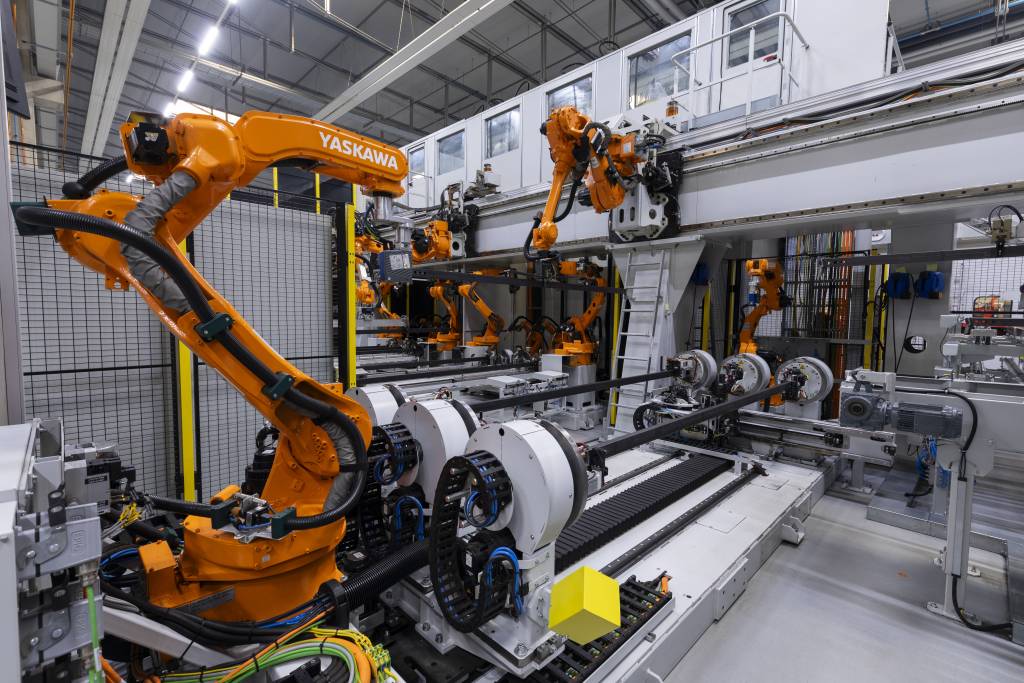
Mit den 500 Systembauteilen des Peri-Up-Gerüstbaukasten sollen Fassaden-, Industrie- und Ingenieurgerüstbauer nahezu alle Anwendungen des modernen Gerüstbaus abdecken können. In der Fertigung legen moderne Verfahren und ein hoher Automatisierungsgrad die Grundlage für hohe Qualität und Effizienz. Im bayrisch-schwäbischen Günzburg hat das Unternehmen ein neues Leitwerk aufgebaut und die komplette Herstellung für den Gerüstbaukasten gebündelt. Über hundert Motoman-Roboter von Yaskawa sind dort bereits seit 2016 im Einsatz.
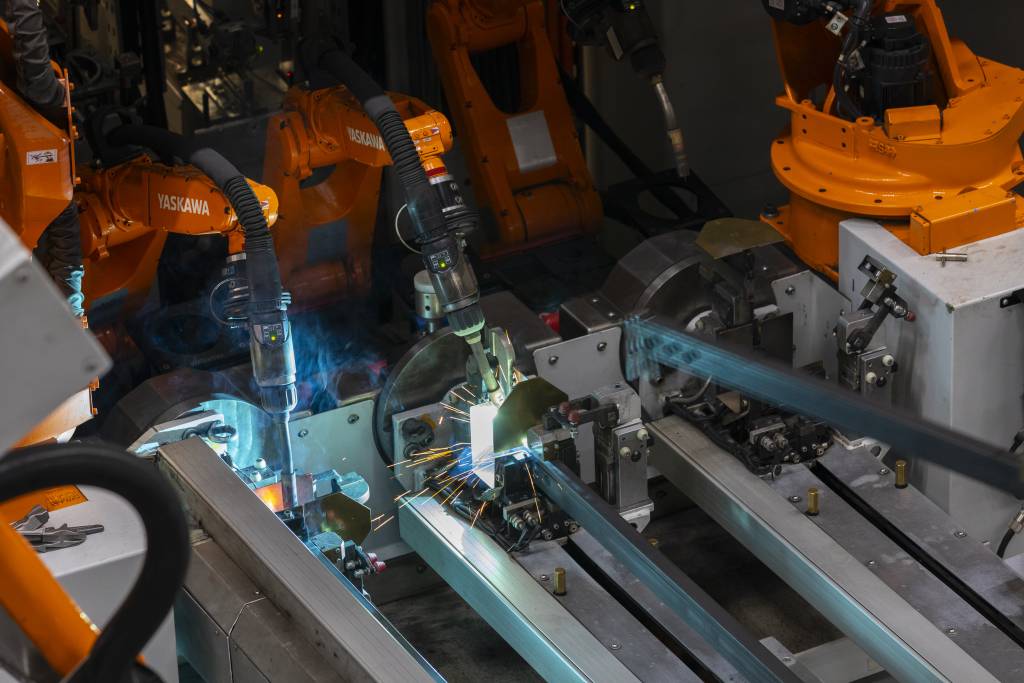
Vollautomatische Horizontalriegel-Schweißanlage
Jetzt kamen noch einmal 18 neue Yaskawa-Roboter in einer groß dimensionierten Schweißanlage hinzu. Ihre Aufgabe: die vollautomatische Fertigung so genannter Horizontalriegel, die im Gerüstbau hunderttausendfach gebraucht werden. Bewegliche Keile gewährleisten einen ebenso komfortablen wie sicheren Aufbau. Gleichzeitig stellen sie hohe produktionstechnische Anforderungen. Durch die integrierten Keile erlaubt die Konstruktion der Bauteile nur sehr kleine Toleranzen. Sie müssen daher sehr präzise ausgeführt werden. Bisher erfolgte die Fertigung teilautomatisiert auf einem halben Dutzend Roboterschweißanlagen mit Drehtisch und manueller Zuführung. „Das ging zwar auch“, blickt Stephan Schraml, Leiter Technologie-Center im Günzburger Werk, „aber mit deutlich höheren Taktzahlen, mehr Logistikaufwand und weniger Flexibilität in Bezug auf die Bauteilgrößen.“
Die neue Horizontalriegel-Schweißanlage übernimmt nun den kompletten Herstellungsprozess, von den einzelnen Rohteilen, zum fertigen Bauteil inklusive 100-prozentiger Schweißparameterüberwachung, optischer Nahtkontrolle durch Kameras sowie Längen- und Winkelmessungen. Das abschließende Palettieren zum Weitertransport erfolgt dabei genauso vollautomatisch wie der gesamte Anlagenbetrieb. Pro Schicht ist nur ein Bediener zur Überwachung der Abläufe notwendig.
Durch die parallele Nutzung von mehreren Schweißstationen kann die Anlage über tausend Riegel pro Schicht fertigen. Die Konzeption der Anlage folgte den Peri-Vorgaben bei möglichst guter Flächenausnutzung. Erst die Umsetzung verschiedener Roboteranordnungen, etwa der Einsatz von Gantry-Systemen, erlauben die sehr komplexe aber kompakte Bauweise. Softwareseitig sorgt die Sicherheitssteuerung FSU von Yaskawa für einen sicheren kollisionsfreien Ablauf der sich überschneidenden und oft parallelen Roboterabläufe. Die Steuerungstechnik fand auf einer Galerie über der Bauteilzuführung ihren Platz.
Komplexe Abläufe
Die Grundprofile werden über Rungen der Anlage vollautomatisch zugeführt, wo diese im nächsten Arbeitsschritt vereinzelt, signiert und vermessen werden. In einer weiteren Station werden die Bauteile Riegelkopf und Keil von Handling-Robotern zugeführt. Nach dem Fügeprozess von Keil und Riegelkopf wird der Riegelkopf mittels MAG-Verfahren verschweißt und in der Folge die Schweißnahtqualität inline geprüft. Neben den groben Schmiedetoleranzen der Riegelköpfe und Keile besteht die größte Herausforderung in der Handhabung der unterschiedlichen Profillängen, die in einem Spektrum zwischen 250 und 3.000mm liegen. Anlagentechnisch werden die unterschiedlichen Bauteillängen durch automatische Greiferwechselsysteme bedient. Zur einfachen Anlagenbedienbarkeit und Übersicht werden alle relevanten Prozess- und Systemdaten auf einer kundenindividualisierten, von Yaskawa entwickelten, digitalen Plattform in Form eines Dashboards auf einem Zentralmonitor dargestellt.
Handhabung und Schweißen
Insgesamt arbeiten in der neuen Anlage bei Peri 18 Roboter Hand in Hand zusammen: sechs präzise Motoman-Schweißroboter vom Typ MH5LS mit jeweils 5kg Tragkraft und weitere zwölf MH-Roboter im Taglastbereich bis 180kg. Letztere übernehmen die vielfältigen Aufgaben bei Zuführung und Handhabung, zwei davon tragen die Kamerasysteme zur automatischen Bauteilkontrolle. Die komplette Anlage wurde von Yaskawa geplant und gebaut. Durch die Systemkompeten konnten auch in der Inbetriebnahmephase alle Aufgaben rund um die neue Horizontalriegel-Schweißanlage im Werk Günzburg gelöst werden. „Die Anlage ist sehr komplex und anspruchsvoll, doch inzwischen läuft sie nahezu störungsfrei“, fasst Schraml zusammen.