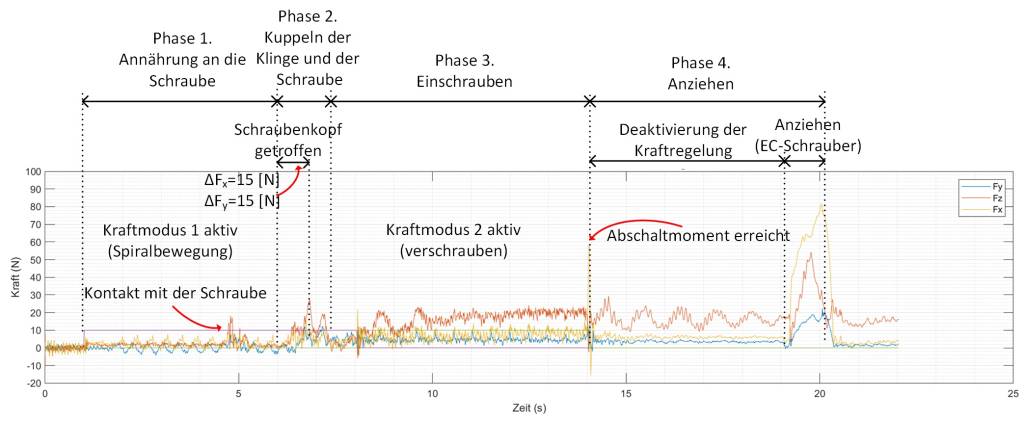
Die Fähigkeit von Werkern, Bauteile flexibel und feinmotorisch zu manipulieren, kompensiert das Fehlen einer zusätzlichen Infrastruktur, die andererseits für die Automatisierung entscheidend ist. Solche Produktionslinien zeichnen sich durch den Mangel an präziser Fördertechnik, Vorrichtungen und Werkstückträgern aus. Deshalb wird bei der Schraubmontage nur die letzte Phase des Anziehens mit industriellen elektronischen gesteuerten Werkzeugen (EC-Schraubern) automatisiert, wobei der Schrauber vom Werker gehalten wird. Hohe Prozesskräfte werden mit Hilfe von passiven Portalsystemen aufgenommen, um eine einfache Handhabung des Werkzeugs zu ermöglichen und den Werker zu schützen.

Cobots in der Montage
Konventionelle Roboterzellen benötigen viel Platz und erfordern, dass während des Betriebs keine Personen den Arbeitsbereich des Roboters betreten. Im Gegensatz dazu sind kooperative Roboter für eine enge Zusammenarbeit zwischen Mensch und Roboter ausgelegt. Cobots werden in verschiedenen Branchen eingesetzt und übernehmen Aufgaben, wie Maschinenbeschickung, Qualitätskontrolle und Fertigungsprozesse. Im Bereich der Montage beschränkt sich der Einsatz von Cobots jedoch meist auf eine kooperative Arbeitsstation, die aufgrund folgender Einschränkungen nicht für das beschriebene Szenario geeignet ist: Der Cobot befindet sich in einer festen Position und verwendet Werkstückhalter und Vorrichtungen. Die Interaktion zwischen Werker und Roboter ist in der Regel auf die Bereitstellung der Werkstücke begrenzt. Letztendlich konzentrieren sich viele verfügbare Cobot-Lösungen auf Schraubaufgaben mit niedrigem Anzugsdrehmoment ohne hohe Belastung.
Automatisierte Schraubprozesse in einer flexiblen und dynamischen Umgebung
Die Abteilung Prozessautomatisierung und Robotik am Fraunhofer IPK beschäftigt sich mit der Entwicklung von flexiblen roboterbasierten Schraubprozessen. Durch die Integration von Lösungen, wie Bildverarbeitung, Kraftregelung und KI, wird das Robotersystem mit neuen Fähigkeiten ausgestattet, um seine Aufgaben trotz externer Störungen, die durch eine für die Automatisierung ungeeignete Produktionsumgebung hervorgerufen werden, robust ausführen zu können.
Die entwickelte automatisierte Schraubstrategie ist als Mensch-Roboter-Kollaborationsszenario konzipiert, bei dem der Werker für die Positionierung des Werkstücks verantwortlich ist, während der Roboter die Einfädel- und Anzugsphase des Schraubvorgangs übernehmen kann. Das Bildverarbeitungsmodul lokalisiert die Schraube auf dem Werkstück, auch wenn dessen Position variabel ist. Die Robotersteuerung ist in der Lage, eine Online-Bahnplanung zu generieren, die kontinuierlich an die aktuelle Position des Werkstücks angepasst wird. Die Steuerung des Robotersystems verwendet dann die Kraftregelung, um die Kopplung von Werkzeug und Schraube aufrechtzuerhalten, bis die Schraube vollständig eingefädelt ist. Die Nutzung der Kraftregelung während des Schraubvorgangs führt zu einem nachgiebigen Verhalten des Robotersystems, die es ihm ermöglicht, Positionsabweichungen zwischen Werkzeug und Schraube, die durch externe Störungen aus der Umgebung entstehen, aktiv zu kompensieren. Auf diese Weise wird eine mögliche Beschädigung des Werkstücks und des Werkzeugs reduziert.
Intelligenter Schraubroboter durch Implementierung von KI
Mithilfe von künstlicher Intelligenz kann der Roboter automatisch erkennen, ob der Kontakt mit der Schraube korrekt ausgeführt wurde oder ob eine Störung aufgetreten ist. Anhand der erfassten Kontaktkräfte zwischen Werkzeug und Schraube wird der Cobot unter Laborbedingungen darauf trainiert, zu erkennen, ob die kritische Phase des Schraubvorgangs erfolgreich stattgefunden hat, das heißt, ob Werkzeug und Schraubenkopf richtig eingekoppelt sind. In naher Zukunft werden solche Algorithmen die Inbetriebnahme von Roboterschraubapplikationen erleichtern, indem nur relevante Parameter, wie z.B. Schraubentyp und Anzugsdrehmoment der Schraubaufgabe, in das Systems eingeführt werden müssen.