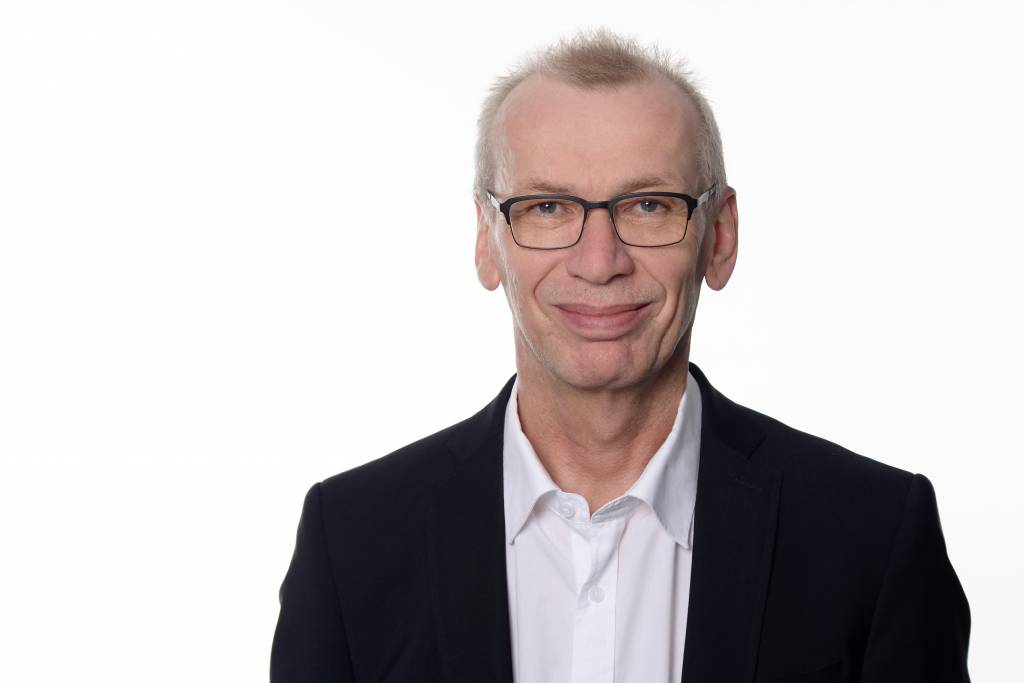
Wenn es Unternehmen schwerfällt Lieferfristen zu halten, Aufträge flexibel umzuplanen und Fragen nach dem Fertigungsstatus zu beantworten, könnte es daran liegen, dass das eingesetzte Manufacturing Execution System nicht mehr das aktuellste ist. Hinweise darauf, ob die Werks-IT heutigen Anforderungen noch genügt, liefern die folgenden Faktoren.
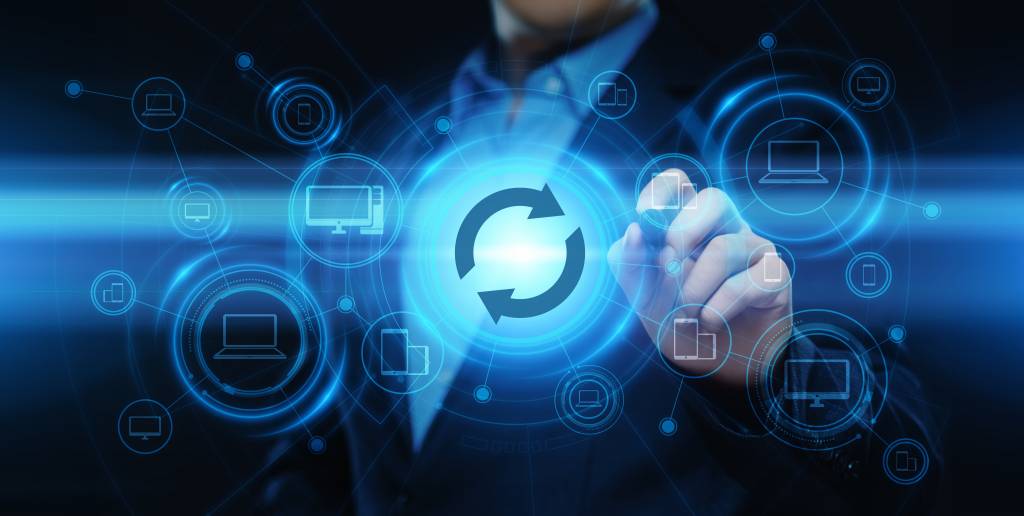
Mangelnde ERP-Integration
Oft stimmen die Daten im MES nicht mit der Auftragsstruktur aus dem ERP-System überein, weil die Schnittstelle zwischen beiden Programmen nicht detailliert genug ist. Manchmal sind Vorgänge auf der Fertigungsschicht viel granularer, als dies im ERP-System verzeichnet ist. Das führt beispielsweise zu Problemen, wenn Nacharbeitsschleifen in der Business Software nicht vermerkt werden können. Ein Mitarbeiter müsste dann den jeweiligen Auftrag manuell in das ERP-System eintragen, was mit Zeitaufwand verbunden ist. Wird die Nacharbeit nicht erfasst, unterscheiden sich die Abläufe im ERP-System von den tatsächlichen Tätigkeiten im Shopfloor. Neuere ME-Systeme bieten die Möglichkeit, die Daten genauer zu erfassen, den Mitarbeiter feingranularer anzuleiten und die Daten auch im führenden System aktuell zu halten.
Fehlende Flexibilität
In der Produktion ist vieles unvorhersehbar, z.B. müssen Mitarbeiter Fertigungsaufträge oft vorziehen oder nach hinten schieben. Solche Umplanungen sollten grundsätzlich im ERP-Programm vorgenommen und dann im MES aktualisiert werden. Im Alltag wird dies oftmals umgangen, wenn die Systeme nicht flexibel genug sind. Wird die Umplanung nicht aus dem ERP-System angestoßen und werden die Daten nicht häufig genug abgeglichen, stimmen die Systemdaten nicht mehr überein: Laut dem ERP-System wird die ursprüngliche Planung beibehalten, obwohl auf dem Shopfloor gerade etwas ganz Anderes passiert.
Keine vorausschauende Planung
Viele aktuellere ME-Systeme sammeln die relevanten Daten aus den mit der Produktion verbundenen Prozessen und stellen diese für Analysen und Auswertungen zur Verfügung. Das ermöglicht Transparenz über die beteiligten IT-Systeme, um Möglichkeiten für Effizienzsteigerungen aufzuzeigen. Auch dabei spielt die Integration von ERP-System und MES eine zentrale Rolle, denn beide müssen (fast) in Echtzeit miteinander kommunizieren. Im Falle vorausschauender Wartung (Predictive Maintenance) müssen beispielsweise Informationen aus dem MES automatisch im ERP-System die Anlage eines Instandhaltungsauftrags anstoßen, der dann wiederum in der Planung die Kapazitäten auf der Anlage reduziert.