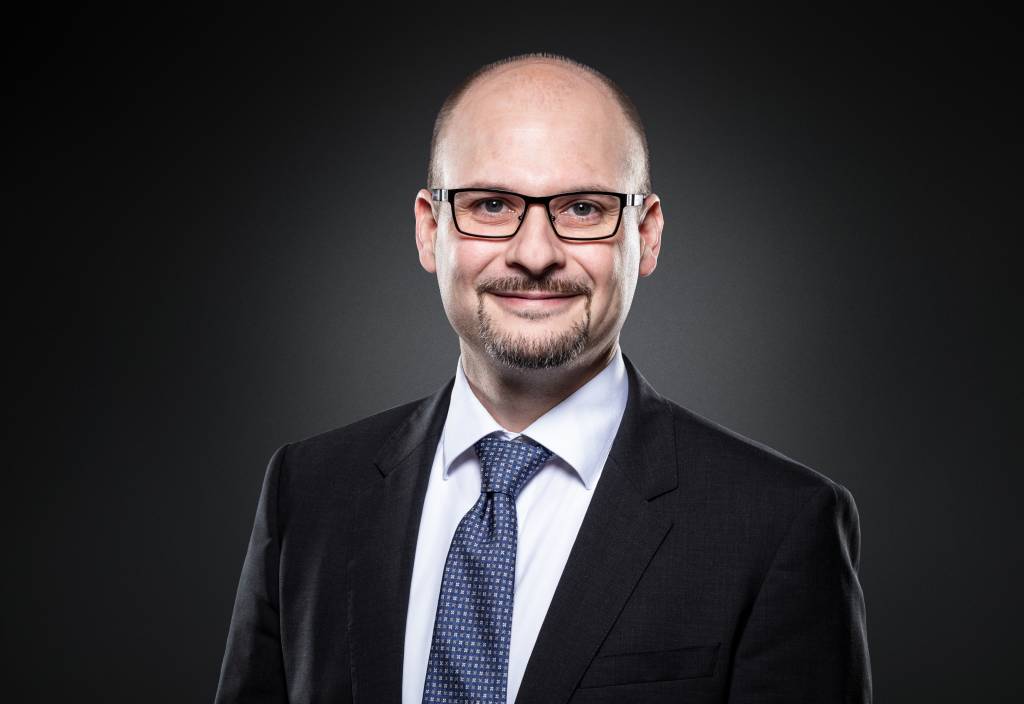
Sowohl Spezialisten von Präzisionswerkzeugen als auch Hersteller von Schleifmaschinen und Bearbeitungszentren kennen sich bei der Optimierung von Prozessen oft bestens aus. Es geht darum, kundenspezifisch den produktivsten sowie wirtschaftlichsten – und immer mehr auch den nachhaltigsten Prozess – zu finden. Fachleute aus Industrie und Wissenschaft zeigen auf, mit welchen Fertigungstechnologien Anwender selbst komplexe Bauteile komplett und somit nachhaltiger herstellen.

Komplettbearbeitung mit Präzisionswerkzeugen
„Mit über 25.000 Standardwerkzeugen und mehr als 150.000 kundenspezifischen Sonderlösungen hat sich Paul Horn aus Tübingen breit aufgestellt und zeigt zahlreiche Neuheiten, Lösungen, Anwendungen und Prozesse auf der EMO 2023 in Hannover“, kündigt Geschäftsführer Markus Horn an (www.horn-group.com – Halle 5, Stand A54). „Das Thema Komplettbearbeitung lässt sich damit ideal abdecken, wie folgende Praxisbeispiele zeigen.“
Zur Fertigung eines Zeckensticks auf einem Langdrehautomaten kamen unterschiedliche Horn-Werkzeuge zum Einsatz. Der erste Bearbeitungsschritt ist das Drehen des Außendurchmessers. Danach folgt das Fräsen der Kontur für die Klinge. Dabei fertigt das Werkzeug im Vollschnitt die obere Kontur sowie die untere Anspiegelung der Klinge. Zur Aufnahme der Zecke wird mit einem 3-mm-Vollradiusfräser eine Absetzung an der Klinge gefräst. Anschließend erfolgt das Fräsen der Klinge. Zum Verschrauben mit einer Hülse wird im nächsten Bearbeitungsschritt ein Außengewinde der Größe M7 x 0,5 gefertigt. Nach dem Gewinde erfolgt das Kopieren der restlichen Kontur. Anschließend fräst eine weitere Zirkularfräsplatte zwei gegenüberliegende Flächen an den Außendurchmesser. Die Flächen dienen zum einen als Griffe und zum anderen als Beschriftungsflächen. Der finale Arbeitsschritt ist der Abstich des Bauteils. Alle Fertigungsschritte erfolgen vollständig auf nur einer Maschine.
„Ein weiteres Beispiel ist die Komplettbearbeitung einer Düse. Diese besteht aus rostfreiem Stahl 1.4301“, führt Markus Horn weiter aus. „Das Bauteil beinhaltet mehrere Zerspanoperationen, die mit unterschiedlichen Horn-Werkzeugsystemen ausgeführt werden.“ Als Schmierstoff dient hierzu die Minimalmengenschmierung (MMS). Beim Längsdrehen der Düse geschieht die Schmierung über die Kühlmittelbohrungen am Werkzeughalter, ebenso wie bei der Herstellung des Außengewindes. Das Innenausdrehen der Düse wird mit einem Werkzeug aus dem Horn-Programm vorgenommen, das über eine Kühlmittelbohrung direkt in der Platte verfügt. Daher erfolgt die Schmierung durch die Platte gezielt an die Schneide bzw. in die Zerspanzone. „Bei den eingesetzten Werkzeugen handelt es sich ausschließlich um Standardwerkzeuge, die nachhaltig über MMS geschmiert werden“, betont der Geschäftsführer. „Alle Lösungen sind grundsätzlich auch auf MMS ausgelegt und benötigen daher keine weitere Anpassung.“

„Schlüsselfertig Schleifen reicht längst nicht mehr“
Die Komplettbearbeitung komplexer Werkstücke in einer Aufspannung ist mittlerweile zum Standard geworden. Dass die Anforderungen im Schleifen immer weiter steigen, zeigen die Entwicklungen der vergangenen Jahre deutlich. „Dies betrifft aber nicht einfach nur das Schleifen, sondern vor allem die vor- und nachgelagerten Prozesse der Herstellung“, sagt Heiko Zimmermann, Head of Sales Europe bei Adelbert Haas in Trossingen (www.multigrind.com – Halle 6, Stand E24). „Der Schlüssel zum Erfolg ist hier definitiv die Software.“ Dass die Software das zentrale Elemente ist und die Hersteller von komplexen Werkstücken einen entscheidenden Schritt weiterbringt, demonstrieren die Präzisionsspezialisten aus dem Schwarzwald seit Jahren eindrucksvoll: beispielsweise mit digitalem Vorschleifen sowie sichtbarem Bearbeitungsabsatz und mit allen Werkstückdetails, von Unebenheiten in den Übergaben und Restwelligkeiten in den Oberflächen bis hin zu genauesten Anpassungen und Korrekturen sowie von der Maschine entkoppelter Prozessoptimierung. „Infolgedessen lassen sich konkret Rohlinge und Schleifmittel einsparen und Prozesszeiten erheblich verkürzen“, erläutert Zimmermann. „Damit basieren wettbewerbsfähige Taktzeiten nicht mehr ausschließlich auf Schleif-know-how und physischen Testbearbeitungen, sondern lassen sich bereits im Vorfeld ohne Aufwendungen von Maschinenstunden und Ressourcen erarbeiten. Das und vieles mehr zeigen wir auf der EMO Hannover 2023.“
Weil Materialien, Energie und Ressourcen noch effizienter eingesetzt werden müssen, leistet die Steuerung der Fertigung einen weiteren wesentlichen Beitrag. Im Fokus befindet sich dabei die Abbild- und Steuerbarkeit des gesamten Fertigungsprozesses. Alle Prozesskomponenten – wie manuelles Scannen, Automationslösung, Reinigungsanlage oder Beschriftungsmaschine usw. – können digital beliebig aus- und eingebaut werden. So wird maximale Transparenz in der Auftragsplanung geschaffen, trotz unterschiedlicher Aufträge, Prioritäten und Stationsbelegungen. Die Modifikation von Aufträgen kann während der Fertigung erfolgen. Das spart wertvolle Zeit und geht mit geringeren Stillstandzeiten einher. Parallel zum gefertigten Auftrag lässt sich bereits rüsten und somit Downtime sparen.
In Prozessen denken – mit Closed Loop automatisieren
„Die Index-Werke aus Esslingen sind bekannt für leistungsfähige Werkzeugmaschinen zum Drehen und Fräsen“, erläutert der Leiter Global Marketing Rainer Gondek, „immer mehr aber auch für unsere Automationslösungen“ (www.index-werke.de – Halle 17, Stand D03). Letztere eignen sich nicht nur zum Be- und Entladen der Maschinen, sondern bereiten außerdem den Weg zu einer automatisierten Prozessführung. Mit dem Closed Loop ist ein geschlossener Regelkreis gemeint. Dieser enthält in der von Index angebotenen Form die Elemente Produzieren, Handhaben, Messen / Prüfen und Kompensieren. Ein Beispiel: Der Anwender fertigt eine Bauteilserie auf einem Produktionsdrehautomaten der Süddeutschen. In der angeschlossenen Index Roboterzelle erfolgt das Teilehandling: Ein Roboter legt das Rohteil aus der Palette in die Maschine ein, entnimmt es nach der Bearbeitung, gibt es an das in der Roboterzelle installierte Prüf-/Messystem weiter und legt anschließend das gemessene Teil wieder in der Palette ab.