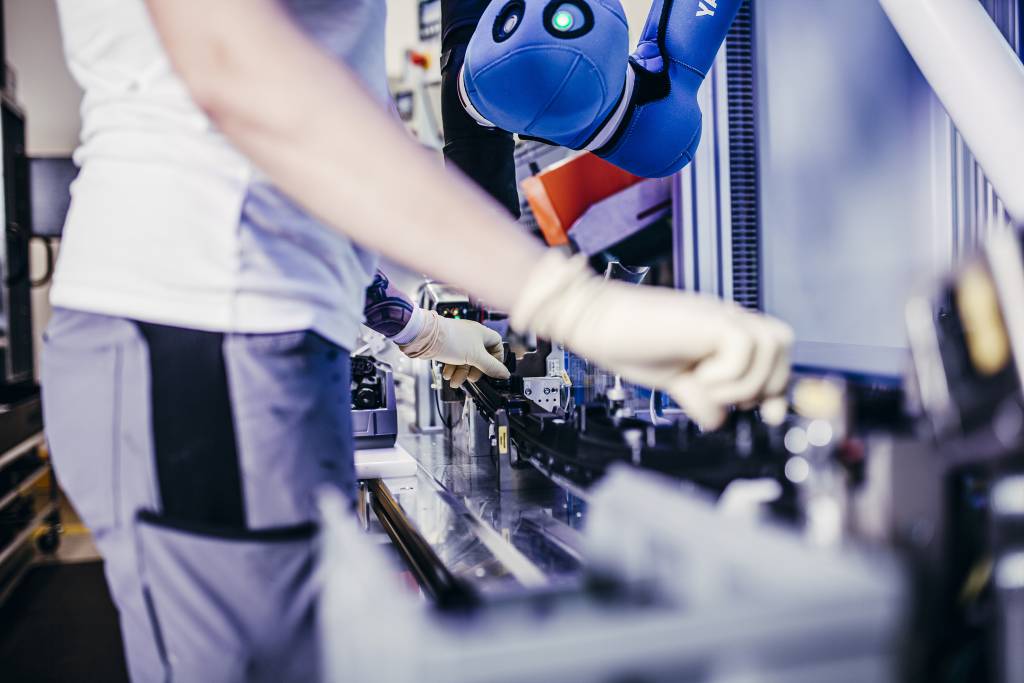
Der Trend zum Einsatz von Leichtbaurobotern für die Mensch/Roboter-Kollaboration rief auch bei ZKW, einem österreichischen Hersteller von Lichtsystemen für die Automobilindustrie, den hauseigenen Maschinen- und Anlagenbau auf den Plan. Allerdings wollten die Robotik-erfahrenen Techniker einen Cobot nicht ausschließlich für kollaborative Anwendungen oder gar nur zum Experimentieren einsetzen. Vielmehr hatten sie von Anfang an das klare Ziel vor Augen, mit einer echten kollaborativen Anwendung die Wirtschaftlichkeit in der Fertigung zu steigern und gleichzeitig die menschliche Arbeitskraft zu entlasten.
Der Schraubprozess bei der Montage des LED-Leuchtenbands für einen Elektro-SUV der Oberklasse erschien aufgrund der zu erwartenden Stückzahlen und der Komplexität der Montage als geeignetes MRK-Pilotprojekt. Für das erforderliche Sicherheitskonzept holte man sich Pilz Österreich ins Boot. Die Pilz-Mitarbeiter standen von der normgerechten Risikobeurteilung bis zur abschließenden Validierung und CE-Konformitätserklärung mit Rat und Tat zur Seite. Das Ergebnis kann sich sehen lassen: Die sichere Zusammenarbeit mit dem Roboter erspart an der Montagestation den auf Dauer anstrengenden Einsatz eines Handschraubers, beschleunigt den Prozess um rund 20 Prozent und sichert eine gleichbleibend hohe Fertigungsqualität.
Die ZKW Group, die seit 2018 zum südkoreanischen LG-Konzern gehört, hat sich auf die Entwicklung und Produktion von Premium-Lichtsystemen und Elektronikmodulen für Fahrzeuge spezialisiert und ist als Systemlieferant Partner der Automobilindustrie. Die Unternehmenszentrale inklusive Entwicklung und Produktion befindet sich in Wieselburg. Um in einem Hochlohnland wie Österreich entwickeln und produzieren zu können, ist Innovation unerlässlich. Dementsprechend sind die mehr als 80 Mitarbeiterinnen und Mitarbeiter im hauseigenen Maschinen- und Anlagenbau von ZKW gefordert, einerseits Potenziale für effizientere Prozesse u.a. durch den Einsatz moderner Automatisierungstechnik zu finden und andererseits dabei stets den Return-of-Investment im Auge zu behalten. Die meisten Montageanlagen im Werk Wieselburg wurden in Eigenregie entwickelt und gebaut.
„Wir haben uns überlegt, für welche Aufgaben in unserer Produktion ein Cobot hilfreich und vor allem wirtschaftlich sinnvoll sein könnte“, erzählt Projektleiter Christian Blamauer. „Nach eingehender Analyse sind wir zu dem Schluss gekommen, dass der Schraubprozess geeignet ist – nicht zuletzt, weil unsere Produkte häufig verschraubt werden und ein wirtschaftlicher Erfolg des Coboteinsatzes daher einen Kopiereffekt haben könnte.“
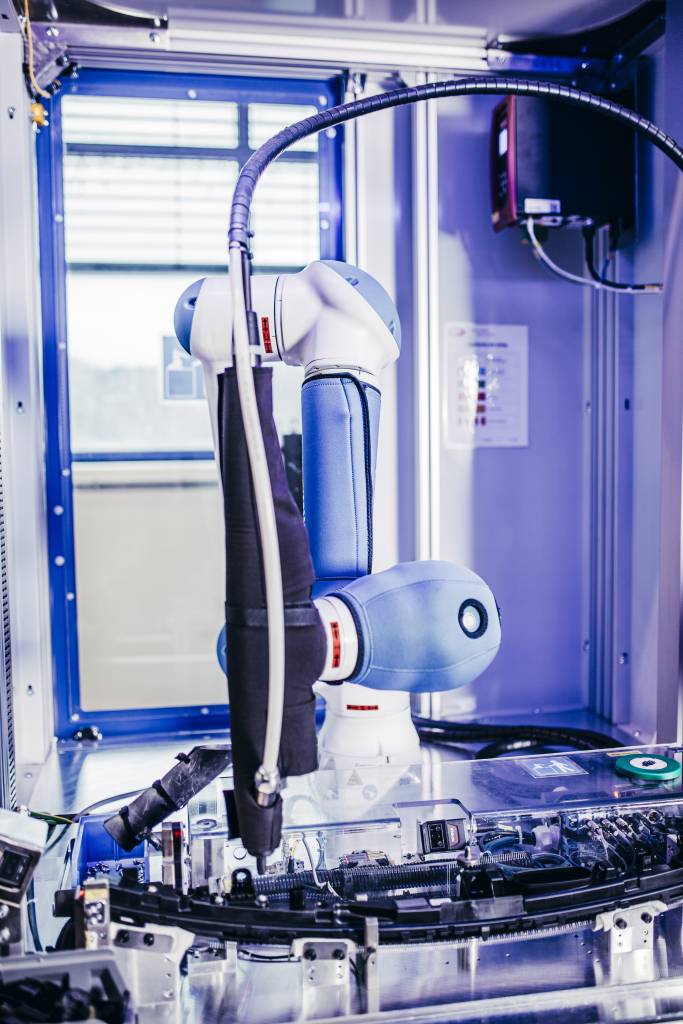
Eigene Schraubspindel als Herz der Lösung
Der Zufall wollte es, dass ZKW fast zeitgleich mit der Cobot-Idee den Auftrag erhielt, das LED-Leuchtenband für einen neuen Elektro-SUV zu fertigen. Unter der Motorhaube angebracht, verbindet das Leuchtenband die beiden Frontscheinwerfer und sorgt so für eine besondere Ästhetik. Das Leuchtenband besteht aus mehreren Einzelteilen, die durch insgesamt neun Verschraubungen miteinander verbunden sind.
„Aufgrund der geplanten Stückzahlen und der damit verbundenen Taktung wäre eine Vollautomatisierung des Montageprozesses nicht sinnvoll gewesen – die Verschraubung hätte daher in einer konventionellen Montagestation mit einem manuell geführten Handschrauber erfolgen müssen“, erklärt Blamauer. Parallel zu den Musteraufbauten für das neue Produkt tüftelten die ZKW-Anlagenbauer an der immer konkreter werdenden Cobot-Anwendung.
Als überraschender Knackpunkt erwies sich die Schraubspindel, denn: „Ursprünglich dachten wir, dass der Schraubprozess mit den am Markt verfügbaren kollaborierenden Schraubspindeln für Roboter relativ einfach umzusetzen wäre“, blickt Blamauer zurück. „Allerdings kamen wir damit nicht an die Schraubstelle des Leuchtengehäuses heran. Deshalb haben wir uns daran gemacht, eine eigene Schraubspindel zu entwickeln, die es so noch nicht gab und die wir auch zum Patent angemeldet haben.“ Was so einfach klingt, erforderte viele Stunden Engineering – vor allem die Kombination der von oben kommenden Spindel mit der seitlichen Eingriffsmöglichkeit per Hand und der damit verbundenen potenziellen Klemmgefahr erforderte Lösungskreativität. Und daran mangelt es Blamauer und seinem Team ebenso wenig wie am nötigen Ehrgeiz: „Unsere Lösung: Die Spindel klappt bei Kontakt mit der menschlichen Hand seitlich weg. Möglich macht das eine spezielle Sensorik an der Schraubspindel, die wir zu einem sicheren Signal verschalten und die dem Roboter frühzeitig – wir sagen immer, bevor es weh tut – signalisiert, dass sich die Hand im Gefahrenbereich befindet.“ Damit war der Weg frei, das von Anfang an definierte Projektziel zu erreichen: Eine echte MRK-Anwendung, die unter Einhaltung aller Sicherheitsrichtlinien und einschlägigen Normen ohne Schutzzäune oder Lichtgitter und bei üblichen Taktzeiten sicher funktioniert und darüber hinaus einen klaren wirtschaftlichen Vorteil bringt.
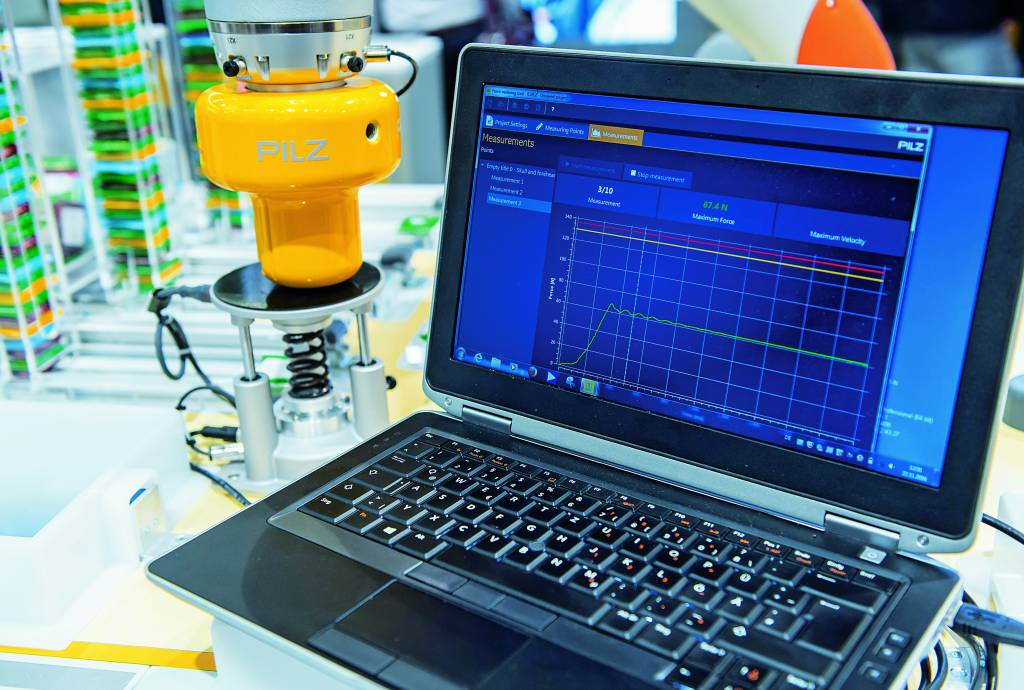
Sicherheitskonzept aufbauend auf Risikioanalyse
Schon frühzeitig informierte sich das Team bei ZKW über die sicherheitstechnischen Anforderungen, die eine solche MRK-Anwendung erfüllen muss. „Wir bauen seit Jahren Roboterapplikationen. Die Mensch/Roboter-Kollaboration und das dafür notwendige normgerechte Sicherheitskonzept waren für uns jedoch Neuland. Wie bei allen anderen Anlagen, die wir selbst entwickeln und bauen, treten wir auch bei der Cobot-Applikation als Inverkehrbringer auf und müssen daher den CE-Prozess korrekt abwickeln und mit der CE-Konformitätserklärung bestätigen“, erklärt Blamauer.
In diesem Bereich arbeitet das Unternehmen bereits seit vielen Jahren mit Pilz zusammen. “Wir setzen zahlreiche Sicherheitssensoren von Pilz ein und schätzen die Kompetenz der Pilz-Mitarbeiter. Gerade bei dem für uns neuen Cobot-Projekt macht es natürlich Sinn, einen bewährten und erfahrenen Partner an der Seite zu haben, zu dem eine entsprechende Vertrauensbasis besteht.“ Gemeinsam wurde zunächst die Risikoanalyse durchgeführt und darauf aufbauend das Sicherheitskonzept erstellt. Die mechanische Konstruktion, die elektrotechnische Planung und die gesamte Automatisierungstechnik inklusive SPS- und Roboterprogrammierung führten die ZKW-Techniker in gewohnter Manier selbst durch. Im Groben werden der gesamte Prozess sowie die Schraubspindel von der SPS mit integrierter Safety-CPU gesteuert, die Sensibilität sowie die Bewegungsabläufe des Cobots berechnet dessen eigene Robotersteuerung.
Kollisionskraft unter der Schmerzgrenze
Die Mensch/Roboter-Kollaboration stellt hohe Anforderungen an die Sicherheit, da sich Mensch und Roboter einen gemeinsamen Arbeitsraum ohne Schutzzaun teilen. Gemäß ISO/TS15066 sind bei MRK-Anwendungen der Methode 4 (ohne Schutzzaun) definierte Schmerzgrenzwerte bei einer möglichen Kollision zu berücksichtigen. Daher muss bei jeder MRK-Anwendung eine entsprechende Validierungsmessung durchgeführt werden. Im ZKW-Projekt verwendeten die Experten von Pilz das Pilz Robot Measurement System – kurz PRMS. Dabei handelt es sich um ein Kraftmessgerät mit neun unterschiedlich starken Federn, die verschiedene Körperregionen des Menschen simulieren.