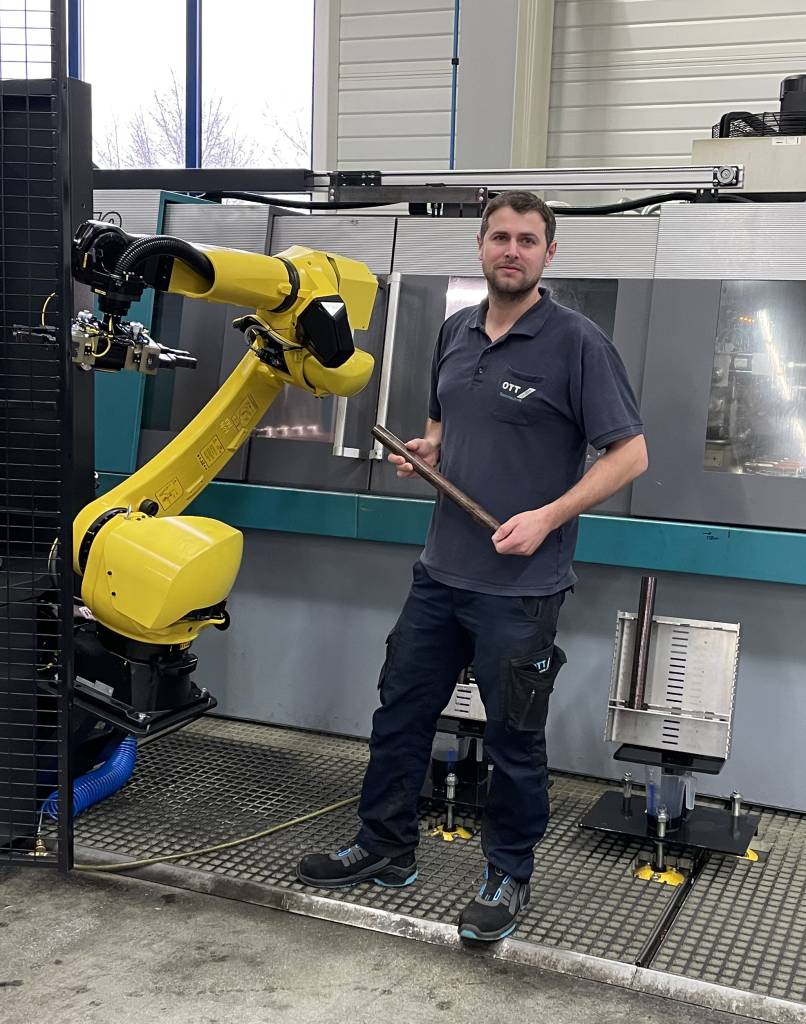
Ott-Jakob Spanntechnik mit Sitz in Lengenwang ist mit rund 250 Mitarbeitern ein weltweit führender Entwickler und Hersteller von automatischer Werkzeugspanntechnik. Als Produzent kompletter Werkzeugspannsysteme beschäftigen sich die Allgäuer zudem mit der Entwicklung und Integration intelligenter Monitoring-Systeme.
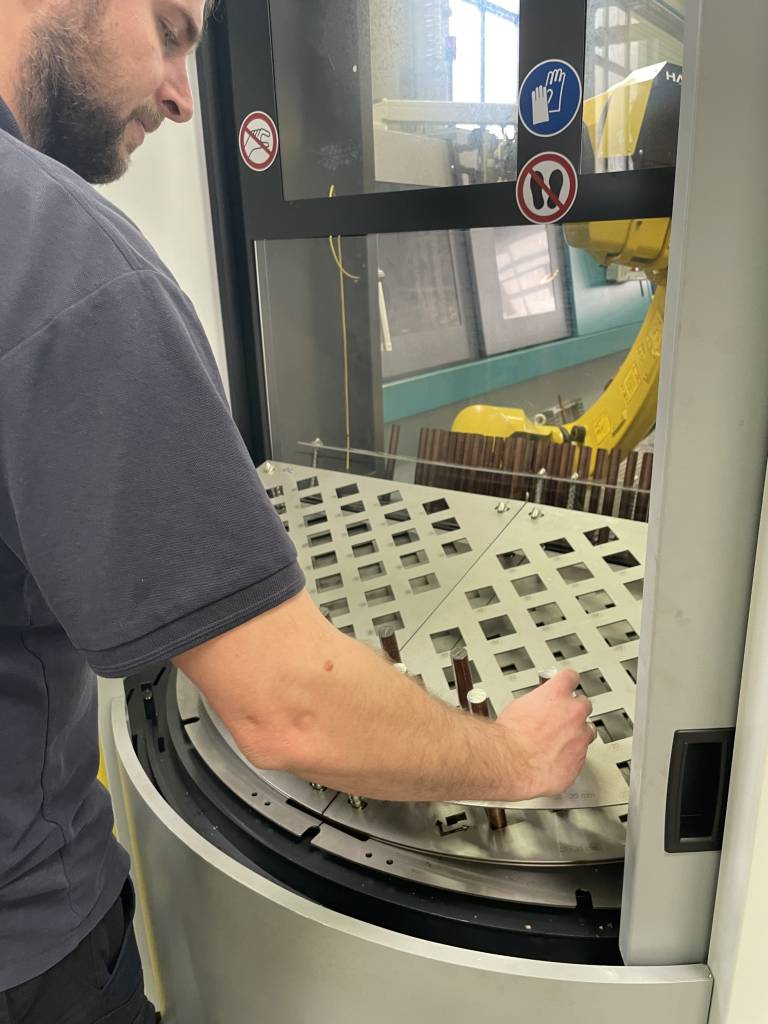
Unterschiedliche Werkstücke bohren
Bei der Fertigung ihrer Spannsysteme verarbeiten die Süddeutschen hauptsächlich hochlegierte Stähle und zu einem geringen Anteil auch Aluminium sowie Buntmetalle. „Rund 80 Prozent unserer Zweispindel-Drehmaschinen sind mit Stangenladern ausgestattet. Und wann immer wir Möglichkeiten und Potenziale sehen, automatisieren wir weitere Bestandsmaschinen“, erläutert der Teamleiter Serienfertigung Florian Hartmann. Ein gutes Beispiel hierfür ist die Tieflochbohrmaschine TBT ML250 zur Produktion von Zugstangen und Zugstangenanschlüssen. Jeweils vier Wellen werden dabei gleichzeitig mit einer Bohrung versehen. Die Dimensionen der zu bearbeiteten Werkstücke sind sehr unterschiedlich. „Die Wellen haben größtenteils Durchmesser von 20 bis 50mm und Längen von 75 bis 550mm, so Hartmann. „Innerhalb dieser Bereiche ist quasi jedes Wellenmaß möglich.“
Bisher lief die Maschine im Zweischichtbetrieb. Ein Mitarbeiter, der sich noch um weitere Anlagen kümmerte, versorgte die TBT ML250 manuell mit Rohteilen und entnahm die Fertigteile. Bei Bearbeitungszeiten zwischen 3 und 30min war das Personal gewissermaßen dauerhaft in den Fertigungsprozess mit eingebunden. „Dies war u.a. einer der Gründe, warum die Tieflochbohrmaschine automatisiert werden sollte. Zwar gab es von Marktbegleitern alternative Angebote, jedoch hat uns das Konzept von Halter überzeugt“, betont der Teamleiter.
Modifizierte Roboterzelle
Hieraus entstand ein Projekt, das mit Blick auf die Flexibilität der Roboterzelle beim Be- und Entladen einige Besonderheiten aufweist. Anders als bei den Standardlösungen belädt in diesem Fall die eigens ausgelegte Roboterzelle die Maschine nicht mit nur einem Werkstück, sondern gleich mit vier Rohteilen. Hierzu handhabt der Roboter die Wellen sowohl in axialer als auch radialer Richtung. „Daher wurde u.a. die Programmierung aller Bewegungsabläufe und somit die gesamte Roboterkinematik modifiziert und vor der Maschine eine Umgreifstation installiert“, berichtet Hartmann. Der Roboterarm selbst verfügt über einen Doppelgreifer mit werkstückspezifischen Greiferfingern.
Als Materialpuffer verfügt die Roboterzelle über eine Standardrasterplatte für Wellen mit Durchmessern zwischen 20 und 35mm sowie Längen von 75 bis 250mm, die insgesamt 176 Werkstücke aufnehmen kann. Darüber hinaus wurde eine Sonderrasterplatte für Wellendurchmesser zwischen 35 und 50mm mit einer Kapazität von 88 Werkstücken entwickelt, wobei der LoadAssistant Universal Premium 35 abweichend von seinem Standardmodell nun Bauteile mit einer Länge bis zu 550mm transportieren kann.
Prozesssicher durch Lageprüfung
2023 nahm die Roboterzelle erstmals ihren Betrieb auf. Im Dauerzyklus bereitet der Roboter die Beladung der bereits laufenden Maschine für die Bearbeitung von insgesamt vier Wellen vor, indem er jeweils ein Rohteil aus dem Werkstückpuffer nimmt und es in der Umgreifstation ablegt. Ist die Fertigung von vier Wellen abgeschlossen, entnimmt der Roboter mit einer Seite des Doppelgreifers ein Fertigteil. Hierbei prüft er zunächst die Lage des Bauteils in der Maschine, wobei er gegebenenfalls über einen in der Zelle integrierten Sensor nochmals die Länge der Welle misst, um mögliche Kollisionen beim Ablegen des Teils in der Umgreifstation zu vermeiden.