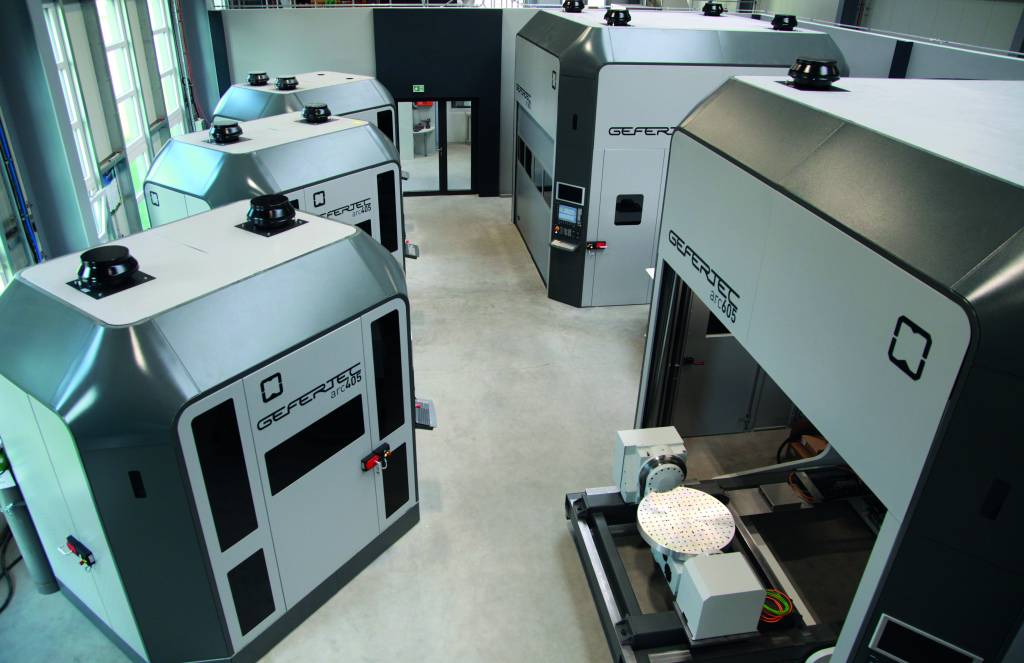
Beim WAAM wird der Werkstoff als Draht mittels Lichtbogenschweißen Schweißraupe für Schweißraupe auf eine Grundplatte aufgebracht. Dies bringt gleich mehrere Vorteile im Vergleich zu pulverbasierten Verfahren mit sich: Draht ist als Ausgangsmaterial deutlich günstiger, und die meisten Werkstoffe sind in Drahtform erhältlich. Zudem können sowohl das aufwändige Pulverhandling als auch die Vakuumtechnologie entfallen. Größter Vorteil ist jedoch eine hohe Aufbaurate, die durch das Verfahren erreicht wird. Je nach verwendetem Werkstoff kann diese bis zu 650cm³/h betragen.

Temperatur im Prozess kontrollieren
Das Berliner Unternehmen Gefertec entwickelt und baut Maschinen, die den WAAM-Prozess für den 3D-Druck von Metallen verwenden. Die arc-Maschinen, die es als 3- und 5-Achs-Variante in unterschiedlichen Größen gibt, integrieren Lichtbogenschweißtechnologie, CAM-Software und Werkzeugmaschine zu einer additiven Fertigungslösung. In der größten Ausbaustufe mit einem Bauraum von 8m³ können Bauteile bis zu 8.000kg gefertigt werden. Eine spezielle CAM-Software erzeugt aus den CAD-Daten des Werkstücks die Daten, mit denen die CNC-Steuerung die exakte Positionierung des Schweißkopfs vornimmt. Die Fertigung des endkonturnahen Werkstücks erledigt die Maschine dann vollautomatisch.
Temperaturen spielen im WAAM-Prozess eine wichtige Rolle, denn die Temperaturverteilungen im Werkstück und das Abkühlverhalten sind von entscheidender Bedeutung, um die Qualität des fertigen Bauteils sicherstellen zu können. „Im Betrieb der Maschine wird erst dann mit dem Aufschweißen begonnen, wenn die darunter liegende Lage auf eine bestimmte Temperatur abgekühlt ist“, erläutert Martin Lange, Mitarbeiter der Produktentwicklung bei Gefertec. Ist die Zwischenlage noch zu warm, führt das zu einem ungleichmäßigen Aufbauverhalten – die Schichtdicke würde zu stark variieren und die Geometrie des Bauteils nicht eingehalten. Die entsprechende Temperaturmesstechnik ist in der Maschine mit einem Pyrometer gelöst. Nach dem Abschluss einer Lage fährt der Schweißkopf zum Startpunkt der nächsten Lage, das Pyrometer misst dort die Temperatur des Bauteils. Erst wenn diese auf den voreingestellten Wert gesunken ist, arbeitet die Maschine weiter. „In den meisten Anwendungen haben wir für die Zwischenlagentemperatur einen Wert von 150 bis 200°C eingestellt“, sagt der Entwicklungsingenieur: „Dies ist für die Reproduzierbarkeit der Schweißnahthöhe optimal.“ In den arc-Maschinen, die Gefertec zukünftig ausliefert, sollen Pyrometer aus der CT-Serie von Optris zum Einsatz kommen. Diese haben einen kleinen Messkopf, der sich einfach integrieren lässt. Die separate Elektronikbox, die im Schaltschrank Platz findet, hat verschiedene Ausgänge, über die der Wert an die Steuerung der Maschine übergeben wird. Auf diese Weise wird die Zwischenlagentemperatur im Betrieb perfekt auf den passenden Wert eingestellt.
Um mit einem Pyrometer die Temperatur genau zu bestimmen, muss der Emissionsgrad exakt bekannt sein. Eine Verfälschung der Messung kann auch auftreten, wenn der Blick auf die Messoberfläche nicht ungestört ist. „Mit unseren arc-Maschinen können wir auch Bauteile aus Titan drucken, wobei allerdings eine starke Schmauch-Entwicklung nicht zu vermeiden ist“, erläutert M. Lange das Problem. In diesem Fall bietet sich der Einsatz von Quotientenpyrometern aus der CTratio-Serie von Optris an. Da hier das Verhältnis der Intensitäten bei zwei Wellenlängen gebildet wird, kann die Messung trotz gestörter Sicht zuverlässig erfolgen. „Deswegen werden wir die Pyrometer der CTratio-Serie in Zukunft vermutlich in Maschinen einsetzen, wenn der Anwender damit Bauteile aus Titan drucken möchte“, so Lange.
Infrarotkameras in der Entwicklung
Bei der Entwicklung der arc-Maschinen und speziell bei der Qualifizierung der Prozesse kommen zusätzlich IR-Kameras zum Einsatz. „Im Rahmen unserer Untersuchungen ist es von Vorteil, wenn man ein Gesamtbild aufnehmen kann und so eine räumliche Verteilung der Temperaturen erhält“ erklärt Martin Wolter, der als Schweißfachingenieur in der Prozessentwicklung bei Gefertec tätig ist. Dadurch lassen sich Temperaturverteilungen und Abkühlprozesse untersuchen, die für die Qualifizierung der Prozesse benötigt werden. Besonders hilfreich ist die Verwendung der Spotfinder-IR-Kamera Xi 400 von Optris (Auflösung 382×288 Pixel). „Da der verwendete Spektralbereich in der aktuellen IR-Kamera für den Einsatz an Metalloberflächen nicht optimal ist, erhalten wir nur eine qualitative Aussage und keine realen Temperaturen“, betont Wolter einen kleinen Nachteil der aktuellen Kamera. Um die tatsächlichen Temperaturen im Schmelzbad und in dessen Umgebung zu bestimmen, wird in Zukunft eventuell mit der PI 1ML eine neue IR-Kamera von Optris eingesetzt, die speziell für Anwendungen mit Metallen konzipiert ist. Sie verwendet eine Messwellenlänge im Bereich von 1µm. In diesem Spektralbereich ist der Emissionsgrad von Metallen deutlich höher als in dem üblichen Spektralbereich zwischen 8 und 14µm. Dadurch sind genauere Temperaturmessungen möglich.
www.optris.de