozessregler und Kühlmittelmodul, die platzsparend aufeinander montiert sind. Die komplette Messtechnik ist im Steuermodul integriert, das gut zugänglich ist. Meist bleibt jedoch bei der Inbetriebnahme nicht viel zu tun, denn das System ist bereits werksseitig auf die gängigen Zweikreiszangen mit 16mm-Kappen voreingestellt. Maximalbegrenzung und Sollwert sind bereits hinterlegt. Nur in Sonderfällen werden andere Werte am Controller menügeführt manuell angepasst.
Kommunikation via Profinet
Der im System eingesetzte Durchflusssensor arbeitet unter Referenzbedingungen mit einer Wiederholgenauigkeit von ±0,4 Prozent vom Messwert bei einer Fließgeschwindigkeit zwischen 0,3 und 10m/s. Neben dem Durchflusssensor sind weitere Sensoren zur Druck- und Temperaturerfassung integriert. Das Steuermodul kommuniziert direkt mit der übergeordneten Robotersteuerung oder SPS. Bei der neuesten Variante der Systemlösung zur Schweißkappenkühlung ist das nun auch über Profinet möglich. Nicht nur die Offenheit für TCP/IP, sondern auch die auf Standard-Ethernet basierte Technik machen Profinet zu einer zukunftssicheren Architektur, die eine Basis für Industrie4.0-Konzepte schafft. So lässt sich z.B. die Anlagenverfügbarkeit steigern, indem die Prozessdaten nicht nur in der lokalen Steuerung verarbeitet werden, sondern auch in Cloud-Anwendungen für die Ferndiagnose sowie für Anpassungen zur Verfügung stehen. Die Systemlösung stellt dafür nicht nur die Profinet-Schnittstelle, sondern durch die zusätzliche Sensorik auch die entsprechenden Signale zur Verfügung.
Einfache Inbetriebnahme
Die Inbetriebnahme des Systems zur Schweißzangenkühlung ist simpel. Codierte Anschlusstechnik und farbige Schläuche erleichtern die Inbetriebnahme von Pneumatik- und Kühlmitteleinheit. Bodenanker sind für die Befestigung nicht notwendig. Zur Inbetriebnahme müssen die Luftversorgungsleitung an der Eingangsseite der Pneumatikeinheit mittels Absperrhahn geöffnet und die Druckluftverbindungen geprüft werden. Ist das System dicht und mit ausreichend Druck versorgt, kann die Kühlmitteleinheit in Betrieb genommen werden. Während des Betriebs lassen sich vier Systemmodi unterscheiden. Im Inbetriebnahmemodus sind alle Komponenten in der Stellung Hilfsenergieausfall; die Prozesseingangswerte stehen über Profinet zur Verfügung. Durch das Signal System Run von der Robotersteuerung oder SPS wird nun der Schweißkappenkühlprozess in Gang gesetzt und betrieben. Der Controller im Steuerungsmodul regelt den voreingestellten Sollwert aus. Mit Überschreiten des unteren Grenzwertes und nicht Überschreiten des oberen Grenzwertes wird ein Signal (Wasserfluss i.O.) generiert und eine LED zeigt den regulären Kühlbetrieb an. Im Hand- und Wartungsmodus können Einstellungen auch direkt vor Ort vorgenommen werden.