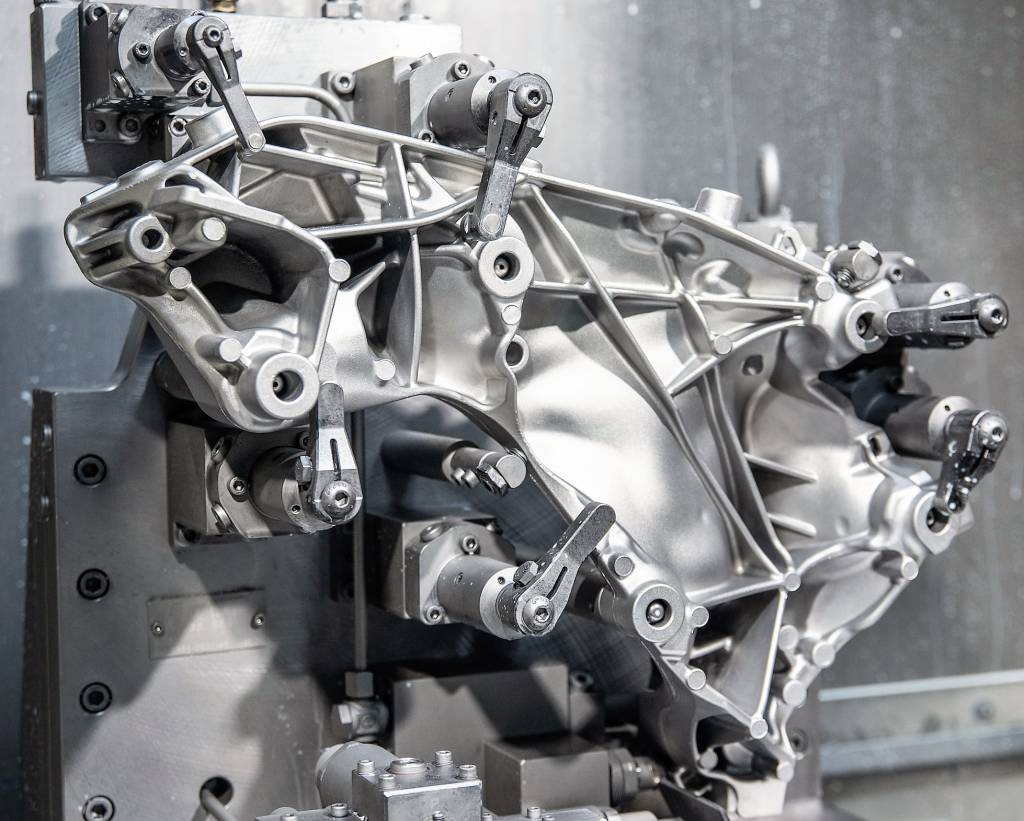
„Durch konsequente Investitionen in erstklassige Maschinen- und Fertigungstechnologie hat sich Fémalk in den letzten Jahren zu einem der gefragtesten Hersteller in der Verarbeitung von Aluminium-Druckgussteilen in Osteuropa entwickelt“, berichtet Samuel Netzer, AMF-Verkaufsingenieur Nord- und Osteuropa. Nicht zuletzt dank moderner Spanntechnik von AMF fertigen die engagierten und qualifizierten Mitarbeiter in den modernen Werken Gussteile zwischen 30 und 5.500g. Man mag es dem Firmensprecher gerne glauben, wenn er sagt „in beinahe jedem Pkw in Europa steckt mindestens ein Teil von uns.“
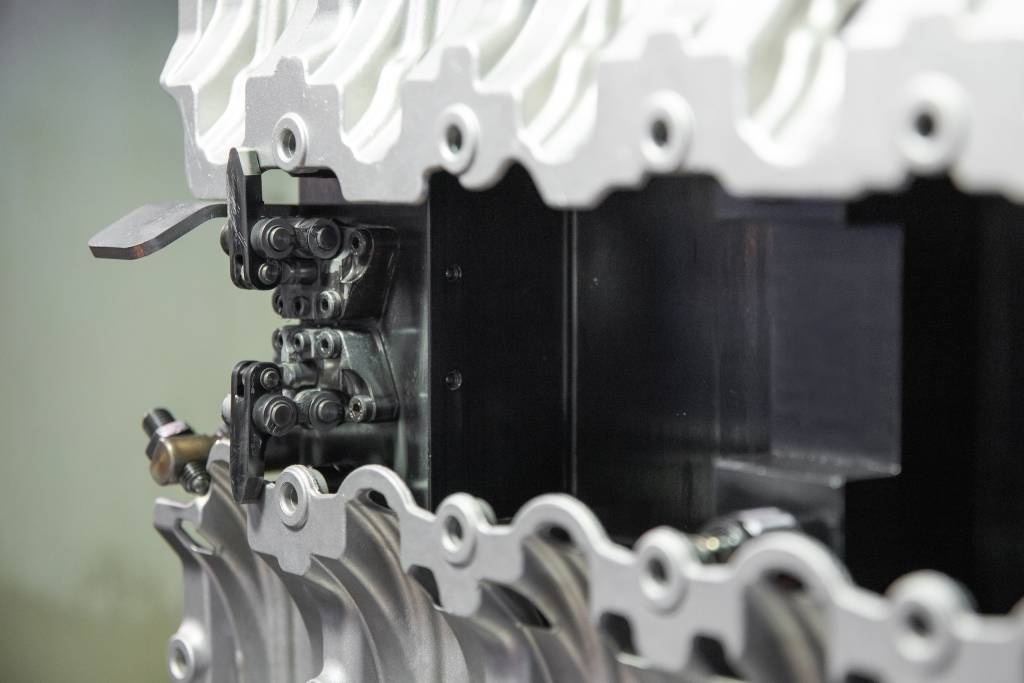
Taktzeiten nur mit moderner Spanntechnik erreichbar
Um dies zu erreichen, investierte Fémalk nicht nur in Gebäude, Maschinen und Arbeitskräfte, sondern auch in hocheffiziente Spanntechnik. Was mit Pilotprojekten und einfachen hydraulischen Spannelementen von AMF begann, ist im Laufe der letzten Jahre zu einer wirkungsstarken Spanntechnik mit Automation und Nullpunkt-Spannsystemen ausgebaut worden. Infolgedessen verkürzten sich die Rüstzeiten dermaßen deutlich, dass die Maschinenauslastung extrem anstieg. Das ist vor allem einem cleveren Mitarbeiter im Hause zu verdanken: Gábor Soós, verantwortlich für den Vorrichtungsbau, hat hier immer weitergedacht und gemeinsam mit den Vertretern von AMF stets nach Optimierungspotenzial gesucht. Inzwischen ist die Spanntechnik so flexibel und teils automatisiert, dass die Maschinen für kleine Stückzahlen (beispielsweise für einen Bentley) genauso effizient gerüstet werden können, wie für Großserien von VW.
Dazu bestückte das Unternehmen 15 Bearbeitungszentren mit moderner AMF-Nullpunkt-Spanntechnik. Was im Jahr 2015 mit einem einfachen Winkelspanner startete, ist inzwischen auf rund 200 Vorrichtungen gewachsen, die mit Bolzen für die Nullpunktschnittstelle ausgestattet sind. Die eigens entwickelten Vorrichtungen enthalten zunächst für jede Maschine eine Grundplatte mit Spannbolzen, die von den Nullpunktspannmodulen aufgenommen werden. Die AMF-Berater halfen dabei mit vielen Tipps und einem umfassenden Teilesortiment effizient weiter. Im Einsatz befinden sich z.B. Schwenkspanner, Spannarme, Schließventile und Druckspeicher genauso wie Schnellkupplungen, Manometer, Vertikalspanner oder Abstützelemente. „Dass ein einziger Anbieter so viele Teile in seinem Sortiment führt, hat uns natürlich sehr geholfen und die Beschaffung stark vereinfacht“, betont Gábor Soós.
Auf den Grundplatten sorgen vier Varianten an Vorrichtungen mit Druckregelventilen und mehreren Mediendurchführungen für eine besonders hohe Flexibilität. „So können z.B. alle Verbraucherkreise mit unterschiedlichem Druck angesteuert werden und – das kommt als Extra hinzu – sie können auch zeitverzögert angesteuert werden“, betont Netzer. Mit dieser Lösung können für die Aufnahme eines Werkstücks zunächst die Abstützelemente ausgefahren und erst danach die Spannvorrichtungen geschlossen werden.
Hauptzeitparallel rüsten
Die Grundplatten sind mit jeweils vier Nullpunktspannmodulen K10 bestückt. Mit je 10kN ziehen sie die Spannbolzen der Grundplatten zuverlässig mit 5µm Wiederholgenauigkeit ein, verschließen sie sicher und halten sie mit hohen 25kN Haltekraft fest. Das Öffnen der Module geschieht hydraulisch mit einem Betriebsdruck zwischen 50 und 60bar. Weil sie nach dem Spannen durch Federkraft mechanisch verriegelt werden, lassen sich die Druckleitungen anschließend jederzeit abkoppeln.
Beladen werden die Vorrichtungen außerhalb der Maschine. So lässt sich hauptzeitparallel außerhalb des Maschinenraums die nächste Bearbeitung optimal vorbereiten. Die Bauteile werden dann in gespanntem Zustand in die Maschine übergeben. Nur so gelingt es, Rüstzeiten dermaßen kurz zu halten, dass sich die Teile, welche die 42 Druckgießmaschinen überwiegend vollautomatisch gießen, auch ohne große Zeitverzögerung weiterbearbeiten lassen. Die Serienproduktion bewältigt dabei Stückzahlen zwischen zehn und 15.000 Stück pro Woche – sowohl kleine als auch große Serien.
Weltweit zu vielen OEMs
Unglaubliche 4.000 Tonnen Aluminium verarbeiten die Ungarn jeden Monat zu Druckgussteilen. Durch Weiterbearbeitung entstehen daraus Fahrwerksteile, Motor- und Getriebelager sowie Elektronikgehäuse, aber auch komplexe Klimakompressorteile, Scheinwerfer- oder Thermostatgehäuse. Die liefert das Unternehmen in verschiedene Werke von OEMs weltweit. Dazu gehören BMW, Bentley und Porsche, aber auch VW, BASF oder Boge. Meist rangiert Fémalk als Tier-1-Zulieferer.