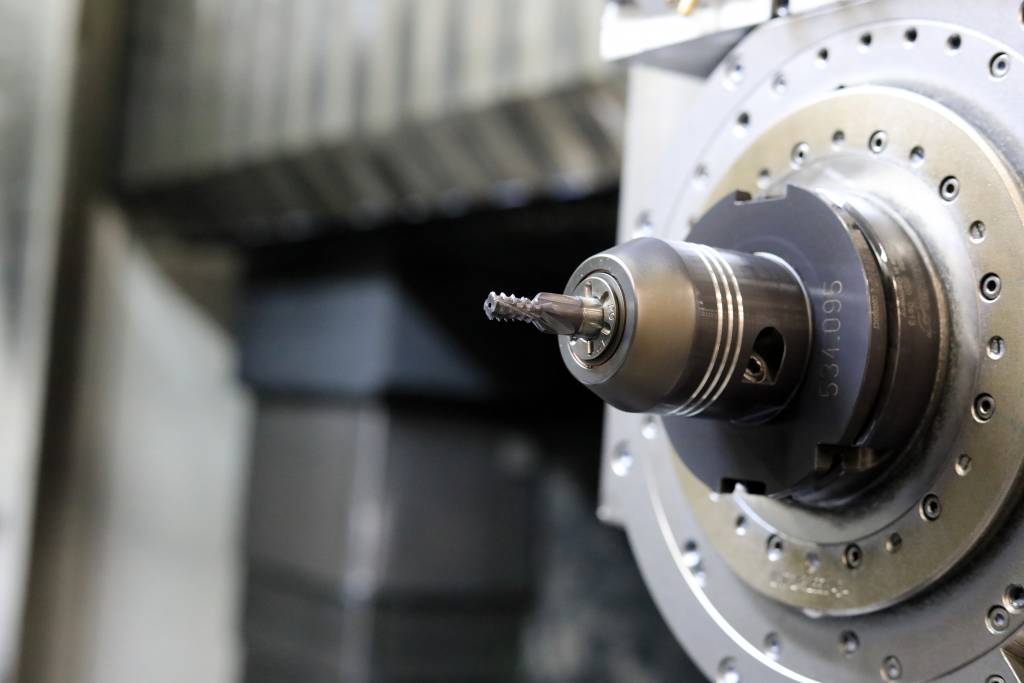
Für ein in Sachen Prozesssicherheit besonders herausforderndes Projekt sprach Florian Zobel, bei Berger als Meister verantwortlich für die Produktlinie Großteile, mit Michael Dreher, Technischer Berater bei Walter. Der Lösungsansatz, den die Walter Experten für sein komplexes Gewindefräs-Projekt vorschlugen, hat ihn zuerst überrascht – und dann überzeugt: Mit dem neuen Gewindefräser TC620 lassen sich die geforderten Gewinde nicht nur deutlich schneller fertigen als mit den von anderen Anbietern empfohlenen Werkzeugen. Der Prozess ist trotz der hohen Belastungen auf dem Werkzeug extrem stabil – und das bei einer sehr langen Werkzeugstandzeit.
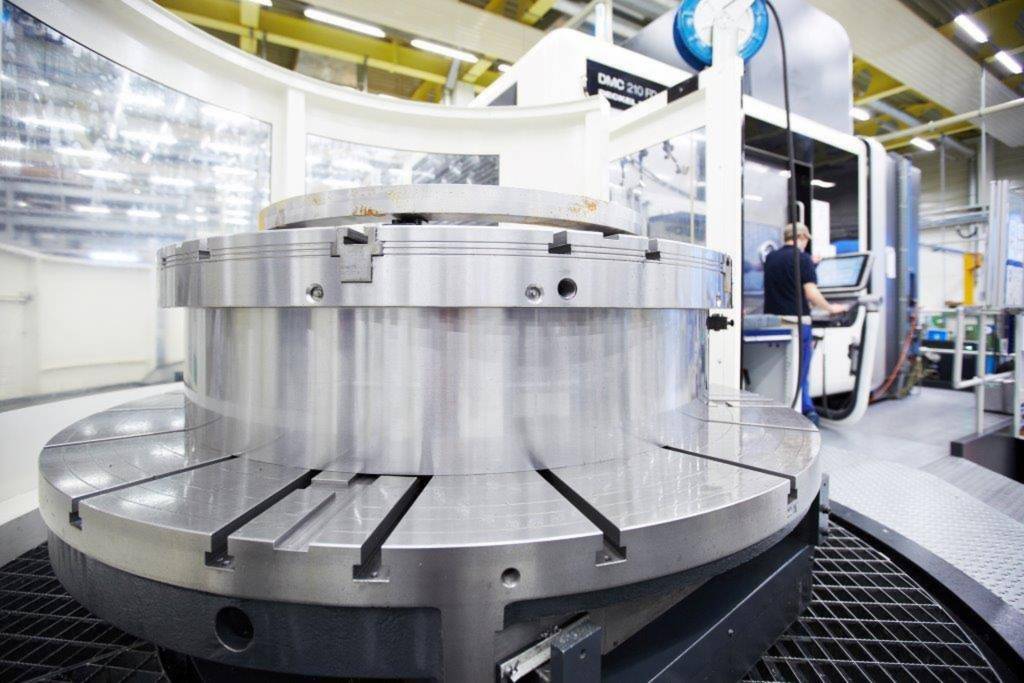
Großes Bauteil, viele kleine Gewinde
Mit Durchmessern zwischen 1,50 und 2,40m sind die Ringe aus C45-Stahl, die bei Berger im Auftrag eines großen Maschinenbauers bearbeitet werden, schon allein aufgrund ihrer Dimensionen eine Herausforderung. Geht bei der Bearbeitung etwas schief, wird die Nachbearbeitung extrem aufwendig – und damit teuer. Und das Risiko eines Werkzeugbruchs ist gerade bei diesem Projekt besonders hoch: In ein Bauteil müssen jeweils bis zu 269 Gewinde (M10 oder M8) eingebracht werden. Prozesssicherheit ist deswegen für Meister Florian Zobel entscheidend: „Einen abgebrochenen Gewindebohrer müssten wir aus dem Bauteil herauserodieren. Das heißt: Dieses Riesending muss runter von der Maschine, raus aus der Halle und zum innerbetrieblichen Dienstleister. Ein Aufwand, den wir unbedingt vermeiden wollen.“
Auch wenn Prozesssicherheit oberste Priorität hat: Für die Wirtschaftlichkeit spielen Bearbeitungszeit und Werkzeugstandzeit die ausschlaggebende Rolle. Die Herausforderung lag darin, hier das Beste aus der Bearbeitungsmaschine herauszuholen. Für das anfangs geplante Fertigungsverfahren – das klassische Bohren der Gewinde – fehlt der bei Berger eingesetzten Maschine die notwendige Dynamik, um auf den Wechsel von Abbremsen und Beschleunigen bei kurzen Gewinden zu reagieren. Florian Zobel, NC-Programmierer Jürgen Swoboda und Zerspanungsmechaniker Tobias Gschwend entschieden sich für das Gewindefräsen als die prozesssichere Alternative. Das Berger Team testete Gewindefräser von vielen namhaften Herstellern, aber wirklich überzeugen konnte keiner: Vor allem die Standmengen schwankten erheblich, mit entsprechenden Auswirkungen auf Bearbeitungszeit und Gewindequalität.
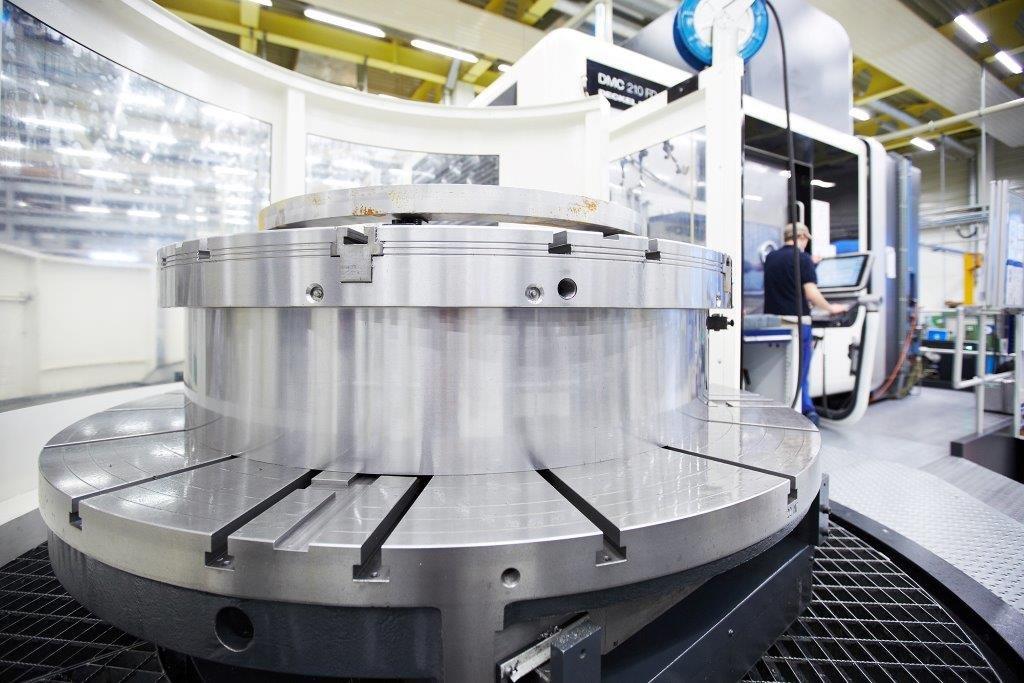
Innovative Fräsergeometrie überzeugt
Als Alternative schlugen Michael Dreher von Walter und sein Kollege, der Anwendungstechniker Marco Herdlitschka, vor, den bis dahin ausschließlich im Walter Testbetrieb gelaufenen Gewindefräser TC620 auszuprobieren. Mit diesem Vollhartmetallfräser haben die Walter Entwicklungsingenieure das grundlegende Problem des Gewindefräsens auf überraschende Art gelöst. Die Zähnezahl wurde reduziert und in einem mehrreihigen Design optimiert.
Der beschränkende Faktor beim Gewindefräsen ist fast immer der Schnittdruck und damit die Abdrängung des Fräsers aus der gewünschten Bahn. Das wirkt sich negativ auf die Standzeiten und auf die Bearbeitungszeit aus. Üblicherweise versucht man, durch mehr Zähne, ungleiche Drallwinkel und Veränderung der Beschichtung diese beiden Parameter zu verbessern. Mit der neuen, mehrreihigen Fräsergeometrie verringert Walter die Zahl der Zähne deutlich – und damit auch den Schnittdruck. Der Effekt: Mit dem TC620 lässt sich ein deutlich höherer Vorschub pro Zahn fahren als mit konventionellen Lösungen.
Problem rasch gelöst
Nach dem ersten Testlauf waren Zobel und sein Team begeistert: „Das Werkzeug sieht nicht aus wie die Fräser, die man so kennt. Wir haben mit niedrigen Schnittdaten angefangen, der Walter TC620 Supreme war trotzdem schneller als alles, was wir vorher versucht hatten. Und die Standzeiten waren genauso herausragend.“ Nach einigen Testläufen stand dann die optimale Frässtrategie. Insgesamt vergingen von den ersten Gesprächen bis zum fertigen Prozess ungefähr zwölf Wochen.