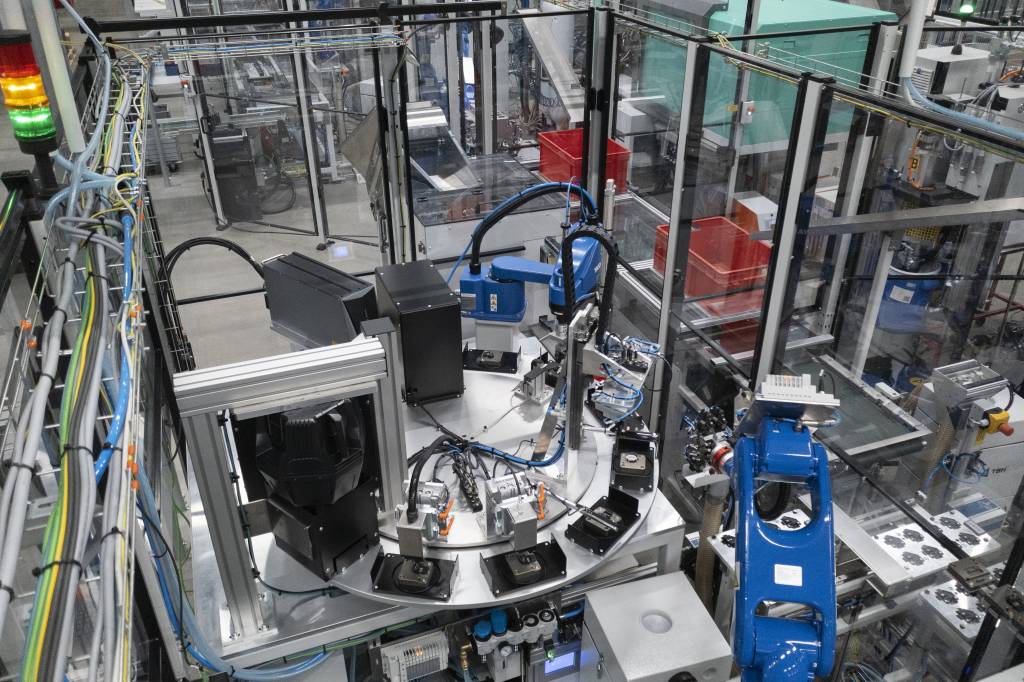
Als Zulieferer für die Automobil- und Luftfahrtindustrie beschäftigt KE Elektronik weltweit rund 3.000 Mitarbeiter. Das Unternehmen gehört zur amerikanischen Amphenol Corporation – einem Hersteller von Steckverbindern. Am Stammsitz in Kressberg-Marktlustenau produziert KE u.a. Motorlüfterstecker, die sowohl in hybriden wie rein verbrennungsmotorisch angetriebenen Fahrzeugen zum Einsatz kommen. Bei diesen Steckern handelt es sich um sogenannte Kunststoff-Hybridbauteile, bei denen vier Metallkontakte mit drei unterschiedlichen Kunststoffen umspritzt werden. „Die Herstellung dieser Stecker ist ein relativ komplexer Prozess, der an eine Vielzahl von Prüfschritten sowie eine lückenlose Rückverfolgbarkeit gekoppelt ist. Um hier der permanent steigenden Nachfrage bei dem bestehenden Fachkräftemangel gerecht werden zu können, war eine intelligente Automatisierungslösung gefragt“, so Jens Gradenegger, Teamleiter Spritzgießautomation bei KE Elektronik.
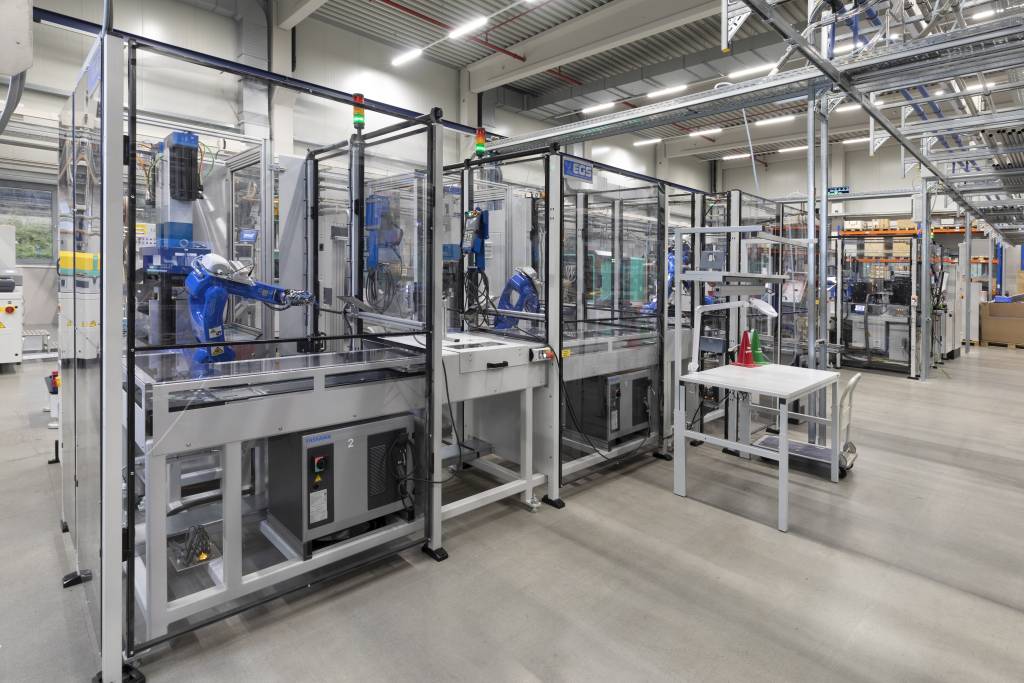
Mehrere Millionen Stecker
Mit der Maßgabe, zwei Stanz-Biege-Einheiten und zwei Spritzgießmaschinen so zu automatisieren und zu verketten, dass ein Output von mehreren Millionen Steckern pro Jahr realisiert werden konnte, wandte sich KE Elektronik an die EGS Automation aus Donaueschingen. „Wir stellen gerne unser Knowhow bei anspruchsvollen Projekten unter Beweis und hier hatten wir tatsächlich reichlich Gelegenheit dazu. In enger Zusammenarbeit mit KE ist es gelungen, auf 15 x 6m eine Fertigungsinsel zu konzipieren, die mit sechs Motoman-Robotern von Yaskawa, jeder Menge Handhabungs- und Prüftechnik und einem Sumo Ecoplex2-Palettiersystem sämtliche Anforderungen umzusetzen“ so EGS-Projektleiter Hartmut Pfalzgraf.
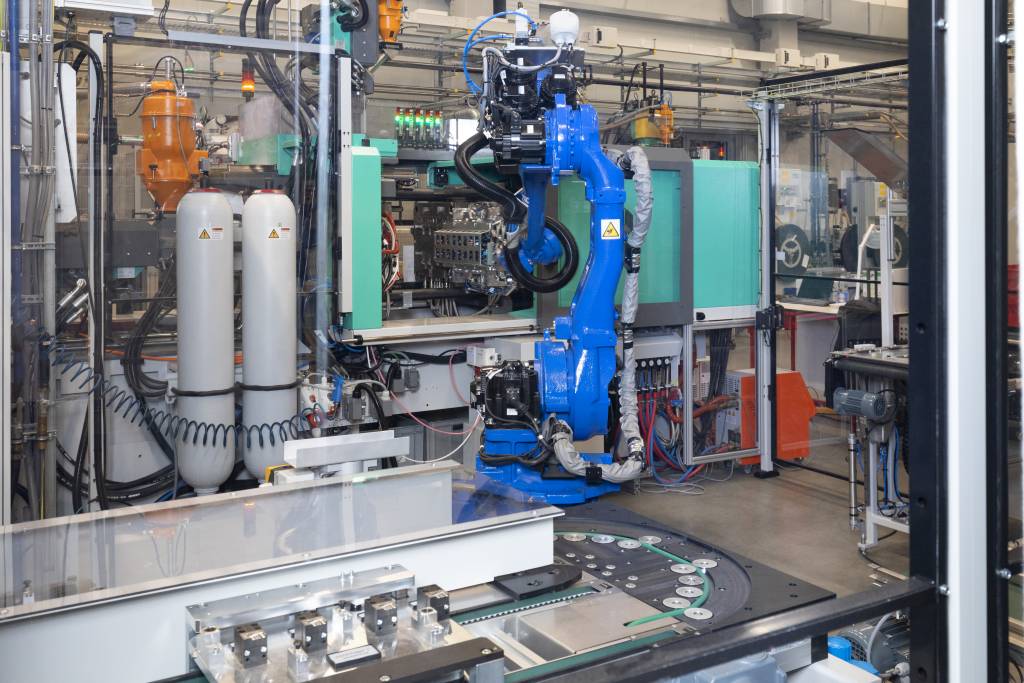
Modul I
Die komplette Linie ist in vier Module gegliedert. Im Modul I sorgen Zwei Stanz-Biege-Einheiten für die Bereitstellung der Steckerkontakte. Während auf der einen Linie Signal-Pins hergestellt werden, produziert die andere Power-Pins. An jeder Stanz-Biege-Einheit ist Yaskawa-Roboter vom Typ Motoman GP7 mit mechanischem Greifer, ausgestattet mit inte-grierter Sensorik und um 25 Grad geneigt, installiert. „Mit der Schrägstellung des Roboters ist es uns gelungen, die benötigte Drehung von der Entnahme- zur Einlegeposition komplett über die S-Achse zu realisieren, um so die Taktzeit auf ein Minimum zu reduzieren“, so Hartmut Pfalzgraf. Die beiden Sechsachser entnehmen an ihrer Linie jeweils zwei Kontakte und positionieren diese in einem Werkstückträger mit vier Aufnahmen, von der jede wiederum mit vier Kontakten bestückt werden muss. Nach vier Arbeitszyklen haben die beiden Sechsachser die vier Aufnahmen bestückt und die Werkstückträger (WT) erreichen ihre Entladeposition, an der sie ein Motoman GP50 von Modul II in Empfang nimmt.
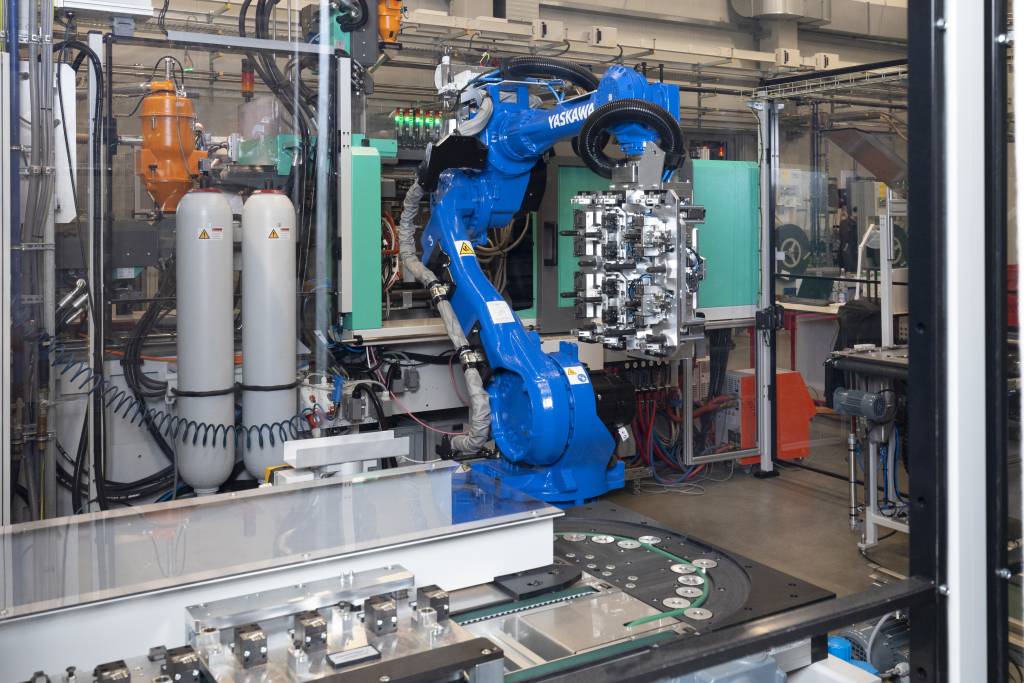
Modul II
Im Zentrum von Modul II steht eine 2K-Spritzgießmaschine (SGM) von Arburg, auf der zwei Kunststoffe gleichzeitig verarbeitet werden können. Im ersten Schritt erfolgt mit dem oberen Werkzeug der SGM eine Formumspritzung, die die Kontakte fixiert. Die Kontaktträger werden dann in einem zweiten Schritt mit dem unteren Spritzgießwerkzeug zu einem Anschlussstecker umspritzt. Alle Be- und Entladeprozesse dieser SGM übernimmt ein Yaskawa-Sechs-Achs-Roboter vom Typ Motoman GP50, an dem ein 36kg schweres Dreifach-Greifsystem Das Aufgabenspektrum des Sechsachsers ist komplex. Zunächst muss der Roboter die SGM entladen, ehe er sie mit neuen Kontakten bestücken kann. Dazu entnimmt der Roboter die fertig umspritzten Anschlussstecker aus dem unteren Werkzeug, setzt die Vorspritzlinge aus dem oberen in das untere Werkzeug um und bestückt im Anschluss das jetzt leere obere Werkzeug mit den 4×4 Stanzbiegekontakten aus dem WT von Modul I. „Um die geforderte Präzision beim Greifen erreichen zu können, dockt der Roboter vor dem eigentlichen Handhaben über einen Zentriergreifer an den Werkzeugen an. Um dennoch die Werkzeugoffenzeit möglichst kurz zu halten, reizen wir die Dynamik des GP50 komplett aus“, verrät Jens Gradenegger. Abschließend steht das Ablegen der umspritzten Stecker auf einem weiteren Werkstückträger auf dem Programm. Über ein Transfersystem gelangt dieser mit insgesamt acht Steckern von Modul II zu Modul III.