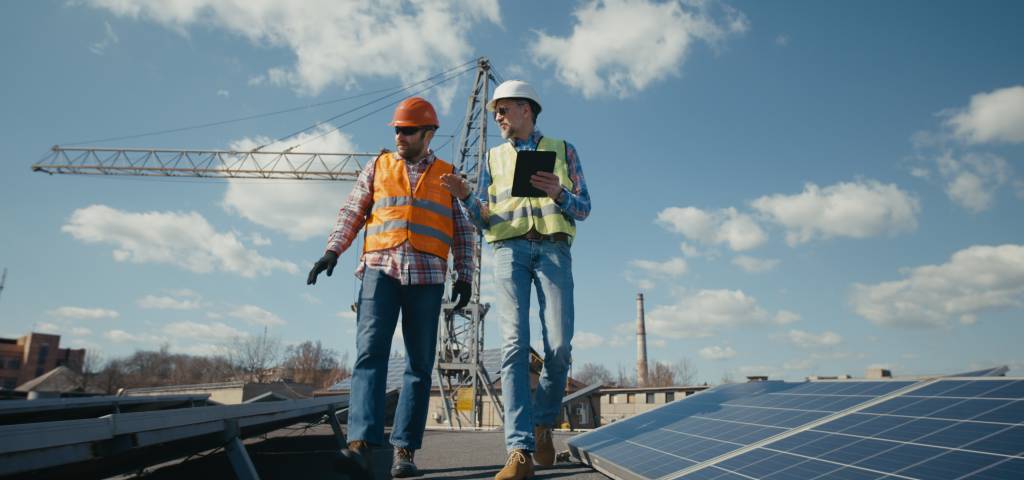
Viele Unternehmen befassen sich gerade mit den Möglichkeiten, ihren CO2-Ausstoß entlang der Wertschöpfungskette zu dokumentieren und zu reduzieren. Gleichzeitig wollen Firmen Innovationszyklen beschleunigen und für Fachkräfte attraktiv bleiben. Der ursprüngliche Begriff der ökologischen Nachhaltigkeit, Sustainability, wird daher zunehmend auf umfassendere Begriffe wie Business Sustainability erweitert, oder mit Begriffen wie Manufacturing Sustainability spezialisiert. Doch welche Konzepte und welche unternehmerischen Maßnahmen stehen hinter diesen Begriffen? Und wie lassen sich die Konzepte umsetzen und mit welchen Tools und Methoden unterstützen?
Startpunkt Daten
„Wir haben heute eine zunehmende internationale Vernetzung, neue Arbeitsmodelle wie Remote Work, eine steigende Relevanz von Nachhaltigkeitsaspekten, aber auch veränderte, individuelle Kundenbedürfnisse“, sagt Björn Manderbach, Director Delmia Industry Consulting bei Dassault Systèmes. „Um einerseits Resilienz, andererseits Agilität und nachhaltig Geschäftskontinuität sicherzustellen, wollen viele Unternehmen, auch Mittelständler aus der Fertigungsbranche, die Digitalisierung jetzt verstärkt anpacken.“ Kernelement ist dabei, über alle Produktionsdaten Bescheid zu wissen und Werte über entstehende CO2-Emmisionen mit einfließen zu lassen. Das wird nicht ganz einfach, ist die Lage bei unterschiedlichen Produktarten doch sehr verschieden. Während beispielsweise der CO2-Fußabdruck eines Laptops vorwiegend in seiner Herstellung entsteht – rund 80 Prozent des Ressourcenaufwandes fallen im Produktionsprozess an, nur 20 Prozent während der Nutzungsphase, ist das Verhältnis bei Komponenten der Automatisierungstechnik oder gar großen Antriebssystemen genau andersherum. Dennoch ist der Einfluss des Fertigungsprozesses auch bei diesen Produkten sehr groß. Um Hersteller in die Lage zu versetzen, möglichst umweltverträgliche, aber dennoch profitable Produkte zu entwickeln, habe Dassault Systèmes das 3DExperience Universe geschaffen, sagt Manderbach: „Wir sehen das Ganze also ein bisschen breiter. Unsere Marke Delmia hat einen Fokus auf die Themen Produktion, Logistik-Prozesse und Global Operations, wie wir es nennen. Die Digitalisierung in diesen Bereichen bietet schon einen großen Hebel für die Erreichung einer nachhaltigen Fertigung.“
Nachhaltigkeit ermöglichen
Für eine nachhaltige Produktentwicklung reicht es nicht, mit einem fertigen Produkt zu kommen und dann zu überlegen, wie sich dieses nachhaltig fertigen lässt. Man müsse viel weiter vorne beginnen. „Das beginnt mit den Requirements, mit den Anforderungen an das Produkt in der späteren Nutzung“, führt Björn Manderbach aus. „Hier gilt es z.B. bereits zu überlegen, welche Materialien verwendet werden und welche Auswirkung diese auf Qualität und Lebensdauer haben, aber auch, welche Auswirkungen sie auf CO2-Ausstoß und Fertigungsmethoden haben.“ Die 3DExperience-Plattform bietet daher die Möglichkeit, verschiedene Beteiligte am Entwicklungs- und Produktionsprozess zusammenzuführen. Die Fragen gehen tief: Welchen Einfluss haben Geometrie, Material und Konstruktion eines Produktes auf Qualität, Nachhaltigkeit, Fertigungsverfahren und Kosten des Endprodukts? Wie sieht es mit Service und Wartung aus? Wie mit der Recyclingfähigkeit? Ein gemeinsames Datenmodell, etwa auf der 3DExperience-Plattform, hilft, diese Anforderungen aus unterschiedlichen Blickwinkeln zu beleuchten, weil auch unterschiedliche Personen aus unterschiedlichen Bereichen oder sogar Firmen am Projekt arbeiten können. „Wenn wir die Rückkopplungsschleifen zwischen beteiligen Abteilungen und Zulieferern eng halten, profitieren alle“, schildert Manderbach.
Ideen virtuell validieren
Werden vernetzte digitale Modelle und virtuelle Zwillinge konsequent ausgerollt, können die Nutzenaspekte deutlich weiter als nur in die Produktentwicklung reichen. „Digitale Modelle sind eine Spielwiese“, sagt Manderbach. „Ich kann meine Gedanken fliegen lassen. Im virtuellen Bereich habe ich die Freiheit, mir andere Abläufe zu überlegen. Ich habe die Freiheit, andere Betriebsmittel einzusetzen und dann zu sehen, welche Auswirkungen das für den Prozess hat. Ich kann sogar die Bebauung mit einbeziehen, die Geometrie der Werkhalle. Ich kann ganze Maschinen neu anordnen, den Platzbedarf testen und vielleicht die Produktion erweitern, ohne eine neue Halle bauen zu müssen. Auch das wirkt sich ja auf den Ressourcenbedarf und damit den CO2-Fußabdruck aus.“ Nach Tests und Abstimmungen mit den Abteilungen kann diese digitale Produktion in die Realität umgesetzt werden, nicht nur physisch, auch bezüglich der Prozesse und Arbeitsanweisungen für die Werker. Doch damit endet die Digitalisierung nicht. Denn die Informationen aus der realen Produktion können auch wieder zurückgespielt werden in den digitalen Zwilling. Abweichungen können auf beiden Seiten korrigiert werden: Entweder in der realen Produktion, oder aber im virtuellen Modell.