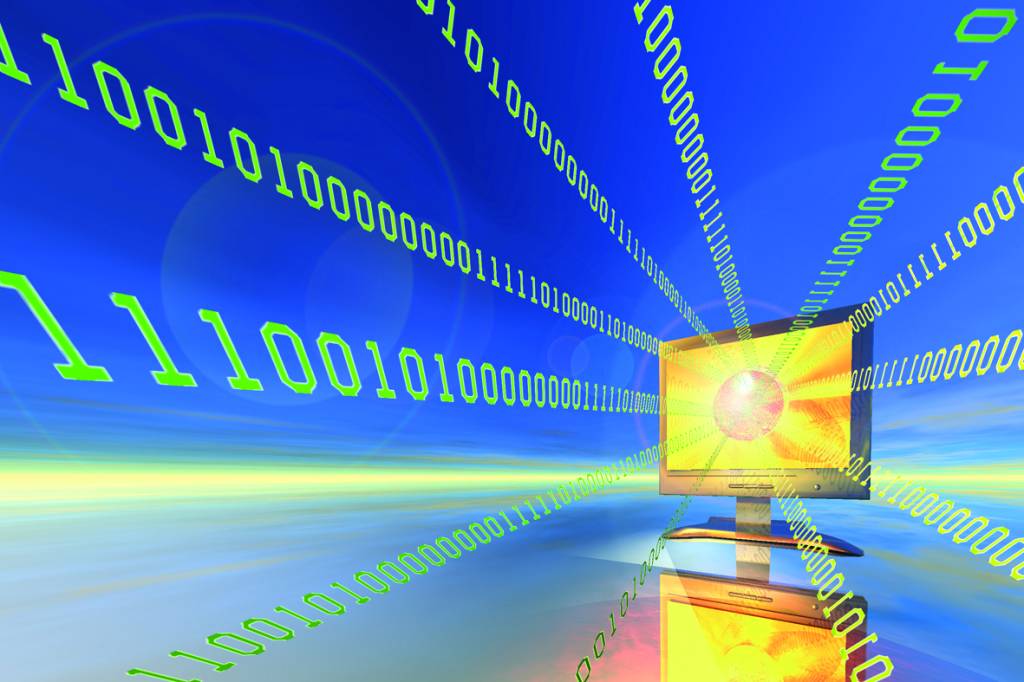
Schon jetzt haben sich für viele Unternehmen die Nachweispflichten mit dem Lieferkettengesetz erhöht. Die Corporate Sustainability Reporting Directive (CSRD) der EU sieht zudem vor, dass ab 2026 auch Mittelständler ab 250 Mitarbeitenden einen Nachhaltigkeitsbericht erstellen müssen. Hinzu kommt in einigen Jahren der geplante Digitale Produktpass. Konkret bedeutet das, für Zertifizierungsprozesse vorbereitet zu sein, die z.B. die Autoindustrie bereits angestoßen hat und in wenigen Jahren von ihren Zulieferern erwartet. Das Nachhaltigkeits-Reporting wird damit zum wettbewerbsentscheidenden Faktor.
Dabei rücken u.a. Kennzahlen zum CO2-Verbrauch und zur Herkunft von Materialien und Rohstoffen in den Vordergrund, ebenso wie Daten aus dem Lebenszyklus des Produkts. Auch die Nachweise zur Nutzung von grünem und blauem Wasserstoff zählen perspektivisch dazu. Um die richtigen Entscheidungen bei Themen wie Wiederverwertung oder Recycling im Sinne der Kreislaufwirtschaft treffen zu können, braucht es bessere Informationen zum jeweiligen Zustand von Anlagen und Komponenten.
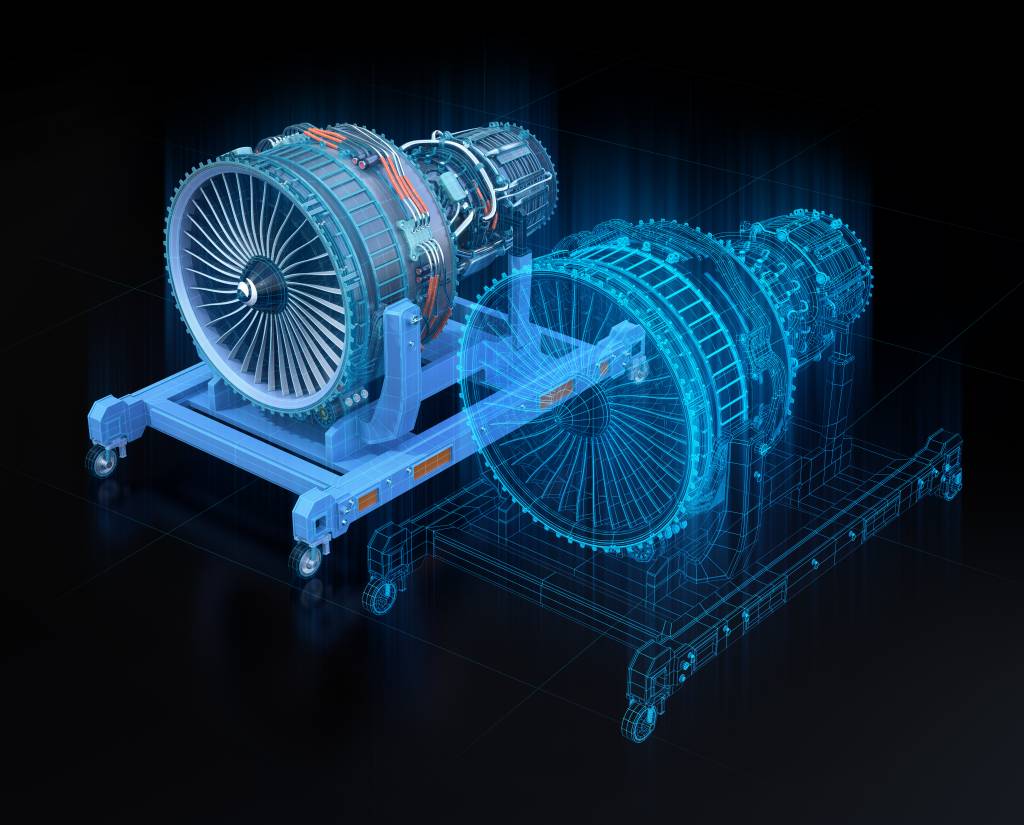
KMU heranführen
Die meisten kleinen und mittelständischen Unternehmen (KMU) sind in der Praxis noch weit von diesen Themen entfernt und durch traditionelle IT-Landschaften mit vielen Datensilos geprägt. Daten werden jedoch künftig gleich für mehrere wichtige Zukunftsthemen zur treibenden Kraft. Dazu gehören auch digitale Geschäftsmodelle und Services, die häufig auf IoT- Sensorikintegration und KI-Analytik basieren. Digitale Service können beispielsweise den Betreibern helfen, Maschinen und Anlagen immer in den jeweils optimalen Leitplanken zu fahren, ihre Rüstprozesse zu optimieren oder mit vorausschauender Wartung für weniger Ausfälle und eine längere Produktlebensdauer zu sorgen. Maschinen- und Anlagenbauer sollten also prinzipiell ihren Fokus von der Entwicklung und Herstellung auf den gesamten Lebenszyklus ihrer Produkte ausdehnen.
Digitalen Zwilling pragmatisch angehen
Im VDMA-Expertenkreis Plattformökonomie zeigte sich in der Diskussion, dass der geplante EU Data Act die Branche maßgeblich betreffen wird, weil sie künftig Daten zu Komponenten und Ausrüstungen in digitaler Form vorhalten muss. Das Datengesetz regelt, wie die in den Wirtschaftssektoren in der EU erzeugten Daten fair genutzt werden können. Der Verband unterstützt Initiativen wie Manufacturing X als selbstbestimmtes Datenökosystem für Industrie 4.0. Die nötigen Daten bereitzustellen und sich an übergreifende Plattformen anzudocken erfordert allerdings ein hohes Maß an Vorbereitung, das sich nicht im Handumdrehen erledigen lässt.
Dabei zeichnet sich schon jetzt ab, dass sich das Konzept des Digitalen Zwillings besonders gut für all diese Herausforderungen eignet. Es kann sowohl für Produkte als auch ihre Herstellungsprozesse und Produktionsumgebungen genutzt werden und schon jetzt haben sich viele Branchengrößen und OEMs dazu bekannt. Obwohl es für die meisten KMU bisher als Buzzword gilt, gibt es pragmatische und bezahlbare Ansätze für die Umsetzung.
Im ersten Schritt geht es darum, die notwendigen Daten zu identifizieren und zu erheben, etwa indem Ausrüstung, Komponenten und Maschinen digitalisiert werden. Dann gilt es, hergestellte und verbaute Objekte mit ihren Eigenschaften in einem Datenmodell zu beschreiben, in das weitere Informationen aus der Nutzungsphase einfließen. Den Input liefern Backend-Systeme wie ERP, PLM/PDM, IoT-Services oder Prozessleitsysteme. Damit Unternehmen schon mit den Vorbereitungen starten können, obwohl es noch keine offiziellen Standards z.B. für den Digitalen Produktpass gibt, sind bereits sogenannte Verwaltungsschalen als herstellerneutraler und branchenübergreifender Standard entwickelt worden. Sie geben Aufschluss über die benötigten Parameter und Eigenschaften.
Zentraler Cloud-Daten-Hub
In der praktischen Umsetzung könnte der Ansatz darin bestehen, eine der großen Cloud-Plattformen als zentrale Datendrehscheibe zu nutzen. Unternehmen müssen sich perspektivisch für einen Technologie-Stack entscheiden. Microsoft beispielsweise bietet mit Azure Digital Twins einen Ansatz, der die Digital Twin Language, das Dataverse für das Handling der Daten und KI-Technologie wie ChatGPT verbindet.