Die 1954 gegründete Firma August Wenzler Maschinenbau in Spaichingen kommt aus dem Sondermaschinenbau. Als die Heller Group 2009 den Betrieb übernahm, wechselte das Portfolio hin zum Standardhersteller von 5-Achs-Bearbeitungszentren. Das BAZ vom Typ VKM weist dabei die Besonderheit auf, dass bis zu zwei Zentren in einem Grundbett integrierbar sind. In Verbindung mit hoher Agilität und der Verwendung von Minimalmengenschmierung (MMS) ist diese Maschine ideal geeignet zur Zerspanung von Aluminiumstrukturbauteilen.

Wenig Masse, hohes Tempo
Andere Maschinen dieser Größe sind meist auf ein hohes Zerspanvolumen ausgelegt; das macht sie entsprechend schwer und langsam. Wenzler ging einen anderen Weg und konstruierte eine hochagile Maschine mit geringen Massen. Ein typisch geeignetes Bauteil für die Maschine ist ein Fahrschemel, der in Fahrzeugen als Hinterachsträger fungiert. Er misst bis zu 1.000×1.000mm bei einem Gewicht zwischen 25 und 30kg. Damit bietet sich eine automatische Be- und Entladung der Maschine an.
Wenn es mal sehr schnell gehen muss, fallen Wenzler auch ungewöhnliche Lösungen ein: beispielsweise als ein Sportwagenhersteller, der nicht über eine eigene Teilefertigung verfügt, dringend 3.000 Fahrschemel benötigte. Der Maschinenhersteller wurde kurzerhand zum Lohnfertiger und half dem Kunden aus der Bredouille. Die Bauteilequalität und das Prozessverständnis der Süddeutschen überzeugten den Autohersteller. Vier Jahre später wandte er sich erneut an Wenzler zur Fertigung von Fahrschemeln. In diesem Fall wollte das Unternehmen eine Maschine mitsamt einem auf MMS ausgelegten Prozess kaufen. Damit startete der Sportwagenhersteller keine eigene Teilefertigung, sondern stattete seinen Zulieferer (eine Gießerei) aus – der aus eigener Kraft allerdings nicht auf die erforderliche Taktzeit für das Bauteil kam.
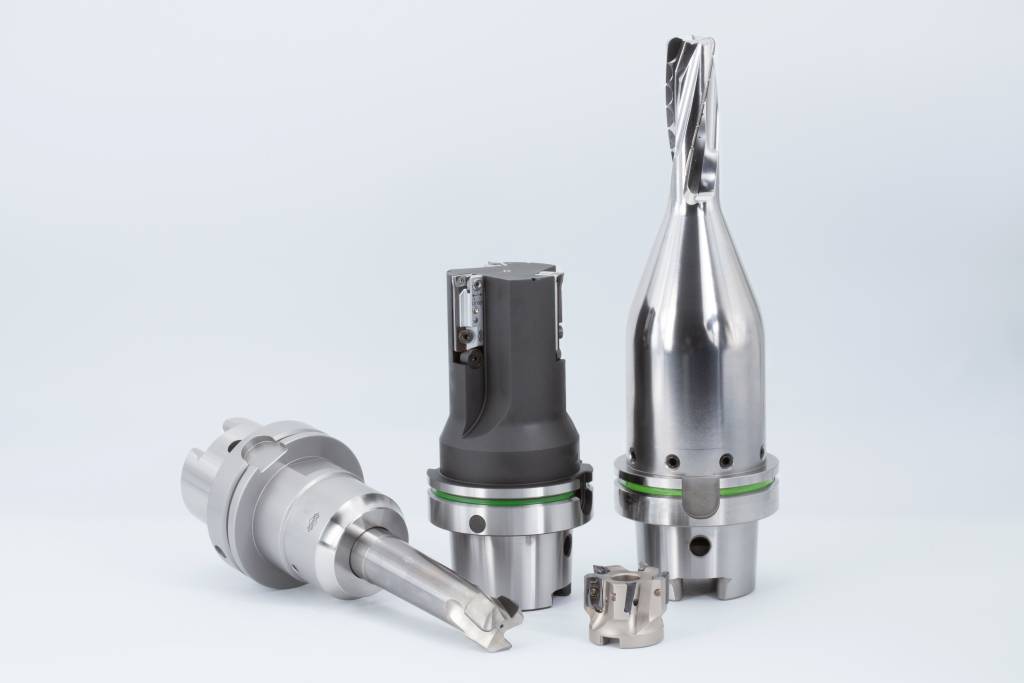
Nur zehn Wochen Zeit
Die Gießerei benötigte anfangs rund vier Stunden für die mechanische Bearbeitung des Achsträgers in mehreren Aufspannungen und kam auch nach verschiedenen Optimierungen nicht unter zwei Stunden. Mit diesem Output wäre das Produktionsziel von jährlich 4.000 Exemplaren der Sportwagen in Gefahr gewesen. Anhand der Daten analysierte Wolfgang Wenzler, der das Familienunternehmen zusammen mit seiner Schwester Ingrid Wenzler in dritter Generation leitet, das Bauteil – und er kam zu dem Ergebnis, dass eine Taktzeit von 16 Minuten möglich ist. Das konnte nach seiner Einschätzung aber nur gelingen, wenn er Mapal aus Aalen als Werkzeuglieferant mit ins Boot holen könnte. Die beiden Unternehmen arbeiten seit mehr als 40 Jahren zusammen und haben schon viele Projekte erfolgreich umgesetzt. Die Herausforderung bestand dieses Mal in dem enorm hohen Zeitdruck für das Projekt, das innerhalb von zehn Wochen komplett abgeschlossen sein sollte. Eine ’normale‘ Laufzeit für solche Projekte beträgt zehn Monate.
Wolfgang Wenzler würdigt die Zusammenarbeit mit Mapal: „Der gute Durchgriff in diesem Unternehmen ist imposant. Wir landen hier sehr schnell bei den richtigen Leuten bis hinauf in die Geschäftsleitung, wenn es um entsprechende Entscheidungen geht. Ohne langen Mailverkehr kommen wir auch am Telefon zu verbindlichen Zusagen, was bei diesem Projekt ganz besonders wichtig war.“ Hinzu komme die Erfahrung von Mapal gerade im PKD-Bereich. Von dem umfangreichen Wissen durfte dann auch Wenzler profitieren.
Das Kombinations-Aufbohrwerkzeug mit gelöteten PKD-Schneiden und ISOWendeschneidplatten bietet maximale Stabilität und Standzeit in der Vorbearbeitung bei ausgezeichneten Oberflächenergebnissen für definierte Oberflächen. – Bild: Mapal Fabrik für Präzisionswerkzeuge Dr. Kress KG 'Verantworten' 60 Prozent der Taktzeit: Auf diesen vier Werkzeugen lag bei der Bearbeitung des Fahrschemels besonderes Augenmerk. – Bild: Mapal Fabrik für Präzisionswerkzeuge Dr. Kress KG 'Verantworten' 60 Prozent der Taktzeit: Auf diesen vier Werkzeugen lag bei der Bearbeitung des Fahrschemels besonderes Augenmerk. – Bild: Mapal Fabrik für Präzisionswerkzeuge Dr. Kress KG
Vier entscheidende Werkzeuge
Die Analyse ergab, dass die ersten vier von insgesamt 26 Werkzeugen für 60 Prozent der Taktzeit verantwortlich sind. Alle weiteren kommen nur relativ kurz zum Einsatz. Damit wusste der Werkzeughersteller den Ansatzpunkt, um die Performance nach oben zu schrauben. „Natürlich haben wir bei Mapal uns Gedanken darüber gemacht, welche Werkzeuge wir angesichts der niedrigen Stückzahlen einsetzen“, erläutert Igor Ivankovic, Component Manager Chassis & Brakes. „Da sich bei einzelnen Bearbeitungen die Schnitte doch zu langen Wegen addierten, führte kein Weg an PKD vorbei.“